Optimizing Electrical Performance: Addressing Resistance in Ring Terminals
Ring terminals are essential components for ensuring reliable electrical connections, particularly …….
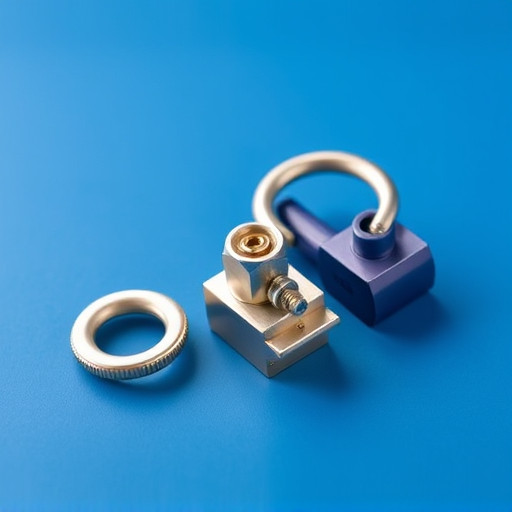
Ring terminals are essential components for ensuring reliable electrical connections, particularly where minimizing resistance and maximizing efficiency are critical. These terminals, which connect wires to devices or components, must be engineered from materials with low resistivity, such as copper alloys, to maintain optimal performance under various conditions like temperature extremes and mechanical stress. Advanced manufacturing processes ensure that the terminals' design reduces resistance and prevents overheating or power loss. The cross-sectional area of the ring terminal is a critical factor affecting resistance, with larger areas allowing for greater surface area and thus lower resistance. Environmental factors such as high temperatures and contaminants can significantly impact resistance, necessitating regular maintenance to prevent performance degradation. In applications demanding high reliability and safety, selecting appropriate materials and designs for ring terminals, along with adhering to strict manufacturing standards, is essential for maintaining efficient energy transfer and ensuring long-term system integrity. Regular inspection and cleaning are vital for maintaining the conductivity and longevity of these crucial components in electrical systems.
When electrical currents flow through systems, the integrity of connections is paramount. This article delves into a critical aspect of these connections: electrical resistance in ring terminals. We explore the factors influencing resistance, the significance of material selection for optimal performance, and practical strategies to mitigate resistance effectively. Understanding the nuances of ring terminals is essential for ensuring reliable power transmission in various applications, from industrial machinery to consumer electronics. Join us as we unravel the complexities surrounding this indispensable component of electrical systems.
- Understanding Electrical Resistance in Ring Terminals
- Factors Influencing Resistance in Ring Terminals
- The Role of Material Selection in Minimizing Resistance
- Strategies for Mitigating Resistance in Ring Terminal Applications
Understanding Electrical Resistance in Ring Terminals
When electrical current passes through ring terminals, a minor but measurable amount of energy is inevitably dissipated as heat due to electrical resistance. This phenomenon, known as electrical resistance, is a critical aspect of the performance and reliability of ring terminals. The resistance within these components can affect the efficiency and integrity of an electrical circuit. Ring terminals, which serve as the interface between wires and various electrical devices or components, must be engineered to minimize this resistance to ensure optimal power transmission and to prevent excessive heat generation that could lead to degradation or failure over time.
The design and material selection of ring terminals play a pivotal role in managing electrical resistance. Factors such as the cross-sectional area of the terminal, the material from which it is made, and the environmental conditions it operates under all influence its resistivity. Copper, for instance, is commonly used due to its low resistivity, but other factors like temperature, frequency of operation, and mechanical stress must be considered to maintain its electrical conductivity. Manufacturers often employ advanced manufacturing techniques and materials with higher conductivity to mitigate resistance, ensuring that the ring terminals can handle the intended current without undue heat build-up or power loss. Understanding and managing electrical resistance in ring terminals is thus essential for maintaining efficient and reliable electrical connections.
Factors Influencing Resistance in Ring Terminals
The electrical resistance in ring terminals is influenced by several factors that are critical to understand for optimal performance and safety in electrical systems. Material composition plays a significant role; terminals made from metals with higher electrical conductivity, such as copper or silver alloys, exhibit lower resistance compared to those made from less conductive materials. The cross-sectional area of the terminal is another determinant, with larger areas offering less resistance due to the increased surface area for current flow.
Environmental conditions also significantly affect resistance. High temperatures can increase resistance due to the thermal expansion of metals and potential oxidation, which forms an insulating layer on the conductor’s surface. Similarly, contaminants like dirt or corrosion products can cause additional resistance as they disrupt the flow of electrons. The design and configuration of the terminal, including its geometry and the method of attachment to the conductive element, further influence resistance. Proper selection of ring terminals that are compatible with the specific application and environmental conditions ensures minimal resistance and reliable electrical connections.
The Role of Material Selection in Minimizing Resistance
When selecting materials for ring terminals, it is crucial to consider their electrical resistance properties to ensure optimal performance in electrical circuits. The choice of material directly influences the terminal’s ability to conduct electricity effectively, minimizing voltage drop and energy loss over time. Copper alloys are commonly preferred due to their superior electrical conductivity and durability; however, other factors such as environmental conditions, temperature extremes, and mechanical stress must be accounted for in the selection process. For instance, silver-plated copper ring terminals offer enhanced conductivity and corrosion resistance in harsh environments, which can significantly reduce resistance compared to uncoated alternatives. Additionally, the cross-sectional area of the terminal must be optimized to balance between current carrying capacity and the physical space available within the application. Incorporating a deeper understanding of the materials’ electrical characteristics and how they interact with the application’s environment allows for the design of ring terminals that minimize resistance and ensure reliable, consistent performance. This not only extends the lifespan of the terminal but also contributes to the overall efficiency of the electrical system it is part of.
Strategies for Mitigating Resistance in Ring Terminal Applications
In high-performance electrical systems, ring terminals play a critical role in establishing reliable connections between cables and apparatuses. To maintain optimal performance, it is essential to address the electrical resistance inherent in these components. Mitigating resistance in ring terminal applications involves a combination of material selection, proper sizing, and precision manufacturing techniques. Utilizing materials with lower resistivity, such as copper alloys over aluminum where appropriate, can significantly reduce the overall resistance of the terminal. Additionally, the cross-sectional area of the ring terminal should be carefully chosen to ensure that it can carry the current required without causing excessive voltage drops. Proper sizing ensures that the contact pressure is evenly distributed across the interface between the cable and the terminal, which minimizes the contact resistance and enhances the longevity of the connection. Furthermore, the design and manufacture of ring terminals should adhere to stringent standards to ensure a tight fit with the cable conductor, preventing any air gaps that could increase resistance. Regular maintenance and inspection are also vital to detect and address oxidation or corrosion that can degrade the terminal’s conductivity over time. By implementing these strategies, engineers can effectively mitigate electrical resistance in ring terminal applications, ensuring reliable and efficient power transmission.