Optimizing Wire Gauge Selection with Ring Terminal Compatibility
When selecting ring terminals for electrical applications, it's crucial to match them with the…….
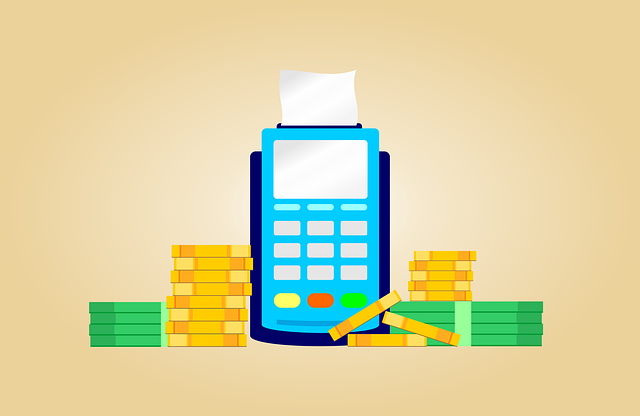
When selecting ring terminals for electrical applications, it's crucial to match them with the appropriate wire gauge to ensure safety and optimal performance. The wire gauge determines the current-carrying capacity of the circuit and must align with the ring terminal's capabilities. Thinner gauges (higher AWG numbers) are for low-current needs, while thicker gauges (smaller AWG numbers) handle high-current applications. Environmental factors like temperature and humidity, as well as mechanical stress from vibration or motion, must be considered to select materials like stainless steel when necessary. The chosen ring terminal must also accommodate the wire's diameter and insulation type without causing strain or overheating. For instance, 14-gauge wires are suitable for low-voltage lighting systems in less demanding environments, while industrial automation may require robust 12-gauge wires with heavy-duty ring terminals to endure saltwater exposure. In all cases, the wire and ring terminal must be compatible to ensure long-lasting, reliable electrical connections across different sectors, including telecommunications and marine applications. Adhering to industry standards like ANSI/NEMA IWRC and consulting manufacturer specifications are key steps in making informed choices for safe and efficient wire-to-ring terminal connections.
When delving into electrical installations, selecting the appropriate ring terminal wire gauge is paramount for ensuring safe and efficient power transmission. This article elucidates the intricacies of ring terminal wire gauge compatibility, a critical aspect of electrical engineering that underpins the functionality and longevity of your systems. We explore the factors affecting compatibility, the significance of ampacity in matching ring terminals to wire gauges, and provide a comprehensive guide for identifying the correct ring terminal size for your specific wiring needs. Through case studies and practical examples, we illustrate the real-world implications of ring terminal and wire gauge combinations, ensuring that readers can confidently apply this knowledge to their projects.
- Understanding Ring Terminal Wire Gauge Selection
- Factors Influencing Compatibility Between Ring Terminals and Wire Gauges
- The Importance of Ampacity in Matching Ring Terminals to Wire Gauges
- Identifying the Correct Ring Terminal for Your Wire Gauge
- Step-by-Step Guide to Determine Suitable Wire Gauges for Different Ring Terminals
- Case Studies: Real-World Applications of Ring Terminals and Wire Gauge Combinations
Understanding Ring Terminal Wire Gauge Selection
When selecting the appropriate ring terminal wire gauge for an electrical application, it’s crucial to consider the current requirements and the length of the wire run to ensure proper performance and safety. Ring terminals are integral components that connect wires to terminals or conductors in electrical systems, providing a secure and reliable electrical connection. The wire gauge directly influences the amount of current the circuit can safely carry; a smaller gauge (thicker wire) allows for higher current capacity but involves more resistance than a larger gauge (thinner wire). Therefore, it’s essential to select a wire gauge that matches both the electrical demand of the device or system and the physical space available within the enclosure or conduit where the ring terminal will be installed.
For instance, when working with low-voltage lighting systems, a smaller gauge such as 14 AWG (American Wire Gauge) might suffice for short distances, whereas high-current applications like those found in motors or heavy machinery may necessitate a larger gauge like 2/0 AWG for the necessary current delivery over longer distances. Additionally, environmental factors and temperature variations should be considered as they can affect resistance and wire integrity, further emphasizing the importance of an appropriate ring terminal and wire gauge combination for optimal performance and longevity of the electrical system. It’s also vital to adhere to national electrical codes and industry standards to maintain safety and compliance.
Factors Influencing Compatibility Between Ring Terminals and Wire Gauges
When selecting appropriate ring terminals for wire gauges, several factors influence compatibility and ensure safe and efficient electrical connections. The American Wire Gauge (AWG) system or its metric equivalent is a key consideration; it dictates the diameter and cross-sectional area of the wire. A wire’s gauge directly affects its current-carrying capacity and resistance, which in turn determines the appropriate ring terminal size to match the wire for a secure connection without causing excessive strain or risk of overheating.
The type of application and environment where the wire and ring terminal will be used also play a significant role in compatibility. Environmental factors such as temperature extremes, humidity, and exposure to chemicals can influence the choice of materials for both the wire and the ring terminal. For instance, if the application is in a corrosive environment, selecting stainless steel or other corrosion-resistant materials would be essential to maintain the integrity of the connection over time. Similarly, the mechanical stresses associated with the intended use, such as vibration, motion, or dynamic loading, must be considered when determining the appropriate ring terminal size and type to ensure a durable and long-lasting connection. It is also crucial to consider the electrical requirements, including voltage, current, and frequency, which can affect the choice of insulation material and the overall design of the ring terminal to prevent overheating and ensure proper conduction. Proper gauge selection is thus not just about physical fit but encompasses a comprehensive approach to ensure optimal performance and reliability of electrical connections.
The Importance of Ampacity in Matching Ring Terminals to Wire Gauges
When interfacing with electrical systems, it is imperative to ensure that ring terminals are correctly matched with the appropriate wire gauges. The concept of ampacity plays a crucial role in this process. Ampacity refers to the maximum current that a conductor can safely carry without exceeding its temperature limits. Selecting the correct ring terminal size for a given wire gauge is essential for the safe and efficient operation of electrical circuits.
Ring terminals, which serve as the termination points for conductors in various applications, must be compatible with the wire gauge to prevent potential issues such as overheating or circuit failure. The American Wire Gauge (AWG) system categorizes wire gauges based on their cross-sectional area and diameter, which directly affects their current-carrying capacity. For instance, a larger AWG number denotes a smaller and thus thinner wire, with less current-carrying ability. Conversely, a smaller AWG number indicates a thicker, stronger wire capable of handling more current. The ring terminal must be designed to accommodate the wire’s gauge securely and allow for the safe dissipation of heat generated by the electrical current. This is especially critical in high-demand environments or where electrical loads are significant, ensuring the longevity and reliability of the electrical connection. Proper ring terminal wire gauge compatibility not only protects the integrity of the system but also safeguards against potential hazards associated with overloading the circuit, making it a key consideration for engineers and technicians working in the field of electrical installations.
Identifying the Correct Ring Terminal for Your Wire Gauge
When working with electrical systems, selecting the correct ring terminal for your wire gauge is paramount to ensure a secure and efficient connection. Ring terminals serve as the termination point for ring lugs on wires, providing a reliable interface between conductors and devices or enclosures. The compatibility of the ring terminal with the wire gauge is influenced by the size and thickness of the wire insulation and the wire itself. Thinner gauges require terminals that can accommodate their smaller diameter without causing excessive compression that could lead to poor conduction or even damage the wire over time. Conversely, thicker gauges necessitate terminals that are large enough to secure the wire without slipping off but not so large that they create unnecessary space and potential for movement within the connection.
To determine the appropriate ring terminal for your specific wire gauge, consult both the ring terminal manufacturer’s specifications and the wire gauge standards. Manufacturers typically provide a compatibility chart or a list of recommended wire sizes that can be safely used with their terminals. Additionally, standards such as ANSI/NEMA IWRC (International Wiring Rules Committee) offer guidelines to assist in selecting the correct ring terminal based on the American Wire Gauge (AWG) system or similar sizing systems. By adhering to these guidelines and ensuring that the ring terminal’s inside diameter matches well with the wire gauge’s size, you can achieve a reliable and durable electrical connection, thereby preventing potential safety hazards and maintaining efficient electrical performance.
Step-by-Step Guide to Determine Suitable Wire Gauges for Different Ring Terminals
When selecting appropriate wire gauges for ring terminals, it’s crucial to consider the electrical load and the type of ring terminal used to ensure proper connections and safety. Here’s a step-by-step guide to determine suitable wire gauges for different ring terminals:
1. Determine the Current Requirements: Begin by calculating the maximum current your application will draw. This information is essential as it directly impacts the gauge of the wire needed. Higher currents necessitate thicker wires to minimize voltage drop and prevent overheating.
2. Consult Industry Standards: Refer to relevant industry standards, such as the National Electrical Code (NEC), which provide guidelines on minimum wire sizes for different applications based on the expected load. These standards are designed to ensure safety and reliability in electrical installations.
3. Select the Ring Terminal Type: Identify the type of ring terminal you will be using. Different types, like those for general use, high-temperature, or those rated for specific voltages, have compatibility with different wire sizes. Ensure that the ring terminal is rated for the voltage and current of your application to prevent failure.
4. Match Wire Gauge to Ring Terminal: After selecting the appropriate ring terminal, match it with a wire gauge that falls within the manufacturer’s specified range. The wire gauge must be able to accommodate the current without exceeding the ring terminal’s capacity or experiencing excessive voltage drop.
5. Check for Bending Radius: Verify that the wire you choose can bend to fit the ring terminal without degrading its integrity. The bending radius should be within the manufacturer’s recommendations to avoid insulation damage or copper strand breakage.
6. Conduct Insulation Rating Compatibility Check: Ensure the insulation rating of the wire is compatible with the temperature and environment where the ring terminal will be used. This step prevents insulation failure due to overheating or exposure to harsh conditions.
7. Perform a Final Verification: Finally, double-check your selections against the manufacturer’s specifications for both the wire and the ring terminal. This step confirms that you have chosen the correct wire gauge for the intended application, ensuring electrical integrity and safety.
By following these steps, you can confidently determine the suitable wire gauges for different ring terminals, ensuring your electrical connections are both safe and efficient.
Case Studies: Real-World Applications of Ring Terminals and Wire Gauge Combinations
In various sectors, including industrial automation and electrical construction, ring terminals serve as a critical component for securely terminating wires to conductive components such as pipes, cables, or enclosures. Their compatibility with wire gauges is paramount to ensure reliable connections and optimal performance under different conditions. For instance, in an automated production line, ring terminals with 14-gauge wires are frequently used for power and signal transmission between machines. The combination of the right wire gauge with the appropriate ring terminal ensures that the connection can handle the required current without overheating or failing, which is crucial for maintaining the continuity of the production process. Similarly, in telecommunication infrastructure, technicians often employ 22-gauge wires with ring terminals to connect low-voltage signaling devices. The compatibility of these fine gauges with the robustness of the ring terminal prevents signal degradation and extends the lifespan of the system.
Another real-world application is in marine environments, where saltwater and humidity can corrode standard terminals within a short period. Here, heavy-duty ring terminals paired with 12-gauge wires are particularly effective due to their robust construction and corrosion resistance. These terminals are designed to withstand the harsh conditions of the sea, providing reliable connections for navigational lights and other critical electrical systems on board vessels. The selection of the correct wire gauge in conjunction with the appropriate ring terminal is essential for maintaining safety and functionality, even under the most challenging circumstances. Each case study underscores the importance of considering wire gauge compatibility when selecting ring terminals to ensure that the electrical connections are both durable and reliable.