Ring Terminal Failure Prevention: Causes, Techniques, and Best Practices
Ring terminals, vital electrical connectors, require proactive care to prevent failures. Regular vis…….
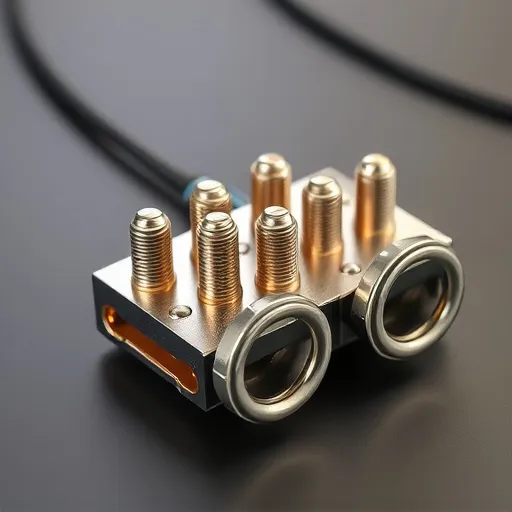
Ring terminals, vital electrical connectors, require proactive care to prevent failures. Regular visual inspections detect corrosion, damage, or loose connections. Correct cable attachment techniques minimize strain on terminals and wires. Environmental factors like moisture, humidity, and corrosive substances accelerate terminal degradation, necessitating protective measures and regular maintenance. Best practices during installation, including proper tools and adherence to guidelines, enhance reliability. Proactive maintenance, such as inspections, lubrication, and replacement, ensures ring terminals' longevity and system efficiency.
“Ring terminals, essential components in electrical systems, play a critical role in secure connections. This article delves into the intricate world of ring terminal failure causes and offers comprehensive prevention strategies. From understanding their basic structure to exploring environmental impacts, we provide a detailed analysis. Learn about visual inspection techniques, correct attachment methods, and maintenance tips for prolonging lifespan. Discover best practices for installation to prevent frequent failures, ensuring reliable electrical connections.”
- Understanding Ring Terminals: Their Role and Basic Structure
- Common Causes of Ring Terminal Failure: A Detailed Analysis
- Visual Inspection: Identifying Potential Issues Early On
- Correct Cable Attachment and Strapping Techniques
- The Impact of Environment and Corrosion on Ring Terminals
- Maintenance Strategies for Prolonged Lifespan
- Best Practices for Installation and Avoidance of Frequent Failures
Understanding Ring Terminals: Their Role and Basic Structure
Ring terminals are essential components in electrical systems, playing a crucial role in securely connecting wires and facilitating reliable power transmission. These terminals are designed with a unique ring-shaped structure that allows for easy insertion and locking of wire ends, ensuring a firm and consistent connection. The basic design consists of a metal ring with a screw or clamp mechanism, which secures the wire in place. This simple yet effective structure is commonly used in various applications, from automotive systems to industrial machinery, due to its reliability and ease of installation.
Understanding the basic function and structure of ring terminals is vital for identifying potential failure points. Over time, factors such as corrosion, excessive vibration, or improper installation can weaken these connections. Regular inspection and maintenance, along with adherence to best practices during installation, are key to preventing ring terminal failures, ensuring the overall efficiency and safety of electrical systems.
Common Causes of Ring Terminal Failure: A Detailed Analysis
Ring terminal failure is a common issue in electrical systems, often leading to costly repairs and downtime. Understanding the root causes is essential for prevention and ensuring the longevity of these critical components. Let’s explore the primary culprits behind ring terminal malfunctions.
One of the most frequent causes is poor installation practices. Inadequate tightening of connections, incorrect wire spacing, or misaligned terminals can create resistance hotspots, leading to degradation over time. Corrosion is another significant player; exposure to moisture, humidity, or corrosive substances accelerates the deterioration process, especially in harsh environments. Moreover, excessive vibration or mechanical stress on the terminal’s surface or internal pins increases the risk of failure by causing fatigue and structural damage. Some ring terminals may also be susceptible to manufacturing defects, including poor-quality materials, faulty design, or substandard machining, resulting in inherent weaknesses that manifest under load.
Visual Inspection: Identifying Potential Issues Early On
Regular visual inspections are an effective way to identify potential issues with ring terminals early on. By taking a close look at these connections, you can spot signs of damage, corrosion, or loose fittings that could lead to terminal failure. During inspection, check for any visible wear and tear, such as cracked or frayed wires, corroded surfaces, or damaged insulation. Even minor imperfections might indicate an underlying problem that, if left unaddressed, could result in electrical failures and costly repairs.
Paying attention to the color and texture of the terminals is also crucial. Discoloration, especially signs of overheating or burning, can signal a potential hazard. Furthermore, ensure that all connections are secure and properly tightened. Loosen or missing screws might suggest vibration-related issues, which could be exacerbated by high-vibration environments, leading to eventual terminal failure. Promptly addressing any visual anomalies can significantly contribute to the prevention of ring terminal failures.
Correct Cable Attachment and Strapping Techniques
Correct cable attachment and strapping techniques are paramount in preventing ring terminal failure. When connecting wires to ring terminals, it’s crucial to ensure the cable is securely fastened with appropriate tension. Over-tightening can damage the terminal or wire, while under-tightening may lead to loose connections that can easily come undone. Professionals should use specialized tools designed for this purpose to achieve a firm yet controlled attachment.
Additionally, proper strapping techniques involve wrapping straps around the bundled wires and securely fastening them at regular intervals. This not only ensures the wires stay bundled together but also distributes any strain evenly across the connection points, minimizing the risk of individual wire failure or terminal damage. Regular checks for loose straps or worn-out fasteners should be part of standard maintenance procedures to maintain reliable electrical connections.
The Impact of Environment and Corrosion on Ring Terminals
The environment plays a significant role in the longevity and performance of ring terminals, which are critical components in electrical systems. Exposure to harsh conditions like extreme temperatures, moisture, and corrosive substances can lead to premature failure of these terminals. Corrosion, in particular, is a common issue that weakens the structural integrity of ring terminals, causing them to lose their ability to create a secure connection. Over time, this can result in increased electrical resistance, overheating, and even short circuits.
Moisture intrusion and atmospheric contaminants can accelerate corrosion processes, especially in areas with high humidity or poor ventilation. Salty environments, frequently encountered near coastal regions, pose an even greater risk as salt water is highly corrosive to metals. To prevent such environmental-induced failures, proper sealing and protective coatings are essential. Regular maintenance practices, including inspecting for signs of corrosion and replacing damaged terminals, can significantly extend their lifespan in challenging conditions.
Maintenance Strategies for Prolonged Lifespan
Regular maintenance is key to ensuring the longevity and reliable performance of ring terminals, which are essential components in various industrial and electrical applications. A well-planned maintenance strategy can significantly extend their lifespan, reducing the risk of unexpected failures. One effective approach is implementing a preventative maintenance program that includes regular inspections, cleaning, and lubrication. By visually inspecting for any signs of damage, corrosion, or wear, you can identify potential issues early on. Cleaning the terminals helps maintain optimal conductivity, especially in harsh environments, preventing build-up that could lead to arcing and damage. Lubrication, where applicable, reduces friction and corrosion, ensuring smooth connections.
Additionally, staying proactive involves replacing worn-out components and keeping an inventory of spare parts. Regular maintenance also includes checking the overall condition of the terminal’s mounting hardware and ensuring proper tightening to prevent loose connections. By integrating these strategies into your operational procedures, you can effectively manage and mitigate risks associated with ring terminal failures, thereby enhancing system reliability and safety over time.
Best Practices for Installation and Avoidance of Frequent Failures
Implementing best practices during installation is paramount for preventing ring terminal failures. Ensuring proper crimping techniques, using high-quality tools and connectors, and adhering to manufacturer guidelines are fundamental steps. Proper cable management, minimizing bent or damaged wires, and regularly inspecting connections for signs of wear or corrosion also significantly reduce failure risks.
To avoid frequent failures, regular maintenance is crucial. This includes periodic checks for loose connections, corrosion buildup, and worn-out components. Utilizing protective coatings and covers for ring terminals can further shield them from environmental factors. Additionally, staying informed about industry standards and keeping up with manufacturer recommendations ensures ongoing reliability and longevity of these essential electrical connections.