Protecting Ring Terminals: Comprehensive Corrosion Prevention Strategies
Ring terminals, integral for wiring connections, are susceptible to environmental corrosion from moi…….
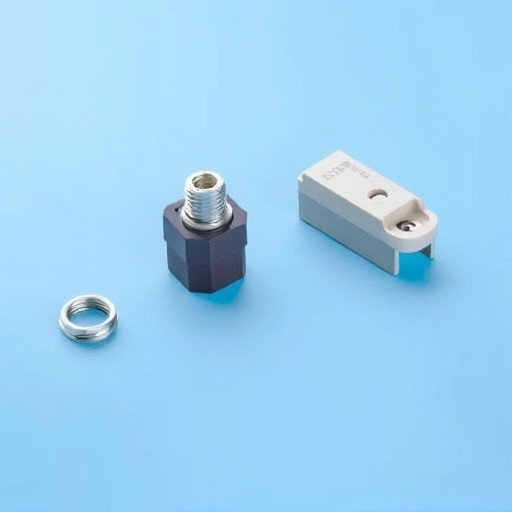
Ring terminals, integral for wiring connections, are susceptible to environmental corrosion from moisture, chemicals, and heat. This leads to circuit damage, outages, and safety risks. Effective protection is crucial for longevity in various applications, especially within the automotive industry. Chemical methods like coatings and paints (e.g., epoxy, zinc-rich) shield against moisture and chemicals, while physical barriers like silicone and rubber seal terminals from environmental harm. Proactive selection of protective measures based on local conditions and regular maintenance are vital to prevent corrosion and ensure reliable electrical connections over time.
Ring terminals, essential components in electrical systems, face significant vulnerability to corrosion, leading to performance degradation. This article delves into comprehensive protection methods for ring terminals, addressing common causes of corrosion and offering practical solutions. From chemical protection techniques to physical barriers and environmental considerations, we explore best practices ensuring long-lasting terminal durability. Discover how regular maintenance tips can safeguard your electrical connections against the ravages of time and elements, preserving the integrity of your system.
- Understanding Ring Terminals and Their Vulnerability to Corrosion
- Common Causes of Ring Terminal Corrosion
- Chemical Protection Methods for Ring Terminals
- Physical Barriers and Coatings for Enhanced Durability
- Environmental Considerations in Corrosion Prevention
- Best Practices and Regular Maintenance Tips
Understanding Ring Terminals and Their Vulnerability to Corrosion
Ring terminals, a fundamental component in electrical wiring and connectivity, serve as crucial joints, facilitating the connection between wires and components. However, despite their importance, these terminals are particularly susceptible to corrosion. This vulnerability stems from their exposure to various environmental factors such as moisture, humidity, salt air, and acidic or alkaline substances commonly found in industrial settings. Corrosion not only impacts the aesthetic appeal but more critically, it undermines the electrical integrity of the circuit, potentially leading to short circuits, power outages, and safety hazards.
The intricate design of ring terminals, with their bent-back structure, while offering secure wire retention, also provides limited protection against corrosive agents. As corrosion progresses, it can cause swelling, deformation, or even complete disintegration of the terminal, compromising the overall reliability of the electrical system. Recognizing this inherent weakness, the need for effective corrosion protection methods becomes evident to ensure the longevity and performance of ring terminals in diverse applications.
Common Causes of Ring Terminal Corrosion
Ring terminal corrosion is a common issue among automotive enthusiasts and professionals alike, stemming from several factors that contribute to its development. One of the primary causes is exposure to moisture, which can seep into the terminal’s crevices, especially in humid environments or after washing the vehicle. This moisture, combined with oxygen, initiates an electrochemical reaction, leading to oxidation and eventual corrosion.
Another significant factor is the quality of the electrical connections. Poorly fitted or dirty ring terminals can create hot spots, causing excessive current flow and localized heating. Over time, this can weaken the terminal’s metal, making it more susceptible to corrosion. Additionally, varying voltage levels, overloading, and poor grounding practices can exacerbate the issue, creating an ideal environment for corrosion to set in and eventually lead to loose connections and potential electrical failures.
Chemical Protection Methods for Ring Terminals
Chemical protection methods play a vital role in safeguarding ring terminals from corrosion, ensuring their longevity and reliability in various environments. One widely adopted approach involves applying specialized coatings that create a protective barrier against moisture, chemicals, and other corrosive elements. These coatings can be organic or inorganic, offering diverse advantages such as superior adhesion, resistance to extreme temperatures, and the ability to fill microscopic gaps, effectively preventing corrosion at its source.
Among the popular options, epoxy coatings stand out for their excellent bonding strength with metal surfaces, durability, and insulation properties. Additionally, zinc-rich paints have gained traction due to their sacrificial protection, where the zinc reacts with oxygen first, delaying the corrosion process of the underlying ring terminal. These chemical treatments not only protect against corrosion but also enhance the overall aesthetics and performance of electrical connections, making them indispensable in industries demanding robust and reliable ring terminals.
Physical Barriers and Coatings for Enhanced Durability
Physical barriers and coatings play a pivotal role in safeguarding ring terminals from corrosion, enhancing their durability, and ensuring optimal performance over extended periods. These protective layers act as a shield against environmental aggressors like moisture, salt, and chemicals commonly found in industrial settings or harsh weather conditions.
Among the popular physical barriers are silicone and rubber compounds that form a flexible, waterproof seal around the terminal. Coatings, on the other hand, offer a more comprehensive defense with options such as epoxy, polyurethane, and vinyl chloride. These coatings not only protect against corrosion but also insulate, providing electrical insulation to prevent short circuits and maintaining signal integrity.
Environmental Considerations in Corrosion Prevention
In the context of ring terminal corrosion protection, environmental factors play a significant role in the longevity and integrity of these components. Humidity, temperature fluctuations, and exposure to corrosive substances like salt water or industrial chemicals can accelerate corrosion rates, compromising the performance of electrical connections. Understanding local environmental conditions is crucial for selecting appropriate corrosion prevention methods tailored to specific applications.
For instance, ring terminals used in marine environments require robust protective coatings that resist both chemical and electrochemical attack. In contrast, those installed in industrial settings might necessitate shielding from harsh chemicals or regular maintenance routines to prevent build-up of corrosive byproducts. By considering these environmental considerations upfront, users can implement more effective corrosion protection strategies for ring terminals, ensuring reliable electrical connections over extended periods.
Best Practices and Regular Maintenance Tips
Regular maintenance is key in preventing ring terminal corrosion. Start by cleaning and inspecting your electrical connections regularly, paying close attention to any signs of wear or damage. Use a suitable cleaner to remove corrosion from the terminals and nearby components before it progresses. Applying anti-corrosion coatings or grease can provide an additional layer of protection, effectively shielding the metal from moisture and environmental factors.
Best practices involve using high-quality ring terminals designed for robust performance and longer lifespan. Ensure proper tightening during installation to maintain a secure connection that minimizes exposure to corrosive elements. Consider using terminal protection covers when not in use, especially in environments with high humidity or frequent exposure to chemicals. Regularly replacing worn-out or damaged terminals is crucial to maintaining the integrity of your electrical system.