Optimizing Industrial Electrical Connections with Advanced Ring Terminal Solutions
Ring terminals are essential for ensuring the safety and efficiency of industrial electrical system…….
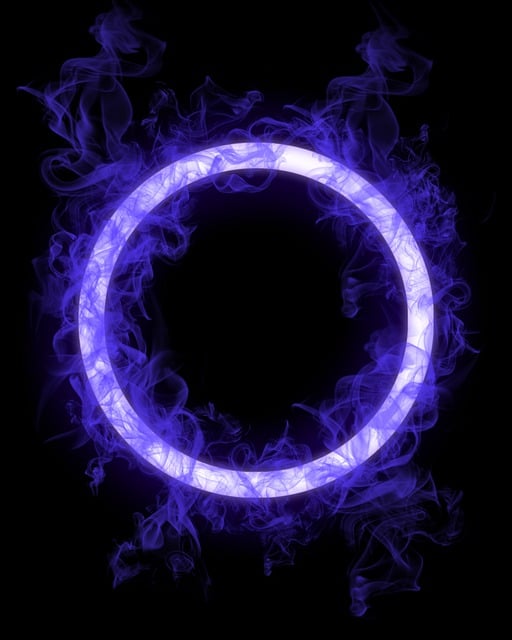
Ring terminals are essential for ensuring the safety and efficiency of industrial electrical systems by providing a secure and durable connection between conductors and their points of use. These terminals are designed to handle various wire sizes and perform reliably under harsh conditions, including extreme temperatures, vibrations, and corrosive environments. The locking feature in ring terminals ensures conductor stability, preventing arcing and disconnection due to stress or environmental factors. Selecting the correct ring terminal that aligns with the wire gauge, type, and operational environment is critical for system safety and efficiency. Ring terminals also need to be matched with the electrical system's current rating to prevent overheating and meet safety standards. Material compatibility is essential to resist environmental factors like corrosion and UV exposure. Mechanical durability, including strain relief properties, ensures a secure connection under physical stress and vibration. Proper tailoring of ring terminals to fit within devices and align with mating connectors, along with flexibility for applications requiring frequent bending or movement, is necessary. Adherence to industry standards, such as those for automotive and renewable energy sectors, ensures that these terminals perform effectively under various conditions. Advancements in materials science have led to the use of high-performance alloys that enhance durability and lifespan, while smart materials offer real-time monitoring capabilities. Manufacturing innovations like 3D printing and Industry 4.0 principles have improved quality control and predictive maintenance, ensuring ring terminals meet stringent standards for critical applications. The future of ring terminals is set to be even more resilient, efficient, and intelligent, solidifying their role as integral components in the industrial sector's technological evolution.
ring terminals serve as critical components in industrial electrical systems, ensuring reliable and safe connections that are indispensable for various applications. This article delves into their pivotal role within these systems, examining the selection criteria that influence their performance and longevity. Furthermore, advancements in materials and technologies are reshaping the landscape of ring terminals, offering enhanced durability and efficiency. As we explore these aspects, it becomes evident that ring terminals are not just a connector but a cornerstone of modern industrial electrical systems.
- Understanding the Role of Ring Terminals in Industrial Electrical Systems
- Key Factors Influencing the Selection and Application of Ring Terminals
- Advanced Materials and Technologies Shaping the Future of Ring Terminals in Industry
Understanding the Role of Ring Terminals in Industrial Electrical Systems
Ring terminals serve as critical components within industrial electrical systems, ensuring the secure and reliable connection between electrical conductors and their respective fittings or devices. These terminals are designed to provide a robust interface that can withstand the demands of high-performance environments. They are engineered to accommodate a range of wire sizes, providing versatility in applications across various industries. The durability and reliability of ring terminals are paramount, as they must perform consistently under often harsh conditions, which may include extreme temperatures, vibrations, and exposure to corrosive elements.
In the realm of industrial applications, ring terminals are instrumental in safeguarding against electrical disconnection due to mechanical stress or environmental factors. Their design incorporates a locking feature that maintains conductor stability over time, thereby reducing the likelihood of arcing and preventing potential hazards associated with loose connections. The selection of ring terminals is a critical aspect of designing a safe and efficient electrical system, as they must be compatible with the specific gauge and type of wire used, as well as the environmental conditions in which the equipment will operate. Properly selected and installed ring terminals contribute significantly to the overall integrity and longevity of industrial electrical systems.
Key Factors Influencing the Selection and Application of Ring Terminals
When integrating ring terminals into industrial applications, several key factors significantly influence their selection and application. The first factor is the electrical rating of the terminal, which must align with the current-carrying capacity required for the specific application to prevent overheating and ensure safety. Material compatibility is another critical aspect; ring terminals must be constructed from materials that can withstand the environmental conditions they’ll encounter, such as corrosive substances, extreme temperatures, or exposure to UV light. The mechanical robustness of the terminal, including its strain relief properties, is essential for maintaining a secure connection under physical stress and vibration during operation.
Furthermore, the physical dimensions and configuration of the ring terminal must be appropriate for the space available on the device and compatible with mating connectors. This includes considering the cable diameter and the orientation of the terminal to ensure proper alignment and conductivity. Additionally, the selection process should take into account the level of flexibility required by the application, as some environments demand terminals that can endure frequent bending or movement without compromising performance. Lastly, compliance with industry standards and certifications is a non-negotiable factor, ensuring that the ring terminals meet the necessary regulatory requirements for their intended use in various industries, from automotive to renewable energy.
Advanced Materials and Technologies Shaping the Future of Ring Terminals in Industry
The evolution of ring terminals within industrial applications is being propelled by advancements in materials science and technological innovations. High-performance alloys are increasingly being utilized to enhance the durability, conductivity, and longevity of ring terminals. These alloys not only improve resistance to environmental factors such as corrosion and extreme temperatures but also ensure consistent electrical performance over extended periods. Additionally, the integration of smart materials has opened new frontiers, allowing for ring terminals that can adapt to varying conditions or provide real-time data on their operational status. This is particularly advantageous in industries requiring high reliability under harsh environments, such as aerospace and automotive sectors.
In parallel with material advancements, the adoption of cutting-edge manufacturing technologies is streamlining the production process of ring terminals, leading to higher precision and efficiency. Technologies like 3D printing are enabling the creation of complex geometries that were previously unattainable, resulting in more robust and ergonomic designs. Furthermore, the integration of Industry 4.0 principles is facilitating smarter manufacturing processes with enhanced quality control and predictive maintenance capabilities. These advancements not only reduce downtime but also ensure that ring terminals meet stringent industry standards, guaranteeing their reliability and safety in critical applications. As these technologies continue to mature, the future of ring terminals in industrial settings is poised to be more resilient, efficient, and intelligent than ever before.