Optimizing Electrical Performance: Navigating Resistance in Ring Terminals
Ring terminals are critical for ensuring reliable and safe electrical connections in a wide array o…….
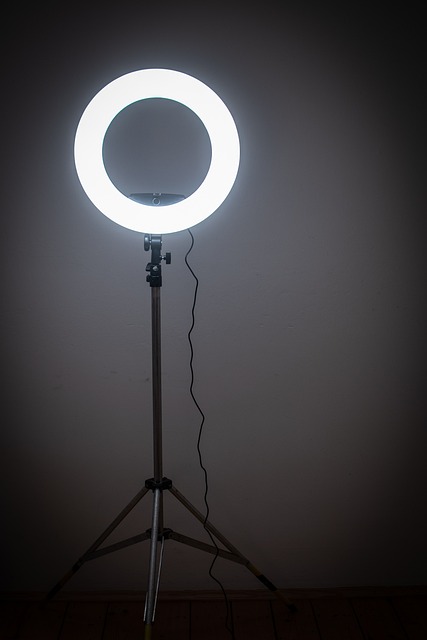
Ring terminals are critical for ensuring reliable and safe electrical connections in a wide array of applications, including industrial machinery and automotive wiring. The performance of these systems hinges on the low resistance provided by ring terminals, which is influenced by their material composition, cross-sectional size, and the environmental conditions they operate within. Selecting the right ring terminal involves assessing factors like conductor size, material type—such as copper alloys, aluminum, or stainless steel—and anticipated mechanical stresses to ensure durability and performance over time. By considering these elements, users can maintain stable and safe electrical connections that resist overheating and energy loss, thereby enhancing the overall safety and efficiency of the system. Manufacturers must design ring terminals with attention to these details to meet the varying demands of different applications.
When electrical currents flow through systems, components like ring terminals play a pivotal role in ensuring efficient energy transfer. This article delves into the critical aspect of electrical resistance within these integral connectors and its influence on overall system performance. We will explore the key factors that affect resistance—namely material properties, design elements, and environmental conditions—and how these can be optimized to enhance conductivity. Additionally, we will examine practical techniques and innovative solutions for reducing resistance in ring terminals, ensuring reliable connections for a variety of applications. By understanding and addressing electrical resistance, users can make informed decisions when selecting the appropriate ring terminal for their specific needs, thereby improving efficiency and longevity in their electrical systems.
- Understanding Electrical Resistance in Ring Terminals: The Impact on Performance and Selection Criteria
- Factors Influencing Resistance in Ring Termals: Material Composition, Design, and Environmental Considerations
- Mitigating Resistance in Ring Terminals: Techniques, Best Practices, and Advanced Solutions for Optimal Conductivity
Understanding Electrical Resistance in Ring Terminals: The Impact on Performance and Selection Criteria
Electrical resistance in ring terminals plays a critical role in their performance and reliability within electrical systems. These components, which serve as the termination points for conductors in various applications, from industrial machinery to automotive wiring, must be selected with careful consideration of their resistance properties to ensure optimal electrical connection. The resistance present in ring terminals can affect current flow, voltage drop, and overall system efficiency. It is influenced by factors such as material composition, the cross-sectional area of the terminal’s conductive path, and the environmental conditions it operates under. Selecting a ring terminal with an appropriate resistance value ensures that there is minimal energy loss during the transfer of electrical current, which is essential for maintaining system integrity and preventing overheating. Moreover, understanding the resistance characteristics allows for better prediction of the terminal’s lifespan and its ability to perform under varying load conditions. When selecting ring terminals, it is imperative to consider the specific application requirements, including the operating temperature range, the size and type of conductors to be used, and the expected mechanical stresses. These selection criteria are vital for ensuring that the chosen ring terminal will provide a stable, reliable connection over its intended service life, contributing to the safety and efficiency of the entire electrical system.
Factors Influencing Resistance in Ring Termals: Material Composition, Design, and Environmental Considerations
Ring terminals are critical components in electrical systems, serving as the interface between cables and various devices or machinery. The resistance exhibited by ring terminals can significantly influence their performance and reliability. Several factors play a pivotal role in determining the resistance characteristics of these terminals.
The material composition of ring terminals is paramount in dictating their electrical resistance. Different metals, such as copper alloys, aluminum, and stainless steel, offer varying levels of conductivity; copper, for instance, has a lower resistance compared to aluminum. The purity of the metal and its grain structure also affect resistance. A fine-grained metal typically exhibits less resistance than one with coarse grains. Additionally, the cross-sectional area of the terminal is directly proportional to its conductivity; larger areas provide lower resistances due to increased surface contact for current flow.
Beyond material composition, the design of the ring terminal also significantly impacts its electrical resistance. The geometry of the terminal, including factors such as the thickness of the conductor, the bending radius, and the presence of any insulating materials, can affect the path current takes, thus influencing resistance. A well-designed ring terminal minimizes sharp bends or constrictions that could disrupt the flow of electricity and cause an increase in resistance. Furthermore, environmental considerations are equally important. Temperature extremes, exposure to corrosive substances, and mechanical stress can all alter the dimensions of the terminal, potentially increasing its resistance over time. It is essential to select materials and designs that are robust enough to withstand the operational environment while maintaining low resistance for optimal performance. Manufacturers must consider these factors in tandem to ensure that ring terminals perform reliably under various conditions throughout their service life.