Stainless Steel Ring Terminals: Material Insights, Application Benefits, and Maintenance Excellence
Ring terminals are robust electrical connectors predominantly made from stainless steel alloys like…….
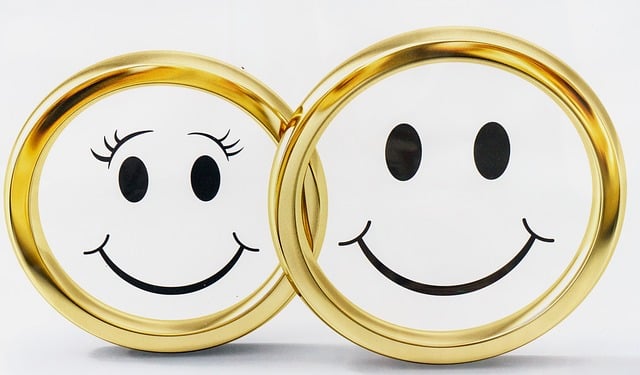
Ring terminals are robust electrical connectors predominantly made from stainless steel alloys like 304 and 316, chosen for their exceptional corrosion resistance, durability, and strength. These terminals are designed to securely join wires and cables in a variety of environments, offering mechanical support through secure clamping mechanisms alongside their electrical conductivity. Available in different sizes and specifications, they cater to diverse needs across industries, ensuring reliable connections that simplify installation without the need for additional tools. Their ergonomic design and locking elements enhance safety and reliability, making them essential components for systems that prioritize safety and enduring longevity. In particular, these terminals are invaluable in challenging settings, from industrial machinery to marine environments, due to their resistance to corrosion and adaptation to harsh conditions. Stainless steel's resilience under mechanical stress and superior electrical conductivity ensure consistent connections necessary for applications like transportation, where vehicles must function reliably across different conditions. The precision engineering of ring terminals guarantees a secure connection that withstands vehicle movement and vibration, delivering a dependable interface. The future of these components is focused on sustainability and efficiency, with smart technology integration for continuous monitoring and predictive maintenance, positioning them as indispensable in the evolution of modern technological frameworks.
Stainless steel ring terminals are indispensable components in electrical connectivity, offering durability and reliability across diverse applications. This article delves into their material properties, innovative designs, and the critical functions they serve. We explore the significance of stainless steel in ensuring robust connections and discuss factors influencing its selection over other materials. Furthermore, we provide best practices for installation and maintenance to optimize performance. Lastly, we examine cutting-edge advancements and innovations propelling the technology behind ring terminals into the future, emphasizing their application in demanding environments where resilience is paramount. Understanding these aspects equips professionals with the knowledge to harness the full potential of ring terminal technology for superior electrical connections.
- Understanding Ring Terminals: Material, Design, and Functionality
- The Role of Stainless Steel in Ring Terminal Applications
- Factors Influencing the Choice of Stainless Steel for Ring Terminals
- Installation and Maintenance Best Practices for Stainless Steel Ring Terminals
- Advanced Applications and Innovations in Stainless Steel Ring Terminal Technology
Understanding Ring Terminals: Material, Design, and Functionality
Ring terminals are robust electrical connectors designed with a hoop or ring-shaped structure, typically used at the end of wires and cables to provide a secure and reliable connection. The material selection for these terminals is critical; they are predominantly made from stainless steel due to its exceptional corrosion resistance, durability, and strength under various environmental conditions. Stainless steel, specifically alloys like 304 and 316, ensures longevity and maintains performance even in harsh settings where other materials might fail.
The design of ring terminals is meticulously engineered to cater to a wide range of applications across industries. They are available in various sizes and specifications to accommodate different wire gauges and current ratings. The functionality of these terminals extends beyond mere electrical conductivity; they also play a significant role in mechanical applications due to their secure clamping mechanism. This design not only ensures a firm grip on the conductor but also facilitates ease of installation, often without the need for additional tools. Additionally, the ergonomic shape and locking features of ring terminals contribute to their safety and reliability, making them an indispensable component in electrical systems where safety, performance, and longevity are paramount.
The Role of Stainless Steel in Ring Terminal Applications
Stainless steel ring terminals are a critical component in electrical and electronic systems, serving as robust connections between wires and various apparatuses. The inherent properties of stainless steel, such as its exceptional resistance to corrosion, make it an ideal material for environments exposed to harsh conditions like humidity, saltwater, and extreme temperatures. This resilience ensures the longevity and reliability of equipment in sectors ranging from industrial machinery to marine applications. The versatility of stainless steel also allows for customization in terms of sizes and shapes, catering to a wide array of ring terminal needs. Its ability to maintain structural integrity under varying mechanical stresses further solidifies its role as a preferred material in demanding environments where durability and performance are paramount.
In addition to their corrosion resistance, stainless steel ring terminals offer excellent electrical conductivity and thermal stability, which are essential for maintaining consistent electrical connections over time. These attributes are particularly valuable in applications where consistent performance is critical, such as in the transportation industry, where vehicles must operate under diverse conditions without fail. The manufacturing process of ring terminals involves precision engineering to ensure that they can securely clamp onto conductors, providing a reliable interface that withstands the dynamic forces encountered during vehicle maneuvers and vibrations. This reliability, combined with the material’s low maintenance requirements, makes stainless steel ring terminals indispensable in both mobile and stationary applications where longevity and consistent performance are essential.
Factors Influencing the Choice of Stainless Steel for Ring Terminals
Stainless steel ring terminals are preferred in a multitude of applications due to their superior durability and resistance to corrosion. The choice of stainless steel over other materials is influenced by several factors that dictate their performance and longevity. Firstly, the inherent strength of stainless steel provides exceptional electrical conductivity while maintaining mechanical integrity under various conditions. This is crucial for ensuring the reliability of connections in harsh environments, such as those exposed to extreme temperatures or moisture.
Moreover, the corrosion resistance of stainless steel ring terminals is a significant consideration, especially in settings with high humidity or salt exposure. The alloy content, particularly chromium, forms a protective layer that prevents rust and deterioration, ensuring the longevity of the terminal’s functionality. This property is essential for applications in marine environments, industrial machinery, and even domestic appliances where long-term performance without degradation is imperative. The choice between different stainless steel grades, such as 304 and 316, also depends on the specific demands of the application, with 316 being more resistant to pitting and crevice corrosion. Additionally, the ease of maintenance and the ability to clean and reuse ring terminals without compromising their performance further solidifies stainless steel as a superior choice for robust electrical connections.
Installation and Maintenance Best Practices for Stainless Steel Ring Terminals
When installing stainless steel ring terminals, it is imperative to adhere to proper techniques to ensure longevity and performance. Begin by carefully measuring the cable diameter and selecting a ring terminal that provides a snug yet not overly tight fit. Clean both the cable end and the interior of the ring terminal to remove any debris or residue that could impede a secure connection. Use a suitable wire stripper to precisely strip the insulation, exposing the conductor that will enter the ring terminal. Apply a small amount of dielectric grease to the conductor to protect it from corrosion and ensure a tight, stable fit within the ring. Insert the conductor into the ring terminal, ensuring that it is centered. Then, using a crimping tool appropriate for the gauge of the cable, apply even pressure around the circumference of the ring to form a secure connection. Be mindful not to over-crimp, as this can damage the wire and compromise the integrity of the connection.
For maintenance, regularly inspect stainless steel ring terminals for any signs of wear, corrosion, or looseness. In environments prone to moisture or chemical exposure, more frequent inspections are advisable. Clean terminals with a suitable cleaning solution, rinsing thoroughly with water and allowing them to dry completely before reapplication of any protective coatings or lubricants. If any connections seem loose or if there is visible damage, retighten or replace the ring terminal to maintain electrical integrity and prevent potential failures. Employing the correct tools and techniques for installation and regular maintenance will extend the lifespan of stainless steel ring terminals, ensuring they remain a reliable component in electrical systems. Regular upkeep not only safeguards against conductive failure but also contributes to the overall efficiency and safety of the system.
Advanced Applications and Innovations in Stainless Steel Ring Terminal Technology
Stainless steel ring terminals have seen significant advancements in technology, particularly in their applications across various industries. These robust and versatile components are designed to provide reliable electrical connections that can withstand harsh environments, making them indispensable in sectors such as automotive, marine, and industrial electronics. The development of high-performance alloys has led to ring terminals that offer greater resistance to corrosion and wear, ensuring longevity and reliability even under extreme conditions. Innovations in the design and manufacturing processes have resulted in more precise fitting, improved conductivity, and enhanced safety features, such as superior insulation and locking mechanisms that prevent accidental disconnections. The integration of these terminals into advanced systems is crucial for maintaining the integrity of power supply networks, which is particularly important in applications ranging from medical devices to renewable energy infrastructure.
Furthermore, the ongoing evolution of stainless steel ring terminal technology is driven by a focus on sustainability and efficiency. Manufacturers are increasingly adopting green practices, including the use of recycled materials and energy-efficient production methods. The integration of smart technology within these terminals allows for real-time monitoring and predictive maintenance, which not only extends their lifespan but also contributes to the optimization of overall system performance. As a result, stainless steel ring terminals are becoming smarter and more connected, capable of interacting with other components in an Internet of Things (IoT) ecosystem. This advancement paves the way for even more sophisticated applications, promising to further cement their role as a critical element in modern technological systems.