Ring Terminal Safety & Efficiency: Insulation Benefits Compared
Ring terminals are essential components that provide reliable and secure electrical connections for…….
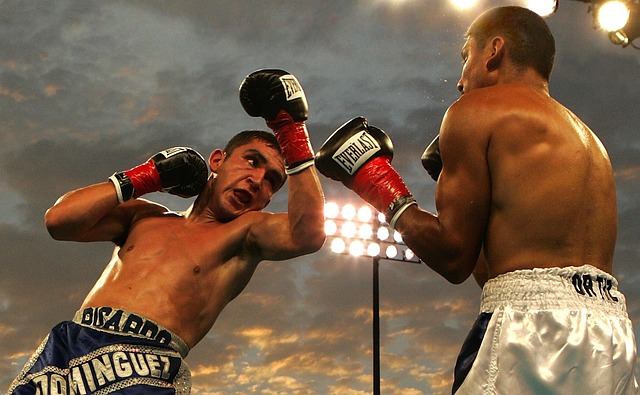
Ring terminals are essential components that provide reliable and secure electrical connections for various applications, ensuring the stability and safety of electrical installations. These terminals can be made from different materials like brass, aluminum, or stainless steel, each chosen based on factors such as temperature, corrosion resistance, and current load to suit specific environments and uses. Brass is suitable for general purposes with good conductivity and corrosion resistance, aluminum offers a lightweight alternative with high conductivity, and stainless steel provides exceptional strength and resistance for severe conditions. Ring terminals also feature robust interfaces with conductors, often reinforced by set screws or clamps to withstand vibration and thermal cycling. Insulation on ring terminals is crucial as it safeguards users and circuits from electrical risks while also protecting the connections from environmental hazards. The choice between insulated and non-insulated terminals depends on the application's requirements, with high-temperature environments favoring robust materials like rubber or PTFE for their thermal stability and chemical resistance. Insulation is key for preventing current leakage and ensuring safety and performance standards in electrical applications. Proper selection of ring terminals, considering environmental factors, voltage levels, and insulation types, is vital for maintaining safe and durable connections that comply with safety standards and regulations. Ring terminals are critical for both insulated and non-insulated setups, with the choice between them determined by the demands of the application, whether it's for safety, efficiency, or adaptability in various electrical systems.
When exploring the intricacies of electrical connections, understanding the role and differences between insulated and non-insulated ring terminals is paramount. This article delves into the materials and functions that define these components, examining their insulation properties to illuminate how they enhance safety and performance within various applications. We will compare both types, highlighting key factors that influence the choice between insulated and non-insulated ring terminals. Additionally, we’ll cover a range of use cases for each type, ensuring a comprehensive overview of their practical applications in the realm of electrical engineering. Ring terminals serve as critical connections in diverse environments, from industrial machinery to consumer electronics, making the insights provided here indispensable for professionals and enthusiasts alike.
- Understanding Ring Terminals: Materials and Functions
- Insulation Properties: Enhancing Safety and Performance
- Comparison of Insulated vs Non-Insulated Ring Terminals
- Factors Influencing the Choice Between Insulated and Non-Insulated Terminals
- Applications and Use Cases for Both Types of Ring Terminals
Understanding Ring Terminals: Materials and Functions
Ring terminals serve as critical components in electrical installations, providing secure and reliable connections to conductors’ ends. These terminal fittings are designed to ensure a solid and safe connection between wires and various apparatuses, such as motors, switches, and machinery. Made from diverse materials, ring terminals are chosen based on the application’s requirements, including environmental conditions, voltage levels, and current flow.
The choice of material for ring terminals is paramount in determining their suitability for different environments and applications. Common materials include brass, aluminum, and stainless steel, each offering distinct advantages. Brass ring terminals are renowned for their excellent conductivity and resistance to corrosion, making them ideal for general-purpose use. Aluminum alternatives are often favored due to their lightweight nature and high electrical conductivity, which is particularly beneficial in applications where weight reduction is critical. Stainless steel variants, with their unparalleled strength and superior corrosion resistance, are the preferred choice for harsh environments or where longevity is a priority. Regardless of the material selected, ring terminals must fulfill the essential functions of ensuring a secure connection that can withstand the forces encountered during operation, prevent electrical faults, and endure the environmental stresses they may face. Their design incorporates a robust interface between the conductor and the terminal body, often complemented by locking set screws or clamps to maintain integrity under vibration or thermal cycling. Understanding the role of ring terminals and the materials they are made from is crucial for ensuring that electrical connections are not only functional but also safe and durable over time.
Insulation Properties: Enhancing Safety and Performance
When selecting ring terminals for electrical applications, the insulation properties are paramount to both enhancing safety and ensuring optimal performance. Insulated ring terminals provide a protective barrier against electrical current leakage, preventing potential harm to both the user and the circuit itself. This insulation acts as a critical shield, safeguarding against environmental factors such as moisture and corrosive substances that could compromise the integrity of the connection. The quality of the insulation is influenced by factors like temperature ranges and chemical exposure the terminal will face. For instance, high-temperature environments necessitate rubber or PTFE insulation due to their excellent thermal stability and resistance to degradation. In contrast, non-insulated terminals expose conductive surfaces directly to potential hazards, making them less safe for applications where electrical shock or fire poses a risk. The choice between insulated and non-insulated ring terminals should be guided by the specific requirements of the application, including the voltage levels, current ratings, environmental conditions, and the necessary level of protection as defined by relevant standards such as IP ratings or industry-specific safety regulations. Selecting the appropriate insulation for ring terminals not only protects against electrical risks but also enhances the longevity of the terminal and the overall system’s reliability. It is essential to consider the compatibility of the insulation material with the metal used in the terminal, ensuring a secure and long-lasting connection that performs under varying conditions. Properly insulated ring terminals are an indispensable component for any electrical installation where safety and longevity are non-negotiable concerns.
Comparison of Insulated vs Non-Insulated Ring Terminals
When selecting between insulated and non-insulated ring terminals for electrical connections, it’s crucial to consider the specific requirements of your application. Insulated ring terminals are designed with a protective layer that shields the conductive elements from environmental factors such as moisture, corrosion, and abrasion. This insulation is particularly beneficial in environments where there is a risk of electrical leakage or where the equipment operates in harsh conditions. The insulation prevents accidental contact with live wires and reduces the likelihood of short circuits, making it a safer choice for both human interaction and sensitive electronic systems. Moreover, the insulating material can vary depending on the voltage requirements, ranging from rubber to silicone or thermoplastic, each offering different levels of protection and temperature resistance.
In contrast, non-insulated ring terminals are typically used in applications where the environment is controlled and the risk of electrical hazards is minimal. These terminals offer a more straightforward connection, without the added bulk or cost associated with insulation. They are ideal for use in open electrical systems where visual inspection is necessary and where the conductive path needs to be exposed. The lack of insulation also allows for better heat dissipation, which can be a critical factor in high-power applications. However, it’s important to ensure that non-insulated terminals are used under proper conditions to prevent any form of electrical mishap. Both types of ring terminals are essential components in electrical systems, and their choice should be guided by the specific needs of the application, including safety standards, environmental factors, and the desired lifespan of the connection.
Factors Influencing the Choice Between Insulated and Non-Insulated Terminals
When selecting between insulated and non-insulated ring terminals, several factors must be considered to ensure optimal performance and safety in electrical applications. The nature of the environment where the terminal will be used is a primary consideration; if the application is in areas prone to moisture or hazardous chemicals, insulated ring terminals are crucial to prevent electrical shorts and protect against corrosion. Insulation also plays a significant role in reducing electrical energy loss by minimizing resistance. This aspect becomes particularly important in applications where energy efficiency is paramount. The type of cable termination is another factor; while non-insulated terminals may suffice for certain wires, insulated ring terminals offer a more secure and weatherproof connection for others, ensuring longevity and reliability.
Additionally, the voltage and current load are critical in determining the appropriate terminal type. High voltage or current can necessitate the use of insulated terminals due to their ability to withstand greater electrical stress without degradation. The mechanical environment is also a decisive factor; insulated ring terminals can provide additional protection against abrasion, impact, and other physical forces that could otherwise compromise the integrity of the connection. Finally, regulatory compliance and standards must be adhered to, as some industries or applications may legally require insulation for safety reasons. In all these aspects, selecting the right ring terminals is essential to ensure safe and efficient electrical connections.
Applications and Use Cases for Both Types of Ring Terminals
Insulated and non-insulated ring terminals serve distinct roles in electrical connections, each with a range of applications where their unique properties are advantageous. Insulated ring terminals are crucial for settings where electrical safety is paramount. Their protective coating prevents accidental electrical discharges or short circuits by insulating the conductive core from external environments. These terminals are commonly used in household appliances, industrial machinery, and commercial lighting systems where they provide a reliable and secure connection while safeguarding against potential shock hazards. The insulation also ensures longevity of the terminal by protecting it from environmental factors like moisture, dust, and corrosive substances.
On the other hand, non-insulated ring terminals are ideal for applications where electrical safety is less of a concern but conduction efficiency and flexibility are required. These terminals are often found in settings such as farm equipment, marine vessels, or in heavy-duty industrial applications where they are subject to harsh conditions. Their design allows for easier installation and maintenance due to the absence of an insulating layer, which can be removed or damaged over time. The durability and robustness of non-insulated ring terminals make them suitable for use in environments with high humidity, extreme temperatures, or where they may come into contact with abrasive materials, ensuring reliable performance even under challenging conditions.