Ring Terminals: Optimizing Wire Gauge Compatibility & Connection Performance
Ring terminals, crucial electrical components, simplify wiring with their spring-loaded design, acco…….
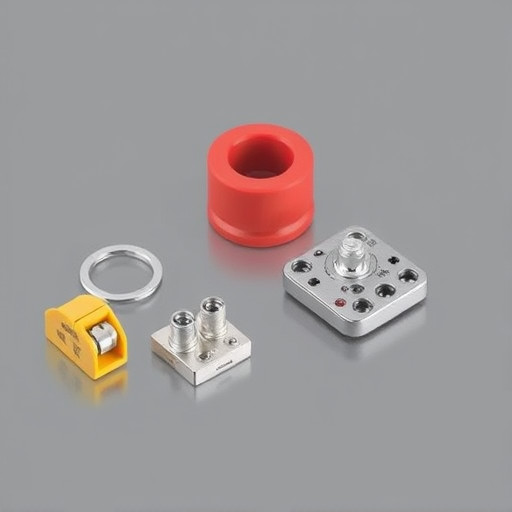
Ring terminals, crucial electrical components, simplify wiring with their spring-loaded design, accommodating diverse applications across industries. Selection of appropriate wire gauge is vital for secure connections, preventing damage and ensuring system integrity. Avoid common errors like mispairing wires and over-tightening. Best practices include using correct wire gauge per guidelines, cleaning contacts, using specialized crimping tools, and regular inspections to maintain reliable connections with ring terminals.
“In the realm of electrical connections, ring terminals serve as versatile components, offering a quick and reliable way to terminate wires. This article delves into the intricate world of ring terminal wire gauge compatibility, an essential aspect often overlooked. We’ll explore different types of ring terminals and how their selection aligns with wire gauges for optimal performance. By understanding factors like material, crimping force, and corrosion resistance, you can avoid common mistakes and ensure robust connections, making ring terminals a game-changer in any electrical project.”
- Understanding Ring Terminals: Definition and Types
- Wire Gauge Compatibility: Factors to Consider
- Common Mistakes to Avoid in Terminal Wire Pairing
- Best Practices for Ensuring Optimal Connection Performance
Understanding Ring Terminals: Definition and Types
Ring terminals, a fundamental component in electrical wiring, are specialized connectors designed for efficient and secure attachment to wires. They serve as a crucial interface between conductive wires and offer a reliable means of making electrical connections. These terminals come in various types, each tailored to accommodate different wire sizes and applications.
The definition of ring terminals extends beyond their basic function. They are characterized by a spring-loaded design that facilitates easy insertion of wires, ensuring a tight grip once inserted. This mechanism allows for quick and hassle-free wiring, making them popular among professionals and DIY enthusiasts alike. Whether it’s in automotive, marine, or industrial settings, ring terminals provide a versatile solution for connecting wires securely.
Wire Gauge Compatibility: Factors to Consider
When considering wire gauge compatibility with ring terminals, several factors come into play. First and foremost, it’s crucial to match the terminal’s current rating with the wire’s gauge and ampere (current-carrying capacity). Using a wire gauge that doesn’t meet the terminal’s specifications can lead to overloading, potential damage to the terminal, and even safety hazards.
Additionally, the type of material used in the wire and its insulation plays a role. Different materials have varying levels of flexibility and resistance to heat and chemicals, which can impact how well they fit within a ring terminal. Ensuring compatibility ensures reliable connections, prevents premature wear and tear, and maintains the overall integrity of your electrical system.
Common Mistakes to Avoid in Terminal Wire Pairing
When working with ring terminals, a common pitfall is mispairing wires based on visual similarity alone. Different gauge wires, even when colored identically, can have vastly differing electrical properties. Always verify the gauge using a tool or by consulting the manufacturer’s specifications to ensure proper pairing.
Another mistake to avoid is over-tightening terminal connections. While a secure fit is crucial, excessive tightening can damage wire insulation and even deform terminals, leading to poor conductivity and potential short circuits. Light but firm pressure is usually sufficient to make a reliable connection.
Best Practices for Ensuring Optimal Connection Performance
When working with ring terminals, best practices for ensuring optimal connection performance involve several key steps. First, always use the appropriate gauge wire for your application; using the wrong gauge can lead to poor connections and potential failures. Refer to the manufacturer’s guidelines or consult industry standards to determine the correct gauge for your specific needs. Next, ensure clean and corrosion-free contact points by thoroughly cleaning both the wire and terminal before making a connection.
Additionally, proper crimping technique is paramount. Utilize specialized crimping tools designed for ring terminals to achieve a secure, reliable hold. Avoid over-crimping, which can damage the terminal or wire, and ensure consistent pressure across the entire surface of the contact area. Regular inspection and maintenance of your connections are also crucial; check for signs of wear, corrosion, or loose fits, and address any issues promptly to maintain peak performance.