Optimizing Safety in Electrical Systems with Proper Ring Terminal Use and Installation
When integrating ring terminals into electrical systems, safety is paramount. This article delves i…….
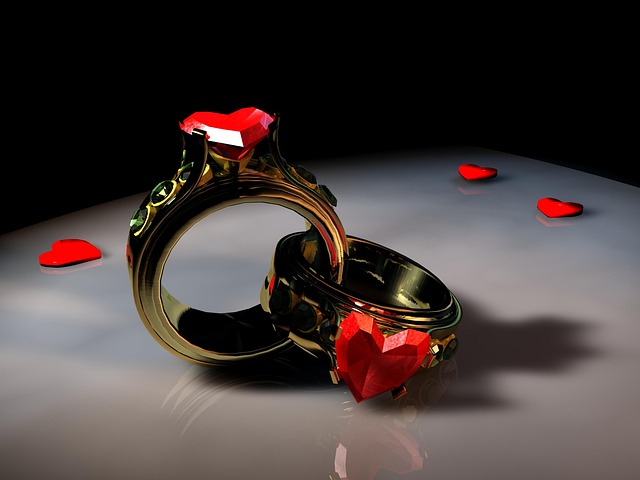
When integrating ring terminals into electrical systems, safety is paramount. This article delves into critical considerations for their installation, ensuring both performance and protection against electrical hazards. From material selection to adherence with safety standards, we explore the essential aspects of handling these components effectively. Understanding the role of ring terminals in safeguarding electrical circuits is the first step; proper installation techniques are vital to maintain their integrity. Regular inspections help identify wear and potential risks, while adhering to best practices for grounding maximizes safety. Additionally, we highlight the importance of training and certification for those handling these installations to ensure compliance with all relevant safety regulations.
- Understanding Ring Terminals and Their Role in Electrical Safety
- Material Selection for Ring Terminals: Factors Impacting Safety and Performance
- Proper Installation Techniques to Ensure Ring Terminal Integrity
- Inspecting Ring Terminals: Identifying Wear and Potential Hazards
- Grounding Best Practices with Ring Terminals in Electrical Systems
- Compliance with Safety Standards and Regulations for Ring Terminal Use
- Training and Certification for Personnel Handling Ring Terminal Installations
Understanding Ring Terminals and Their Role in Electrical Safety
Ring terminals play a critical role in electrical safety by providing secure and reliable connections to conductors, ensuring the integrity of electrical systems. These components are designed to form a protective enclosure around the terminal end of a wire, safeguarding against corrosion, strain, and accidental disconnection. The proper use of ring terminals is essential for maintaining the functionality and longevity of electrical installations, as they are exposed to various environmental conditions and physical stresses that could otherwise compromise the system’s safety.
When selecting a ring terminal, it is imperative to consider factors such as the wire gauge, the operating environment, and the expected mechanical stress to ensure a compatible fit. The material of the ring terminal itself, often copper alloy or brass, contributes to its durability and electrical conductivity. Proper installation techniques involve stripping the wire insulation to the correct length, inserting the conductor into the ring, and securing it with a set screw. This process minimizes resistance and ensures a solid connection that can handle the demands of its application. Regular inspection and maintenance are also crucial to verify that the ring terminals remain intact, without signs of overheating or damage, which could pose significant safety risks.
Material Selection for Ring Terminals: Factors Impacting Safety and Performance
When implementing ring terminals, the selection of material is paramount for ensuring both safety and performance. These components are critical in establishing a secure electrical connection between conductive elements and cables’ termination points in various environments. The choice of material influences the terminal’s resistance to environmental factors such as corrosion, mechanical wear, and temperature variations. For instance, copper alloys are often favored for their excellent electrical conductivity, durability, and resistance to corrosion. Additionally, the material must be compatible with the voltage and current ratings of the system to prevent overheating and potential fires. In harsh conditions, materials like stainless steel offer superior resistance to rust and chemical exposure, making them ideal for use in industrial settings or in areas with high humidity. It is also crucial to consider the mechanical properties of the material, including tensile strength and flexibility, to ensure a secure connection that can withstand vibrations and physical stress without loosening or failing. Proper material selection not only enhances the longevity of the ring terminal but also safeguards personnel and equipment from electrical hazards.
Proper Installation Techniques to Ensure Ring Terminal Integrity
When installing ring terminals, adherence to proper technique is paramount to maintaining their integrity and ensuring safe electrical connections. The process begins with selecting the appropriate size and type of ring terminal for the conductive wire gauge and the application’s environment. Properly sizing the ring terminal ensures that the connection will be secure and that the wire will not be over or under stressed, which could lead to failure or increased resistance. It is crucial to clean and deburr the terminal opening to remove sharp edges that could damage the insulation of the wire. Once the wire is inserted and positioned correctly within the ring terminal, it should be twisted or wrapped as per manufacturer’s instructions to prevent slippage and ensure a solid connection.
After inserting the wire, applying the correct amount of force is essential when crimping the terminal onto the wire. Over-crimping can lead to deformation of the terminal or the wire, potentially compromising the connection’s integrity, while under-crimping may result in an unsafe connection that could become loose over time. Utilizing a proper crimping tool designed for the gauge of the wire and the type of terminal is non-negotiable. The force applied should be consistent and even; this can be achieved by using a calibrated crimping tool or a hydraulic press. Post-installation, inspecting the connection for any signs of deformation, misalignment, or poor fit is a critical step to confirm that the ring terminal installation is both secure and reliable. Regular inspections and maintenance are also recommended to ensure that connections remain intact and function optimally throughout the lifespan of the electrical system.
Inspecting Ring Terminals: Identifying Wear and Potential Hazards
When maintaining electrical systems, regular inspections of ring terminals are imperative for safety and reliability. Ring terminals serve as critical connections between cables and electrical apparatuses, subjecting them to wear over time. A thorough visual inspection should be conducted to identify any signs of physical damage, corrosion, or loose connections. Corroded contacts can lead to poor conductivity and potential arcing, which poses a fire hazard. Additionally, wear on the insulation can expose conductive elements, creating a risk of electrical shock or short-circuiting. It is crucial to check for any deformation or distortion in the terminal as well, as this can affect the terminal’s mechanical integrity and its secure attachment to both the cable and equipment. Ensuring that ring terminals are properly maintained and inspected will mitigate these risks and maintain the integrity of the electrical system. Regular upkeep not only extends the lifespan of the terminals but also ensures the safety of personnel and the operational efficiency of equipment.
Grounding Best Practices with Ring Terminals in Electrical Systems
Grounding is a critical aspect of electrical systems to ensure safety and proper functionality. Ring terminals play an essential role in this process by providing secure connections between conductive elements and cables. When implementing ring terminals for grounding, adherence to best practices is paramount. It’s crucial to select the correct size and type of ring terminal based on the cable gauge and the expected current levels. The terminal must be capable of withstanding the current without overheating, ensuring both safety and longevity. Properly tightening the terminal onto the cable ensures a firm connection, reducing the risk of loosening over time and maintaining low resistance contact.
Additionally, it’s important to consider the environmental conditions where the ring terminals will be used. Exposure to elements like moisture or corrosive substances can compromise the integrity of the terminal if not properly protected. Employing appropriate coatings or weatherproof enclosures can mitigate these risks and prevent degradation of the terminal’s performance. Regular inspection and maintenance are also key practices for maintaining the reliability of ring terminals in grounding applications. This includes checking for signs of corrosion, damage, or looseness, and tightening or replacing the terminals as necessary. By following these best practices, electrical systems can be effectively grounded, enhancing safety and protecting against equipment damage and potential electrical hazards.
Compliance with Safety Standards and Regulations for Ring Terminal Use
When implementing ring terminal installations, adherence to safety standards and regulations is paramount to prevent electrical hazards and ensure system integrity. These terminals, which serve as connections between wires and conductive elements such as bolts or bars, are critical components in various electrical systems. The National Electrical Code (NEC) provides specific guidelines for the proper use of ring terminals, emphasizing the importance of selecting the correct size and type for the application to handle the expected current load safely. Proper installation involves securely tightening the terminal to the conductor, applying the appropriate amount of sealant to prevent corrosion, and ensuring that all connections are free from tension that could loosen over time. Additionally, it is crucial to use terminals with the correct insulation rating for the environment in which they will be used, as exposure to different temperatures can affect both the terminal’s performance and the integrity of the electrical circuit. Regular maintenance checks and inspection by qualified personnel are necessary to verify that ring terminals remain compliant with safety standards throughout their service life, thereby minimizing the risk of accidents or equipment failure due to faulty connections. Adhering to these practices not only ensures compliance with safety regulations but also contributes to the longevity and reliability of the electrical system as a whole.
Training and Certification for Personnel Handling Ring Terminal Installations
When integrating ring terminals into electrical installations, proper training and certification of personnel are paramount to ensure safety and compliance with industry standards. Adequate training programs should be established for those responsible for handling and installing ring terminals, as these components interface with high-current connections that require precise and secure terminations. Personnel must be versed in the technical specifications of the ring terminals they are using, including the selection of the correct size and type for the application at hand. This knowledge is crucial for maintaining electrical integrity and preventing potential hazards such as overheating or electrical arcing.
Certification ensures that workers have the necessary skills and theoretical understanding to perform their duties effectively and safely. It is important that those involved in the installation process are certified in accordance with relevant safety regulations, such as the National Electrical Code (NEC) or other local standards. This certification often includes practical assessments, where individuals demonstrate their ability to correctly install ring terminals on conductors, properly tighten them to specified torque values, and verify that connections are both secure and leakage-free. Regular updates to training and recertification are necessary due to the evolving nature of electrical systems and safety protocols, thus maintaining a high standard of competency among those handling ring terminals.