Optimizing Electrical Connections with High-Performance Copper Ring Terminals
Copper ring terminals are essential components for secure and efficient electrical connections, wide…….
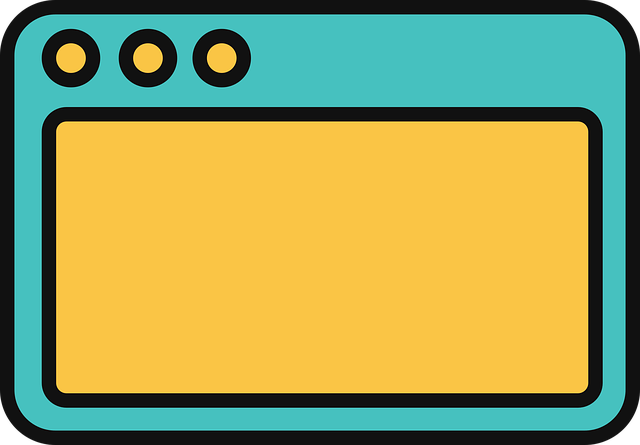
Copper ring terminals are essential components for secure and efficient electrical connections, widely used across various applications due to their durability and conductivity. These terminals encapsulate wire ends, ensuring a reliable interface with components like outlets, motors, and control devices. Copper's high conductivity, thermal properties, and corrosion resistance facilitate safe power transmission while the terminals' malleable nature allows for use in a range of settings from residential to heavy industrial environments. The importance of selecting the right ring terminal based on wire size, environmental conditions, and potential mechanical stress cannot be overstated for optimal performance and safety within electrical systems. Adherence to ASTM standards guarantees excellence and safety, with rigorous benchmarks covering material specifications, performance criteria, and testing protocols. Advanced materials science has led to enhancements in these terminals, improving their conductivity, durability, and environmental resistance, which is crucial for their integrity under mechanical stress and resisting corrosion. These improvements ensure consistent performance across a variety of sectors, including automotive and industrial machinery, guaranteeing dependable power transmission and enhancing overall safety and reliability within electrical systems.
Copper ring terminals are a critical component in electrical connections, offering robust and reliable performance in various applications. This article delves into their pivotal role, material specifications, and the stringent ASTM standards that guarantee quality and safety. We will guide you through selecting the optimal size and type for your specific needs, and explore cutting-edge advancements in ring terminal technology that enhance overall system efficiency and longevity. Join us as we examine how these indispensable electrical connectors ensure secure and dependable connections across industries.
- Understanding the Role of Copper Ring Terminals in Electrical Connections
- Key Features and Material Specifications of Copper Ring Terminals
- The Importance of ASTM Standards in Ensuring Quality and Safety of Copper Ring Terminals
- Guide to Selecting the Right Size and Type of Copper Ring Terminal for Your Application
- Innovations and Advancements in Copper Ring Terminal Technology for Optimal Performance
Understanding the Role of Copper Ring Terminals in Electrical Connections
Copper ring terminals play a pivotal role in ensuring reliable and secure electrical connections, particularly in applications that demand high conductivity and durability. These terminals are engineered to fit around the end of a wire with a ring-like shape, providing a solid interface for connecting to various components such as electrical outlets, motors, or control devices. The use of copper as the material of choice is attributed to its superior electrical conductivity, high thermal conductivity, and excellent corrosion resistance, which are essential properties for maintaining efficient and safe electrical systems.
The design of copper ring terminals incorporates a tight fit around the wire, which minimizes the risk of loose or poor connections that could lead to signal degradation or even fire hazards. The tight fit also helps to prevent oxidation and corrosion at the point of connection, ensuring longevity and reliability over time. Moreover, the flexibility and formability of copper allow for versatile applications in various environments, from industrial settings to consumer electronics. Selecting the appropriate size and type of ring terminal, considering factors such as the wire gauge, environmental conditions, and mechanical stresses, is crucial for optimizing performance and safety in electrical installations.
Key Features and Material Specifications of Copper Ring Terminals
Copper ring terminals are a critical component in electrical connections, offering robust and reliable joints for various applications. These terminals are engineered to securely connect conductors to other electrical components, ensuring efficient electrical contact and preventing corrosion or loosening over time. Key features of copper ring terminals include their versatility, as they are suitable for use in a range of environments from domestic to industrial settings. The design typically incorporates a robust copper ring, which serves as the conductive element, and is often combined with an insulating material that protects the connection while allowing for flexibility and movement within the joint.
Material specifications for copper ring terminals are meticulously controlled to maintain high standards of performance. Copper, with its excellent electrical conductivity and durability, provides a reliable path for electric current. The alloy used in the manufacturing process can vary, with common types being oxygen-free high-conductivity (OFHC) copper and annealed copper, each chosen for specific applications based on their respective properties. Additionally, these terminals are often coated or plated with materials like tin, nickel, or silver to enhance corrosion resistance and prolong the lifespan of the connection in harsh conditions. The selection of the correct ring terminal involves considering factors such as current load, temperature range, and environmental exposure to ensure optimal performance and safety.
The Importance of ASTM Standards in Ensuring Quality and Safety of Copper Ring Terminals
Copper ring terminals are critical components in electrical connections, serving as the interface between conductive wires and various equipment components. The reliability and safety of these terminals are paramount, considering their widespread application across numerous industries, from residential electrical systems to heavy-duty machinery. ASTM standards play a pivotal role in ensuring the quality and safety of copper ring terminals. These standards, set by the American Society for Testing and Materials (ASTM), provide a comprehensive framework that dictates material specifications, performance criteria, and testing methods. By adhering to ASTM standards, manufacturers can produce copper ring terminals that consistently meet stringent requirements for durability, conductivity, and resistance to environmental factors. These benchmarks not only guarantee the functionality of the terminals under various conditions but also safeguard users from potential hazards associated with electrical malfunctions or poor connections. The consistent application of ASTM standards across the industry fosters a uniform level of quality and safety, instilling confidence in professionals and consumers alike who rely on these terminal connections for their electrical needs.
Guide to Selecting the Right Size and Type of Copper Ring Terminal for Your Application
When working with electrical connections, selecting the appropriate size and type of copper ring terminal is paramount for ensuring safe and efficient power transmission. The right choice depends on several factors, including the gauge of the wire, the amplitude of the current, and the environmental conditions in which the connection will operate. For instance, larger gauges of wire require ring terminals with proportionately larger inner and outer diameters to maintain a secure and conductive fit. It’s essential to match the terminal’s cross-sectional area to the wire’s ampacity to prevent overheating and potential fires. Additionally, environmental factors such as temperature extremes, moisture, and exposure to corrosive substances necessitate the use of ring terminals with appropriate insulation and protective finishes.
In applications ranging from residential wiring to industrial machinery, the choice between solid copper or tinned copper for the terminal material also plays a significant role. Solid copper provides superior conductivity, while tin coating offers enhanced corrosion resistance, making it suitable for outdoor use or in humid environments. Furthermore, the type of ring terminal should align with the application’s mechanical demands. For example, heavy-duty applications might require terminals with set screws for additional clamping force, while those in sensitive equipment may call for insulation displacement (IDP) types to minimize contact resistance and maximize performance. Selecting the correct ring terminal is a critical step in the assembly of reliable electrical connections, ensuring safety, longevity, and optimal function of the device or system.
Innovations and Advancements in Copper Ring Terminal Technology for Optimal Performance
Copper ring terminals have undergone significant advancements in recent years, driven by the need for reliable and efficient electrical connections across various industries. Innovations in materials science have led to enhancements in the copper alloys used, resulting in terminals that offer superior conductivity, durability, and resistance to environmental stressors. These developments ensure that connections remain intact under high mechanical loads and resist corrosion, thereby prolonging their lifespan and maintaining optimal performance.
The evolution of copper ring terminal technology is characterized by the integration of precision engineering with advanced manufacturing techniques such as cold heading and cold forming. This has enabled manufacturers to produce terminals with tighter tolerances and improved electrical contacts. Additionally, the use of high-performance insulating materials has significantly reduced the risk of electrical failure due to poor connections. As a result, these terminals are not only safer but also more reliable for applications ranging from automotive to industrial machinery, ensuring seamless power transmission under varying conditions.