Ring Terminal Safety: Best Practices from Selection to Maintenance
Ring terminals are essential for reliable and safe electrical connections, particularly in industri…….
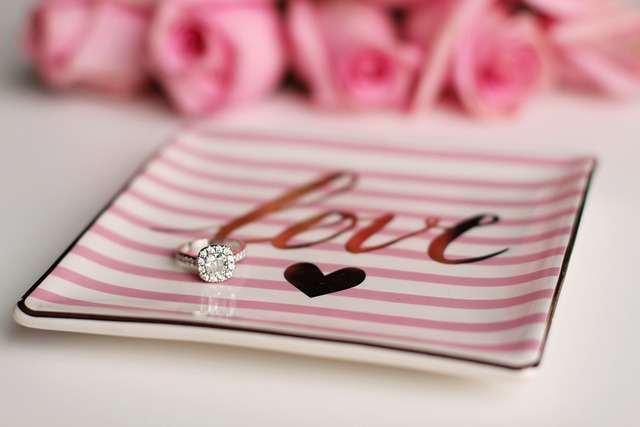
Ring terminals are essential for reliable and safe electrical connections, particularly in industrial settings where they securely terminate cables and withstand environmental stressors. The correct selection of a ring terminal, considering cable gauge compatibility, environmental conditions, and mechanical loads, is paramount for safety and functionality. Installation requires precision tools like wire stripping pliers and crimping devices to ensure electrical integrity without compromising the conductor or insulation. Adhering to the National Electrical Code and local electrical codes, along with regular maintenance and inspection, ensures that these connections remain uncorrupted and functional, safeguarding against electrical hazards and extending the lifespan of both the system and equipment. Regular checks using appropriate testing tools are necessary to maintain compliance and reliability, making ring terminals a critical component for overall electrical system safety.
When integrating electrical systems into machinery or structures, the role of ring terminals is paramount due to their durability and secure connection. This article delves into the essential safety considerations for effective ring terminal installations. From assessing environmental factors that may influence their performance to selecting the appropriate ring terminals for your application, this guide ensures a comprehensive approach to ensure safety and compliance with industry standards. We will cover the critical steps from tool selection to regular maintenance, providing a detailed roadmap for installers and engineers to guarantee the longevity and reliability of ring terminal connections.
- Understanding Ring Terminals and Their Application
- Assessing the Environmental Conditions for Safe Ring Terminal Installation
- Selecting the Correct Ring Terminal for Your Application
- Proper Tool Selection for Ring Terminal Installation
- Step-by-Step Guide to Safely Installing Ring Terminals
- Best Practices for Grounding and Bonding with Ring Terminals
- Regular Maintenance and Inspection of Ring Terminal Connections for Safety Compliance
Understanding Ring Terminals and Their Application
Ring terminals are robust, versatile components essential for the termination of cables in electrical systems. These terminal ends facilitate a secure and efficient connection between conductors and various apparatuses, ensuring reliable electrical performance. The design of ring terminals incorporates a unique shape that allows them to be tightened around a cable’s insulation, providing a clamp-like grip without piercing the conductor, which preserves the integrity of the cable’s shielding and minimizes the risk of corrosion at the termination point. This design not only enhances safety by preventing the risk of electrical arcs but also allows for easy installation and maintenance.
Ring terminals are applied across a wide array of industries, from construction to manufacturing, due to their adaptability and strength. In industrial settings, they are used to connect machinery control cables to terminals and control panels, ensuring the safe transfer of electrical current. The choice of ring terminal is critical, as it must align with the specific gauge and type of cable being used, as well as the environmental conditions in which the terminal will operate. Proper selection and installation of ring terminals are indispensable for preventing electrical hazards and maintaining the operational integrity of equipment. Understanding the correct application and maintenance of ring terminals is a cornerstone of electrical safety and system reliability. It is imperative to select the appropriate size and type of ring terminal to match the cable’s specifications and the demands of the application to ensure optimal performance and longevity.
Assessing the Environmental Conditions for Safe Ring Terminal Installation
When installing ring terminals, it is imperative to evaluate the environmental conditions where they will be used to ensure safe and effective performance. These conditions include temperature ranges, humidity levels, and exposure to chemicals or corrosive substances. Ring terminals are designed to handle electrical currents securely, connecting conductors in industrial applications. However, their functionality can be compromised if exposed to extreme temperatures that could affect the insulation material or cause a reduction in conduction efficiency. Similarly, high humidity or exposure to moisture can lead to corrosion or oxidation of metal components over time, potentially resulting in electrical resistance and increased risk of failure. It is crucial to understand the operational environment’s specific characteristics to select the appropriate type of ring terminal with the correct materials for insulation and protection against environmental factors. This proactive approach not only safeguards the integrity of the ring terminals but also contributes to the longevity and safety of the entire electrical system. Users should refer to the manufacturer’s specifications and guidelines, which often include recommendations for environmental suitability based on testing and certified performance data for different models of ring terminals. Adhering to these guidelines is essential for maintaining operational safety and preventing potential accidents or malfunctions in various industrial settings.
Selecting the Correct Ring Terminal for Your Application
When it comes to electrical installations, selecting the correct ring terminal is paramount for ensuring both safety and functionality. Ring terminals serve as critical connections between wires and various components such as switches, receptacles, and machinery. The choice of an appropriate ring terminal hinges on several factors that are specific to the application it will serve. For instance, the type of wire gauge, environmental conditions, and the mechanical load that the terminal will endure all play a significant role in determination. It is essential to consider the diameter of the conductor as per the National Electrical Code (NEC) or local electrical codes, which dictates the size of the ring terminal required for proper current flow and safety. Additionally, the operating environment can range from indoor to outdoor settings, or even harsh industrial conditions. These environments may expose terminals to moisture, chemicals, or high temperatures, necessitating the selection of materials that are resistant to such factors, like stainless steel for corrosive environments or high-temperature resistant alloins for extreme heat. Furthermore, the terminal must be compatible with the specific type of conductor insulation, whether it’s XLPE, PVC, or rubber. By carefully evaluating these aspects, installers can select ring terminals that not only provide a secure and reliable connection but also adhere to safety standards and regulations, ensuring longevity and performance of the electrical system.
Proper Tool Selection for Ring Terminal Installation
When embarking on a ring terminal installation, selecting the appropriate tools is paramount to achieve a safe and efficient outcome. The correct toolkit can make the difference between a seamless process and one fraught with difficulties. For instance, pliers designed specifically for wire stripping are essential for preparing the wires to accommodate the terminals correctly. These pliers facilitate precise cuts and removals without causing damage to the conductor or insulation, which is critical for maintaining electrical integrity. Additionally, a crimping tool tailored for ring terminal applications is crucial for a secure connection. Such tools ensure that the terminal is firmly attached to the wire, minimizing the risk of disconnection or corrosion over time. It’s important to use a tool with the correct jaw size for the gauge of wire being used to prevent mismatches that could lead to poor conductivity or potential safety hazards. Furthermore, the use of insulation displacement tools can streamline the process by inserting and forming the terminal onto the wire in one motion, ensuring a tight fit without the need for additional crimping. Proper tool selection also includes personal protective equipment such as safety glasses and gloves to safeguard the installer from electrical shocks and physical injury. By adhering to these guidelines and utilizing the correct tools, professionals can ensure that ring terminal installations are performed safely, effectively, and in compliance with industry standards.
Step-by-Step Guide to Safely Installing Ring Terminals
When installing ring terminals, adherence to safety protocols is paramount to prevent electrical hazards and ensure a reliable connection. Begin by selecting the appropriate ring terminal for the gauge of wire you are using, ensuring a secure fit. Properly strip the wire insulation, aligning the stripped length with the groove within the ring terminal. Twist the stranded wire ends around the terminal to create a solid contact, taking care not to over-tighten and damage the wire. Once the wire is secured, insert the ring terminal into the appropriate enclosure or conduit, making certain it seats properly without deformation. Use a screwdriver to secure the setscrew, tightening it against the wire until the terminal is firmly in place. The setscrew should be snug but not overly tight, as this can lead to electrical resistance and potential connection failure. Always double-check the tightness of both the ring terminal and the setscrew with a multimeter to confirm continuity. Additionally, verify that there are no sharp edges or exposed metal that could cause an electric shock or short circuit. By following these steps diligently, you can ensure a safe and efficient installation of ring terminals, essential components for reliable and safe electrical connections. Remember to follow all manufacturers’ guidelines and local electrical codes during the installation process to maintain safety and compliance.
Best Practices for Grounding and Bonding with Ring Terminals
When implementing ring terminal installations for grounding and bonding applications, adherence to best practices is paramount for electrical safety and system reliability. Ring terminals, which provide a robust connection to conductive elements, should be appropriately sized to handle the expected current and the mechanical stresses of their application. The choice of materials for both the ring terminal and the conductor must consider compatibility with the systems’ operating environment, ensuring longevity and performance under various conditions. Proper installation techniques include cleaning and preparing the conductive surface to which the ring terminal will be connected, applying a suitable dielectric lubricant if necessary, and tightening the terminal to the manufacturer’s specified torque to ensure a secure and conductive fit without overstressing the material. Additionally, care must be taken during the installation process to avoid any damage to the insulation, which could lead to future electrical failures or safety hazards.
For optimal performance, ring terminals should be installed as part of a comprehensive grounding and bonding system design that includes all conductive parts. This design must account for the system’s layout, the types of loads it will carry, and potential sources of electrical interference. The use of ring terminals in this context enhances safety by reducing the risk of corrosion or loosening over time, which can compromise the integrity of the grounding path. Regular inspection and maintenance of these installations are also crucial to ensure that they continue to perform as intended and to quickly identify any issues before they lead to system failures or pose a hazard to personnel or equipment.
Regular Maintenance and Inspection of Ring Terminal Connections for Safety Compliance
Regular maintenance and meticulous inspection are indispensable for ensuring the safety and longevity of ring terminal connections, particularly in environments where electrical systems are subjected to rigorous use or harsh conditions. The integrity of ring terminals, which serve as critical connection points between conductors and various electrical components, can be compromised over time due to factors such as corrosion, wear, and environmental influences. To maintain compliance with safety standards, it is imperative to conduct routine checks that assess the physical condition of the terminals, including their connections, tightness, and any signs of damage or degradation. This includes visual inspections for any discoloration, which may indicate overheating, as well as ensuring secure fastening to prevent loosening due to vibrations or thermal expansion.
A systematic maintenance schedule should be established and adhered to, outlining the frequency of inspections based on the specific application and environmental factors. This schedule should not only cover visual examinations but also include functional tests to verify the electrical performance of the terminals. Utilizing appropriate tools and techniques, such as insulation resistance testing and tightness verification with torque wrenches, can help identify potential issues before they lead to system failures or safety hazards. By prioritizing regular maintenance and thorough inspections, businesses and maintenance personnel can proactively mitigate risks associated with ring terminal connections, thereby safeguarding both personnel and equipment from the dangers of electrical malfunctions.