Waterproofing Ring Terminals: Structure, Challenges, & Solutions
Ring terminals are durable electrical connectors designed for water-resistant termination of wires i…….
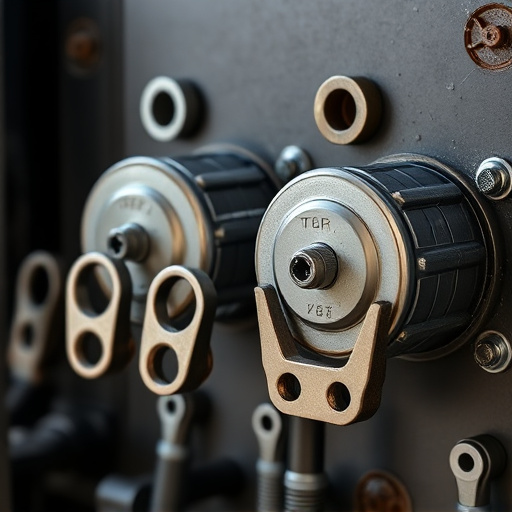
Ring terminals are durable electrical connectors designed for water-resistant termination of wires in environments with moisture exposure. Made from metal with internal threads, they're crimped or soldered onto wires and sealed with nuts to prevent water intrusion. Waterproof ring terminals enhance protection against corrosion, short circuits, and system failures in marine, automotive, and construction sectors by creating robust seals. They come in silicone-sealed and pressure-rated varieties for different environmental conditions, and proper installation and maintenance ensure reliable wiring systems.
Waterproof ring terminals are a crucial component in electrical systems exposed to moisture or wet environments. This article delves into the world of ring terminals, highlighting their basic structure and function as reliable connections. We explore why waterproofing is essential, especially in such conditions, and address common challenges faced with traditional terminals. Subsequently, various types of waterproof ring terminals available are reviewed, along with installation, selection, and maintenance tips to ensure optimal performance.
- Understanding Ring Terminals: Their Basic Structure and Function
- The Importance of Waterproofing in Electrical Connections
- Common Challenges with Traditional Terminals in Wet Environments
- Types of Waterproof Ring Terminals Available on the Market
- Selection, Installation, and Maintenance Tips for Waterproof Ring Terminals
Understanding Ring Terminals: Their Basic Structure and Function
Ring terminals are a type of electrical connection device designed for reliable and secure termination of wires in various applications, particularly where water resistance is crucial. Their basic structure consists of a metal ring with an internal thread, often made from durable materials like brass or stainless steel to ensure longevity. This ring is typically crimped or soldered onto the end of a wire, creating a robust connection point.
The function of ring terminals involves providing a way to securely fasten wires together or to electrical components while protecting against environmental factors, especially moisture. The internal threads allow for tight threading of a matching nut, ensuring a sealed joint that prevents water intrusion. This makes ring terminals an ideal choice for outdoor installations, marine applications, and any environment where exposure to water is a concern.
The Importance of Waterproofing in Electrical Connections
Waterproofing is an essential aspect when it comes to maintaining reliable electrical connections, especially in environments where moisture or water exposure is a possibility. Ring terminals, commonly used for wiring and circuit assembly, play a crucial role in ensuring such connections withstand harsh conditions. By creating a robust seal around the terminal’s contacts, waterproofing techniques prevent corrosion and short circuits caused by moisture intrusion.
This becomes particularly vital in industries like marine, automotive, or construction, where electrical components are exposed to rain, humidity, or direct water contact. Waterproofed ring terminals offer enhanced durability and reliability, ensuring the longevity of wiring systems. This simple yet effective measure can prevent costly repairs, system failures, and potential safety hazards associated with wet conditions.
Common Challenges with Traditional Terminals in Wet Environments
In wet environments, traditional terminal connections often face significant challenges. One of the primary issues is corrosion, which can lead to poor conductivity and eventually cause electrical failures. Moisture intrusion into the connection points is a common problem, especially in harsh outdoor settings or humid industrial spaces. This moisture can accelerate corrosion and compromise the integrity of the entire wiring system.
Additionally, traditional ring terminals may struggle with vibration and movement, as they are not designed to withstand these forces in wet conditions. Over time, this can result in loose connections, increasing the risk of short circuits or other electrical malfunctions. Waterproof ring terminals address these challenges by providing enhanced protection against moisture and environmental factors, ensuring more reliable and durable wiring systems.
Types of Waterproof Ring Terminals Available on the Market
When it comes to waterproof ring terminals, the market offers a variety of options designed for different applications and environmental conditions. These terminals are crucial components in industries where electrical connections need to withstand moisture or water exposure, such as marine, automotive, and construction sectors.
The two primary types available include silicone-sealed and pressure-rated ring terminals. Silicone-sealed terminals feature a soft, flexible silicone rubber compound that creates a waterproof barrier around the terminal. This type is ideal for mild to moderate water exposure conditions. Pressure-rated terminals, on the other hand, are designed for extreme environments and high-pressure applications. They use advanced sealing techniques like O-ring technology or specialized coatings to ensure maximum protection against water intrusion, making them suitable for deep-sea or high-pressure industrial settings.
Selection, Installation, and Maintenance Tips for Waterproof Ring Terminals
When selecting waterproof ring terminals, consider factors like wire size compatibility, material quality, and sealing efficiency to ensure optimal performance in wet environments. Look for terminals with high-grade stainless steel or aluminum construction, as these materials offer excellent corrosion resistance. Additionally, check that they are designed for specific applications, such as marine use or industrial settings, to guarantee adequate protection against moisture and humidity.
Installation requires careful attention to detail. Ensure proper cleaning and preparation of the cable ends before connecting them to the terminals. Tighten the terminal screws securely without over-tightening to avoid damage. Regular maintenance involves inspecting the terminals for signs of wear, corrosion, or damage. Periodically applying a layer of protective grease or sealant can help maintain their water-tightness, ensuring reliable connections even in harsh conditions.