Preventing Failures in Ring Terminal Systems: Causes, Design, and Best Practices
Ring terminals are crucial for establishing secure and efficient connections within electrical syst…….
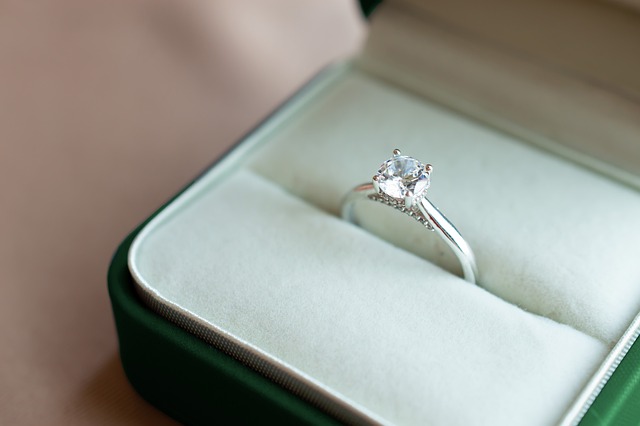
Ring terminals are crucial for establishing secure and efficient connections within electrical systems, serving as vital points where conductive wires link to various termination points. The longevity and safety of these systems depend on the integrity of ring terminals, which can be compromised by factors such as environmental degradation, mechanical wear, electrical overload, improper installation, and substandard materials. To prevent failure and extend lifespan, it is essential to adhere to industry standards, conduct regular maintenance, and follow best practices during installation. This includes rigorous testing by manufacturers to ensure their terminals meet high standards for conductivity, strength, and resistance to corrosion. By prioritizing quality control and proper installation techniques, the reliability of ring terminals can be significantly enhanced across various applications, thereby preventing safety hazards, system malfunctions, and costly repairs. Regular training for installers on correct practices, equipment suitability, and wire sizing also play a vital role in maintaining the performance and longevity of these components.
Ring terminal failures can pose significant risks to electrical systems, leading to equipment damage, safety hazards, and costly downtime. This article delves into the functional intricacies of ring terminals, shedding light on their design and the common pitfalls that lead to failure. We explore the detrimental effects of material degradation, environmental stressors, and improper installation, as well as the role of substandard components and manufacturing defects. Understanding these issues is crucial for implementing best practices in selecting and installing ring terminals. Subsequently, we outline effective preventative maintenance strategies, emphasizing routine inspections and predictive maintenance techniques. Furthermore, advancements in material science and manufacturing processes offer promising solutions to enhance the reliability and longevity of ring terminal applications. By integrating these insights, industries can mitigate failure risks and maintain optimal electrical system performance.
- Understanding Ring Terminal Functionality and Design
- Common Causes of Ring Terminal Failure
- – Material Degradation and Environmental Stressors
- – Improper Installation Techniques
- – Substandard Components and Manufacturing Defects
Understanding Ring Terminal Functionality and Design
Ring terminals serve as critical electrical connections that securely attach conductive wires to various types of ring-shaped termination points, such as those found on electrical enclosures, conduit systems, and machinery. Their functionality is centered around providing a reliable and durable connection that can withstand environmental factors and the mechanical stresses associated with industrial applications. The design of these terminals is meticulously engineered to ensure optimal performance under a range of conditions, including exposure to moisture, vibrations, and harsh chemicals.
The design of ring terminals encompasses several key components that contribute to their robustness and reliability. These include a conductive metal body, typically made from copper or aluminum alloys, which facilitates the efficient flow of electrical current. The terminals are designed with a robust contact point, often made of a high-conductivity material like silver or tin plating, ensuring a secure connection to the wire insulation. Additionally, the design incorporates a locking mechanism that ensures the terminal remains firmly attached to the wire, preventing loosening due to vibrations or thermal expansion and contraction. The insulation used in ring terminals is selected based on the operating environment, providing both electrical isolation and mechanical protection. Proper selection and application of ring terminals are paramount for the safety and functionality of electrical systems, and understanding their design intricacies is essential for preventing failure and ensuring long-term reliability.
Common Causes of Ring Terminal Failure
Ring terminals are critical components in electrical systems, serving as the point of connection between conductive wires and various termination points such as terminals or devices. The failure of ring terminals can lead to significant safety risks, system malfunctions, and costly repairs. Common causes of such failures include material degradation due to environmental factors like corrosion from exposure to moisture and salts, or mechanical wear resulting from frequent movements or vibrations during the operation of machinery. Electrical overload is another significant factor; when a wire carries more current than it is rated for, it can cause excessive heat that damages both the wire insulation and the terminal itself. Improper installation can also lead to failure; this includes tightening bolts too much, which can crush the terminals, or using incorrect sizes of conductors and terminals, leading to poor connections that may overheat and fail under normal operating conditions. Additionally, the use of substandard materials in the manufacturing process can compromise the integrity of the terminal, making it susceptible to failure under normal use. Regular maintenance and inspection, coupled with adherence to industry standards and best practices for installation, are essential for preventing these failures and ensuring the longevity and reliability of ring terminals in any application.
– Material Degradation and Environmental Stressors
– Improper Installation Techniques
When addressing the causes behind ring terminal failure, one of the primary culprits is improper installation techniques. The integrity of a ring terminal’s connection is paramount to the safety and functionality of electrical systems. A common oversight is the use of excessive force when crimping or installing the terminal onto conductors. This can lead to deformation of the terminal’s contacts, which in turn may cause poor electrical contact and eventual failure. Additionally, selecting an incorrect size ring terminal for the gauge of wire used can result in insufficient contact pressure, leading to potential resistance and overheating. It is imperative that installers adhere strictly to manufacturer guidelines and use the appropriate tools designed for this purpose. Regular training and adherence to best practices in installation can mitigate these risks and ensure a reliable connection. Emphasizing proper technique and maintaining awareness of the correct equipment and wire sizes can significantly reduce the likelihood of ring terminal failure, thus ensuring the longevity and safety of electrical systems.
– Substandard Components and Manufacturing Defects
Ring terminals are critical components in electrical connectivity systems, serving as the interface between wires and various devices or systems. The reliability of these terminals is paramount, as their failure can lead to significant safety hazards, operational disruptions, and costly repairs. Substandard components and manufacturing defects are two primary culprits behind such failures. Poor-quality materials or components can compromise the structural integrity and electrical performance of ring terminals, leading to potential risks like overheating, short-circuiting, or even electrical fires. Manufacturing defects, such as inaccurate dimensions, improper heat treatment, or poor welds, can also render ring terminals prone to failure under load or environmental stresses. To mitigate these risks, it is imperative to adhere to stringent quality control measures throughout the manufacturing process. This includes rigorous testing protocols that ensure each terminal meets or exceeds industry standards for electrical conductivity, mechanical strength, and corrosion resistance. Additionally, selecting reputable suppliers and employing advanced manufacturing techniques can significantly reduce the likelihood of substandard components entering the supply chain. By prioritizing quality and durability in the design and production of ring terminals, manufacturers can enhance safety and reliability for end-users across various industries. Regular maintenance and inspections are also crucial to extending the lifespan of these terminals and preventing failures due to wear or environmental factors.