OEM vs. Aftermarket Ring Terminals: Selecting the Right Fit for Your Application
Ring terminals are essential for secure, weatherproof connections in various electrical installatio…….
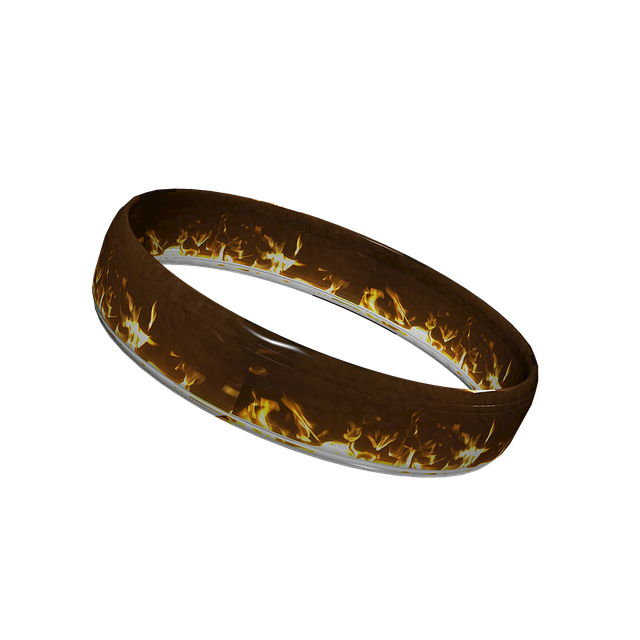
Ring terminals are essential for secure, weatherproof connections in various electrical installations, designed to interface with flexible cable ends. When choosing between OEM and aftermarket ring terminals, it's vital to consider factors like cable size, voltage rating, environmental conditions, and specific application demands. OEM ring terminals are made by the original equipment manufacturer, ensuring high-quality performance that matches design specifications. They come with certifications and warranties, and are ideal for critical applications requiring reliability. Aftermarket ring terminals offer a wider range of options at potentially lower costs but may vary in quality. Both types must meet industry standards set by organizations like NEMA or IEC to guarantee durability and compliance with safety standards. Users should evaluate the material composition—such as copper alloys, aluminum, or stainless steel—for conductivity, durability, and environmental resistance. The chosen ring terminal must also have the appropriate rating for voltage and current capacity to suit your project's needs. Cost, availability, and lead times are additional factors to consider, with OEM options typically offering superior performance and longevity at a higher initial cost but potentially leading to cost savings over time. For a reliable electrical connection, select ring terminals that align with your application's requirements, budget constraints, and the necessity of meeting all relevant industry standards.
When electrical projects demand secure and reliable connections, ring terminals serve as a critical component. This article delves into the pivotal distinctions between Original Equipment Manufacturer (OEM) and aftermarket ring terminals, crucial for informed decision-making in your next project. We will explore their key differences, including material composition, durability, and performance, ensuring you navigate the OEM vs aftermarket landscape with confidence. Understanding the nuances between these options is essential for maintaining electrical integrity and system reliability. Join us as we dissect the factors that influence the choice between OEM and aftermarket ring terminals, enhancing your project’s success.
- Understanding Ring Terminals: OEM vs Aftermarket Options
- Key Differences Between OEM and Aftermarket Ring Terminals
- Factors to Consider When Choosing Between OEM and Aftermarket Ring Terminals for Your Project
Understanding Ring Terminals: OEM vs Aftermarket Options
Ring terminals serve as critical components in electrical installations, providing a secure and weatherproof connection to the end of flexible cables. When selecting ring terminals, it’s important to consider the specific application requirements to ensure compatibility with cable sizes, voltage ratings, and environmental conditions. Original Equipment Manufacturer (OEM) ring terminals are designed and produced by the equipment manufacturer to meet exact specifications for optimal performance. These OEM options are tailored to match the quality and reliability of the original design, offering consistent and predictable outcomes. On the other hand, aftermarket ring terminals are manufactured independently and can be an economical alternative for replacements or additional installations. They often come with a variety of certifications and ratings, allowing users to select the best fit for their needs from a wide range of products. Both OEM and aftermarket ring terminals must adhere to stringent industry standards, such as those set by the National Electrical Manufacturers Association (NEMA) or International Electrotechnical Commission (IEC). When choosing between OEM and aftermarket ring terminals, factors like compatibility with existing equipment, budget constraints, and the specific requirements of the application should be carefully weighed. Quality assurance, durability, and safety are paramount when working with electrical connections, making it essential to select ring terminals that meet or exceed the necessary standards and provide a reliable interface between cables and their termination points.
Key Differences Between OEM and Aftermarket Ring Terminals
When selecting ring terminals for electrical connections, discerning between Original Equipment Manufacturer (OEM) and aftermarket options is crucial due to their distinct characteristics and implications for performance and reliability. OEM ring terminals are designed and produced by the original manufacturer of the equipment, specifically tailored to meet the exact specifications and quality standards set forth for that particular product. These terminals often come with certifications and warranties, ensuring they adhere to stringent performance criteria and offer a precise fit for the application. They are engineered to deliver consistent and reliable electrical connections over time, making them a go-to choice for professionals who demand high-quality and dependable performance in critical applications.
In contrast, aftermarket ring terminals serve as alternative options available from third-party manufacturers. While these can offer competitive pricing and a wider variety of options in terms of sizes, materials, and colors, their design and quality may vary. Aftermarket ring terminals are not produced by the original manufacturer but are compatible with various equipment types. Users must carefully evaluate aftermarket options to ensure compatibility and performance standards that meet their needs. These terminals can be an excellent choice for less demanding applications where cost-effectiveness is a primary concern, and where the application does not necessitate the rigorous quality assurances of OEM parts. When choosing between OEM and aftermarket ring terminals, it’s important to consider the specific requirements of your application, budget constraints, and the importance of having a product that meets both current needs and potential future demands.
Factors to Consider When Choosing Between OEM and Aftermarket Ring Terminals for Your Project
When selecting between OEM (Original Equipment Manufacturer) and aftermarket ring terminals for your project, it’s crucial to evaluate several key factors to ensure the best performance and reliability for your application. The material composition of the ring terminal is a primary consideration; both OEM and aftermarket options vary in terms of materials such as copper alloys, aluminum, or stainless steel, which can impact conductivity, durability, and resistance to environmental factors. The quality of the termination and insulation is also paramount; OEM ring terminals are often designed with the specific equipment in mind, offering tailored performance, while aftermarket options may provide a broader range of compatibility but could vary in quality.
Another important factor is the compliance with industry standards. OEM ring terminals are typically engineered to meet strict manufacturing and safety standards set by the original equipment manufacturer. Aftermarket alternatives should also adhere to these or equivalent standards, but it’s essential to verify this for your specific needs. Additionally, the rating of the ring terminal, including voltage and current capacity, must align with your project requirements. Consider as well the environmental conditions the terminals will endure; both OEM and aftermarket options should be suitable for the temperature ranges, moisture levels, and chemical exposures expected in your operational environment. Lastly, the cost, availability, and lead time are practical considerations that can influence your decision. While OEM ring terminals may be more expensive initially, they could offer long-term savings through superior performance and longevity. Aftermarket options might provide a cost-effective solution but require careful selection to ensure compatibility and reliability.