Optimizing Ring Terminal Crimp Quality: A Comprehensive Testing Guide
Ring terminals are critical components for ensuring the functionality and safety of electrical conn…….
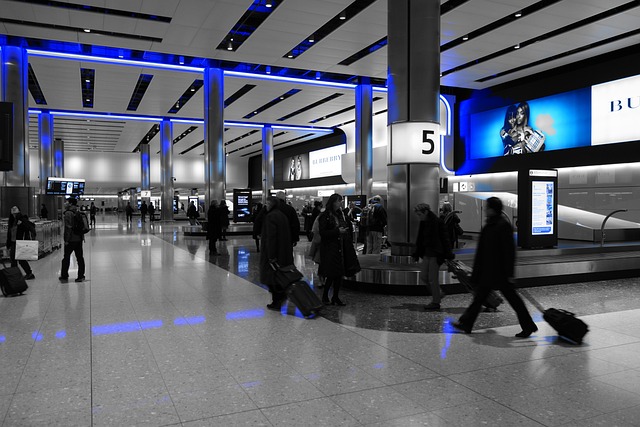
Ring terminals are critical components for ensuring the functionality and safety of electrical connectors across various sectors such as industrial machinery and consumer electronics. The reliability of these terminals is directly linked to the quality of their crimp connections, which are rigorously evaluated through comprehensive testing. This process involves meticulous assessments to verify that the ring terminals securely and consistently interface with connectors, adhering to high industry standards. Key factors like crimp height, angle, and applied force are measured to ensure optimal performance under operational stresses. By strictly following these quality control measures, manufacturers guarantee that each terminal is defect-free, thereby preventing potential failures and mitigating safety risks. The crimp quality testing is an essential practice in the production of ring terminals, ensuring they can withstand harsh conditions and maintain reliable electrical connections, reflecting a commitment to excellence in manufacturing integrity. High-quality crimping tools, consideration of environmental factors, and stringent testing protocols—encompassing mechanical, electrical, and environmental assessments—are all vital to maintaining consistent performance and long-term reliability for ring terminals. This dedication to quality assurance not only ensures peak performance but also extends the lifespan and enhances the safety of the systems they support.
When electrical integrity hinges on the reliability of connections, ring terminal crimp quality emerges as a critical factor. This article delves into the pivotal role of crimp quality testing for ring terminals, emphasizing the importance of maintaining consistent and high-performance standards to ensure safety and dependability in electrical applications. We will explore the essential aspects of this process, from assessing the integrity of ring terminals to adhering to stringent performance benchmarks, ensuring that every connection is both secure and robust. Join us as we shed light on the intricacies of crimp quality testing and its indispensable contribution to the world of electrical engineering.
- Assessing the Integrity of Ring Terminals: The Role of Crimp Quality Testing
- Key Factors Influencing Ring Terminal Crimp Consistency and Performance Standards
- The Process of Crimp Quality Testing for Ring Terminals: Ensuring Reliability and Safety in Electrical Connections
Assessing the Integrity of Ring Terminals: The Role of Crimp Quality Testing
Ring terminals serve as critical components in electrical connectors, ensuring the reliable transfer of electrical currents in various applications. The integrity of these terminals is paramount, and one of the most effective methods to assess this is through crimp quality testing. This process involves a series of technical evaluations that determine the quality and durability of the terminal-to-connector interface. Crimp quality testing is essential for verifying that the mechanical and electrical connections are secure, consistent, and free from defects. It encompasses both visual inspections and automated systems that apply precise force to the terminals. These tests measure parameters such as crimp height, angle, and the force applied, ensuring compliance with industry standards. The results of these tests are crucial for predicting the terminal’s performance under operational conditions, thereby preventing potential failures and reducing safety risks in the field. Manufacturers rely on crimp quality testing to ensure that each ring terminal meets the necessary specifications, contributing to the overall reliability and longevity of the electrical connections they form. This rigorous process is a cornerstone of quality control within the manufacturing industry, ensuring that these essential components perform as expected in demanding environments.
Key Factors Influencing Ring Terminal Crimp Consistency and Performance Standards
In the realm of electrical connectivity, ring terminals play a pivotal role due to their robust and reliable design. The consistency in the crimp quality of these terminals is paramount for ensuring optimal performance under various conditions. Key factors influencing crimp consistency include the precision of the crimping tool, the material properties of the terminal and conductor, the skill of the operator, and the environmental conditions during installation and operation. Advanced crimping tools are engineered to apply consistent force and maintain alignment throughout the crimping process, which is essential for achieving a high-quality crimp every time. The choice of materials, such as copper alloys or aluminum, in both the ring terminal and the conductor, affects the electrical conductivity and mechanical strength of the joint. Operator proficiency, on the other hand, is critical to avoid human errors that could compromise the integrity of the crimp. Environmental factors like temperature and humidity can also influence the performance of the crimped connection; thus, it’s imperative to consider these elements during both installation and long-term operation.
To maintain performance standards, rigorous testing protocols are essential. These protocols often involve a combination of mechanical, electrical, and environmental tests to ensure that the crimp meets or exceeds established industry norms. For instance, mechanical pull tests assess the strength and resistance of the connection, while electrical tests verify the continuity and integrity of the conductor. Additionally, durability tests under various temperature extremes and exposure to corrosive substances help guarantee the longevity and reliability of the ring terminal crimp in diverse applications. Adherence to these performance standards is crucial for safety, efficiency, and long-term system dependability, underscoring the importance of a meticulous approach to ring terminal crimping quality testing.
The Process of Crimp Quality Testing for Ring Terminals: Ensuring Reliability and Safety in Electrical Connections
Ring terminals play a critical role in ensuring the reliability and safety of electrical connections in various applications, from industrial machinery to consumer electronics. The process of crimp quality testing for ring terminals is a meticulous procedure that assesses the integrity of the connection between the wire and the terminal. This test ensures that the crimped joint can withstand environmental stressors, maintain a secure connection, and perform reliably over time.
The crimp quality testing involves multiple stages where specific parameters are measured to validate the structural and electrical performance of the terminal-to-wire junction. Key metrics such as crush length, wire diameter tolerance, and insulation thickness are scrutinized against industry standards. Advanced equipment, including automatic crimping machines coupled with precise measurement tools, is employed to automate the testing process, enhancing consistency and reducing the potential for human error. This rigorous process not only guarantees the optimal functionality of the ring terminals but also contributes to the overall safety and longevity of the electrical systems they serve.