Ring Terminal Protection: Weighing Insulation Benefits for Electrical Efficiency
Ring terminals are essential components that secure and protect electrical connections, particularl…….
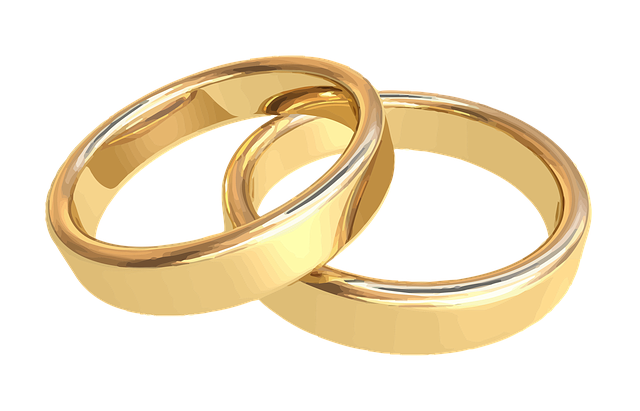
Ring terminals are essential components that secure and protect electrical connections, particularly in environments subject to temperature extremes, moisture, and chemical exposure. When insulated, they offer a shield against these elements, ensuring the integrity of the connection and preventing electric shocks or short circuits. This makes them ideal for industrial applications, automotive electronics, agricultural machinery, and any setting where durability and safety are critical. Conversely, non-insulated ring terminals provide a cost-effective solution for more benign conditions, such as residential electrical systems, where their simplicity and ease of installation contribute to the efficiency and longevity of the system. The choice between insulated and non-insulated ring terminals hinges on factors like ambient temperature, space constraints, and the potential for electrical risks, necessitating careful consideration to ensure safe and reliable electrical connections across various applications.
When electricians and engineers discuss the intricacies of electrical connections, ring terminals emerge as a pivotal component. This article delves into the critical comparison between insulated and non-insulated ring terminals. We’ll explore their distinct roles, the importance of insulation in safeguarding circuits, and the impact of environmental factors on their performance. From material selection to real-world applications, discerning professionals will gain insights to make informed decisions about which type best suits their needs. Join us as we navigate the nuances of ring terminals, ensuring a secure and efficient electrical infrastructure.
- Understanding Ring Terminals: Purpose and Functionality
- Insulation Basics: The Role of Insulation in Ring Terminals
- Comparing Materials: Types of Insulation for Ring Terminals
- Factors Influencing Insulation Selection in Ring Terminals
- The Impact of Ambient Temperature on Insulated vs Non-Insulated Ring Terminals
- Evaluating the Durability and Longevity of Insulated vs Non-Insulated Ring Terminals
- Case Studies: Real-World Applications of Insulated and Non-Insulated Ring Terminals
Understanding Ring Terminals: Purpose and Functionality
Ring terminals serve as critical components in electrical installations, ensuring a reliable and secure connection between wires and various fittings or equipment. Their primary purpose is to protect and maintain the integrity of electrical circuits by providing a durable, weatherproof enclosure for terminal connections. When selecting ring terminals, it’s crucial to consider the specific requirements of the application, including the voltage, current, and environmental conditions the terminal will encounter.
Insulated ring terminals offer enhanced protection against the elements and mechanical stress. They are designed with a robust insulating material that covers the metal ring, providing electrical insulation while also shielding the connection from physical damage. This insulation is particularly important in outdoor or industrial settings where exposure to moisture, abrasion, and corrosive substances is common. The choice between insulated and non-insulated ring terminals largely depends on the environment in which they will be used and the level of protection needed to maintain the safety and efficiency of the electrical system.
Insulation Basics: The Role of Insulation in Ring Terminals
Insulation in ring terminals plays a pivotal role in safeguarding electrical circuits and components from environmental factors and electrical hazards. When selecting between insulated and non-insulated ring terminals, understanding the basics of insulation is crucial for ensuring both safety and performance. Insulated ring terminals are designed with a protective layer that encases the conductive ring, offering a barrier against moisture, dust, and other corrosives. This insulation is particularly important in environments that are prone to harsh conditions or where there is a risk of electrical shock. The type and thickness of insulation material can vary, from rubber to thermoplastic elastomer, each with its own set of properties and temperature ratings. These materials are chosen based on the application requirements and environmental conditions the terminal will be exposed to. In contrast, non-insulated ring terminals are typically used in less demanding environments where direct electrical contact is necessary or in applications where the terminal will not be exposed to potentially damaging elements. The choice between insulated and non-insulated ring terminals should be made based on the specific needs of the application, considering factors such as the operating environment, temperature ranges, and the level of protection required against electrical hazards. Properly insulated ring terminals can extend the lifespan of electrical connections and prevent costly repairs or failures by providing a robust defense against environmental influences and accidental touches.
Comparing Materials: Types of Insulation for Ring Terminals
When selecting ring terminals, one critical aspect to consider is the type of insulation they possess. Insulated ring terminals offer enhanced protection against electrical hazards and environmental factors. They are designed with various types of materials, each serving specific purposes and providing distinct advantages. For instance, rubber insulation is commonly used for its high dielectric strength and flexibility, making it suitable for a wide range of temperatures and conditions. Ethylene Propylene Diene Monomer (EPDM) rubber, in particular, is favored for its ozone and weather resistance, ensuring longevity and reliability even in harsh environments. On the other hand, thermoplastic insulation, such as polyvinyl chloride (PVC), offers a lighter weight alternative with excellent electrical properties and chemical resistance, which is particularly beneficial in dryer or less demanding applications. The choice between these materials depends on factors like the operating environment, voltage levels, temperature extremes, and mechanical stresses that the terminals will encounter. Selecting the appropriate insulation for ring terminals not only ensures safety and performance but also contributes to the longevity and reliability of the electrical connections in various applications.
Factors Influencing Insulation Selection in Ring Terminals
When selecting insulation for ring terminals, several factors must be considered to ensure optimal performance and safety in electrical circuits. The type of environment where the terminal will be used is a primary consideration; insulation must be able to withstand the specific conditions it will face, whether that be high temperatures, extreme cold, or exposure to chemicals and corrosive substances. The voltage level at which the terminal will operate is another critical factor, as the insulation must be rated for the appropriate voltage to prevent electrical leakage or failure.
Additionally, the physical dimensions and space constraints of the application influence insulation choice. Insulation materials come in various thicknesses and can add significant size to the terminal, which may not be feasible in compact or tight spaces. The mechanical properties of the insulation, including flexibility and durability, are also essential. These must align with the movement and stress expected during the terminal’s operation to prevent damage or electrical shorts. Finally, the cost and compatibility of the insulation with the existing system components should be considered. Balancing these factors requires a thorough understanding of both the technical requirements and practical considerations to select the most appropriate insulation for ring terminals. This ensures that the terminals perform reliably over their intended lifespan and maintain the integrity of the electrical circuit they are part of.
The Impact of Ambient Temperature on Insulated vs Non-Insulated Ring Terminals
When operating in environments with significant fluctuations in ambient temperature, the choice between insulated and non-insulated ring terminals becomes critical for electrical system integrity and safety. Insulated ring terminals provide a protective barrier against extreme temperatures, which can prevent conductive losses or overheating of the conductor. This insulation is particularly important in applications exposed to harsh conditions, such as those found in industrial settings or outdoor environments. The insulation helps to maintain the electrical integrity of the circuit by preventing moisture ingress and potential corrosion, which could compromise the connection’s reliability. Additionally, the insulation ensures that the temperature within the conduit remains within safe limits, reducing the risk of fires or insulation damage due to thermal expansion.
In contrast, non-insulated ring terminals are suitable for applications where ambient temperatures are more stable and controlled. These terminals offer a cost-effective solution with a compact design, making them ideal for less demanding environments. However, their lack of insulation means they are not recommended for situations where temperature extremes are a concern. Exposure to high temperatures can cause the metal to expand and potentially weaken the connection over time, while exposure to low temperatures can increase electrical resistance and potentially lead to brittleness. Therefore, when selecting between insulated and non-insulated ring terminals, it is essential to consider the specific temperature range the device will encounter, as this will dictate the appropriate level of protection required for consistent performance and safety.
Evaluating the Durability and Longevity of Insulated vs Non-Insulated Ring Terminals
When assessing the durability and longevity of ring terminals, both insulated and non-insulated variants have distinct advantages and considerations for their application. Insulated ring terminals are designed with a protective layer that safeguards against electrical hazards and environmental factors. This insulation typically consists of thermoplastic or rubber materials, which not only extend the lifespan of the conductor but also prevent short circuits and reduce the risk of electric shock. The quality of the insulation directly impacts the terminal’s resistance to abrasion, corrosion, and exposure to extreme temperatures, ensuring a longer operational life in demanding environments.
In contrast, non-insulated ring terminals are more cost-effective due to their simpler construction. They are suitable for applications where electrical safety is less of a concern and environmental conditions are milder. The lack of insulation means that these terminals are lighter and may offer greater flexibility, which can be beneficial in certain situations. However, their durability can be compromised by exposure to moisture or harsh chemicals, potentially leading to corrosion and reduced lifespan. When selecting between insulated and non-insulated ring terminals, it is crucial to consider the specific requirements of your application, including environmental conditions, safety standards, and the potential for electrical hazards. Insulated ring terminals are often the preferred choice for long-term installations where protection against electrical risks and environmental factors is paramount, ensuring a reliable and safe connection over time.
Case Studies: Real-World Applications of Insulated and Non-Insulated Ring Terminals
In various sectors, from industrial machinery to residential electrical systems, the application of ring terminals plays a critical role in establishing reliable and safe electrical connections. Insulated ring terminals have been particularly influential in environments where moisture and chemicals are prevalent, such as in agricultural machinery or food processing plants. A case study involving their use in automated milking systems highlights their effectiveness; by providing a secure connection that remains intact despite exposure to the harsh conditions of a dairy farm, these terminals ensure the safety of both livestock and operators. The insulation prevents electrical shorts and protects against corrosion from milk and cleaning agents, extending the life of the equipment and minimizing the risk of fire or electric shock.
Conversely, non-insulated ring terminals excel in applications where environmental conditions are less extreme, such as in residential lighting fixtures or general-purpose electrical installations. A real-world application showcases their use in a standard home renovation project. Here, non-insulated ring terminals were chosen for their ease of installation and cost-effectiveness. Their robust construction ensures a secure and long-lasting connection that meets the lower demands of domestic environments. The lack of insulation allows for easier temperature dissipation and reduces overall system resistance, contributing to energy efficiency. Both types of ring terminals demonstrate their value through these case studies, highlighting the importance of selecting the appropriate terminal based on the specific application’s requirements.