Ring Terminal Longevity: Analyzing Causes and Strategies for Prevention
Ring terminals are critical components for ensuring the integrity of electrical connections across …….
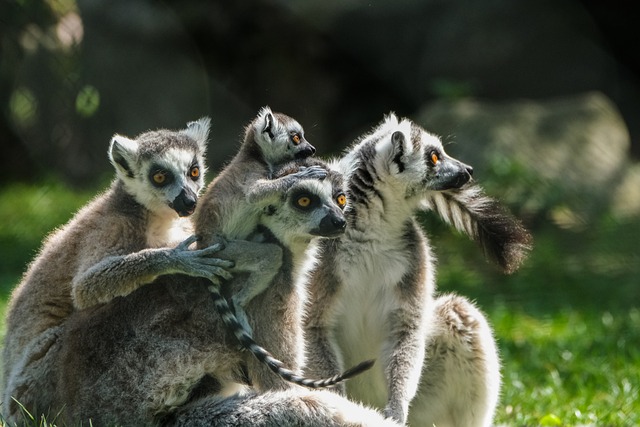
Ring terminals are critical components for ensuring the integrity of electrical connections across various sectors, from residential wiring to industrial machinery. They are constructed with robust metal materials, typically copper alloy, featuring grooves or spring-like mechanisms that secure wire connectors and insulating bushings that protect against electrical leakage and corrosion. These bushings are made from high-dielectric materials designed to endure harsh conditions and mechanical stresses. Ring terminals are engineered for durability, resisting vibration, shock, and extreme temperatures, and can be directly threaded into enclosures or conduit systems for stable connections. Available in various sizes and configurations, they accommodate different wire gauge sizes and current ratings, but proper installation following the manufacturer's specified torque is essential to maintain optimal conductivity and prevent future issues. Regular maintenance is necessary to identify and address potential problems such as bushing interface corrosion or environmental damage that could lead to terminal failure. The selection of appropriate materials, adherence to quality control, and proactive maintenance are crucial for the longevity and reliability of ring terminals within electrical systems, ensuring their performance and preventing costly system failures. Proper installation and regular inspections are vital to maintain the safety and efficiency of these critical components.
Ring terminals serve as critical connections in electrical systems across various industries, ensuring safe and efficient power transmission. However, their performance can be compromised due to a range of factors leading to failure. This article delves into the anatomy and functionality of ring terminals, identifying common causes of failure such as corrosion, material defects, and suboptimal installation practices. It also examines how load variations affect reliability, introduces advanced inspection techniques for early detection of degradation, and proposes strategies for enhancing longevity through material upgrades and design improvements. Moreover, it outlines best practices in handling, storage, and installation to prevent malfunctions, thereby safeguarding the integrity of electrical systems and minimizing downtime. Understanding these aspects is crucial for maintaining the reliability and safety of electrical circuits where ring terminals are utilized.
- Understanding Ring Terminal Anatomy and Functionality
- Common Causes of Ring Terminal Failures: A Comprehensive Overview
- – Corrosion and Environmental Factors
- – Material Selection and Quality Issues
- – Improper Installation Techniques
- Assessing the Impact of Load Variations on Ring Terminal Reliability
Understanding Ring Terminal Anatomy and Functionality
Ring terminals are critical components in electrical connections, serving as the termination points for conductors in various applications, from residential wiring to industrial machinery. A thorough understanding of their anatomy and functionality is essential for effective maintenance and prevention of failure. These terminals consist of a robust metal housing, often made of copper alloy, designed to encapsulate and protect the wire terminations. The housing typically features a groove or a spring-like mechanism that ensures a secure fit around the conductor, facilitating a reliable electrical connection. The design incorporates an insulating bushing, which separates the conductive surfaces from the terminal body, thereby preventing electrical leakage and corrosion. This bushing is usually made of a high-dielectric material that can withstand environmental factors and mechanical stresses.
The functionality of ring terminals is multifaceted. They are engineered to withstand vibration, shock, and temperature extremes, making them suitable for both stationary and mobile applications. The metal housing is often designed to be threaded directly into a variety of enclosures or conduit systems, providing a stable and durable connection. Additionally, ring terminals come in different sizes and configurations to accommodate various wire gauge sizes and current ratings. Proper installation involves tightening the terminal onto the wire to the manufacturer’s specified torque, ensuring optimal conductivity and preventing slippage or loosening over time. Regular inspection and maintenance are crucial to ensure that these terminals remain effective and to prevent potential failure points such as corrosion at the bushing interface, loose fittings due to improper tightening, or damage caused by environmental factors like UV exposure or chemical contaminants. Understanding these aspects of ring terminal anatomy and functionality is key to their reliable operation and the longevity of the systems they serve.
Common Causes of Ring Terminal Failures: A Comprehensive Overview
Ring terminals are critical components in electrical connections, serving as the interface between conductive wires and various fittings or apparatuses. Their reliability is paramount for the safe and efficient operation of electrical systems across diverse industries. Common causes of ring terminal failures can be attributed to a variety of factors, ranging from material degradation to improper installation techniques. Environmental conditions often play a significant role in premature wear and tear; exposure to harsh elements like saltwater or extreme temperatures can corrode the terminals, leading to poor connections and potential system failure. Mechanical stress, such as that from vibrations during operation or from physical impacts, can also contribute to failures by causing fatigue and eventual breakdown of the terminal’s structure.
Manufacturing defects or substandard materials can compromise the integrity of ring terminals from the outset. It is crucial for manufacturers to adhere to stringent quality control processes to ensure that the terminals meet industry standards. Additionally, it is imperative for users to follow best practices during installation, which includes using the correct size and type of terminal for the application, ensuring proper tightening without overtightening, and employing appropriate corrosion protection measures like applying anti-seize compounds or coatings as necessary. Regular inspection and maintenance are also vital to detect and address issues before they escalate into complete failures, thus maintaining the longevity and performance of ring terminals in critical electrical connections.
– Corrosion and Environmental Factors
Ring terminals are critical components in electrical connections, serving as the interface between conductors and various conduits or enclosures. Their reliability is paramount for the integrity and safety of electrical systems. One prevalent issue affecting ring terminals is corrosion, which can be attributed to environmental factors. Corrosion occurs when ring terminals are exposed to moisture, salt, dust, and other contaminants that react with the terminal materials, often resulting in degraded performance or complete failure. The type of metal used in the ring terminal construction also plays a significant role in its susceptibility to corrosion; for instance, aluminum and copper alloys may suffer from different types of corrosion under similar environmental conditions. To mitigate this risk, it is essential to select materials that are resistant to the specific environmental conditions present at the installation site. Employing corrosion-inhibitive coatings, such as zinc or tin plating, can further protect ring terminals from environmental degradation. Regular inspection and maintenance are also crucial practices to ensure the longevity of these components, as they allow for early detection and remediation of potential issues before they lead to failure. By understanding the environmental factors that contribute to corrosion and taking proactive measures, the reliability and lifespan of ring terminals can be significantly enhanced, thereby maintaining the safety and efficiency of electrical systems.
– Material Selection and Quality Issues
Ring terminal failures often stem from material selection and quality issues at their onset. The choice of material for a ring terminal is critical, as it must withstand the environmental conditions and electrical loads it will encounter during its service life. For instance, using an inappropriate material that lacks sufficient electrical conductivity or mechanical strength can lead to failure under load or exposure to harsh elements. Additionally, the quality of the material and the precision of the terminal’s manufacturing process are paramount. Substandard materials or improper manufacturing techniques can result in premature wear, corrosion, or even electrical disconnects. To prevent such issues, it is essential to select materials that meet industry standards and have proven performance records under similar conditions. Furthermore, rigorous testing and quality control measures throughout the production process are necessary to ensure that each ring terminal meets the required specifications and can reliably perform its intended function over time. Regular inspections and maintenance can also help detect potential issues before they lead to failure, thus extending the lifespan of the ring terminals and ensuring the integrity of electrical connections in various applications.
– Improper Installation Techniques
When discussing ring terminal failure, one of the primary causes is improper installation techniques. The integrity of a connection can be compromised if ring terminals are not installed correctly. This often occurs when the terminal is too loose or overtightened on conductors, leading to potential risks such as arcing, corrosion, and eventual failure. Proper technique dictates that the terminal should be snug against the conductor without deforming it. The use of the incorrect size or type of terminal for the conductor gauge can also lead to a weak connection, which may not conduct electricity efficiently and could fail under load. To prevent such issues, it is crucial to adhere to manufacturer specifications and industry standards when installing ring terminals. Training personnel in correct installation methods, utilizing the right tools, and ensuring that they understand the importance of proper tightening can significantly reduce the likelihood of failure. Regular inspections of installed ring terminals can also help identify potential issues before they lead to a breakdown, allowing for timely maintenance and replacement if necessary. By prioritizing the correct installation of ring terminals, industries can enhance the safety and reliability of their electrical systems, thereby preventing costly downtime and ensuring optimal performance.
Assessing the Impact of Load Variations on Ring Terminal Reliability
When it comes to electrical systems, the integrity and performance of components are paramount, especially under varying load conditions. Ring terminals, which serve as critical connections between conductors and various devices, are particularly susceptible to the effects of load variations. These variations can manifest as changes in current magnitude or frequency, and they can significantly impact the reliability of ring terminal connections. It is imperative to understand how these alterations affect the mechanical and electrical integrity of the terminals.
Load fluctuations can induce mechanical stress on the ring terminals, leading to potential degradation over time. This stress can be a result of thermal expansion and contraction or cyclical loading, which may weaken the terminal’s clamping force and increase the risk of electrical contact loss. The frequency of load changes also plays a role; frequent variations can cause fatigue in the material, potentially compromising the terminal’s ability to conduct electricity effectively. Assessing the impact of such variations requires careful monitoring and analysis of both the electrical parameters and the mechanical response of the ring terminals. By employing advanced testing methods, such as high-frequency vibration tests or thermal cycling tests, engineers can predict how different load conditions will affect terminal performance. This knowledge enables the design of more robust terminals that can withstand a wider range of operational scenarios, thereby enhancing the overall reliability and longevity of electrical systems. Regular maintenance checks and adherence to industry standards for ring terminal selection and installation are also crucial in preventing failure due to load variations. By proactively addressing these concerns, manufacturers and operators can minimize downtime and ensure consistent, reliable performance in demanding environments.