OEM vs Aftermarket Ring Terminals: Quality, Cost, and Durability Compared
Ring terminals are robust electrical connectors designed for durability and weather resistance, cru…….
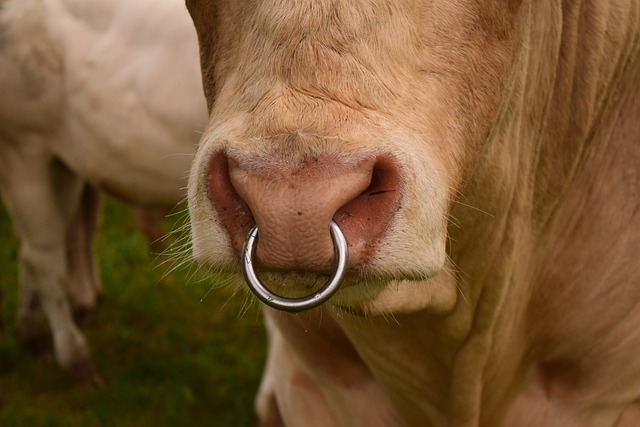
Ring terminals are robust electrical connectors designed for durability and weather resistance, crucial for maintaining secure and reliable connections in a wide array of applications, from automotive to heavy machinery and residential systems. These connectors are available in various materials, including copper alloy, stainless steel, or aluminum, ensuring compatibility with different operational conditions. When choosing between OEM and aftermarket ring terminals, it's important to consider factors like quality, compatibility, and cost. OEM ring terminals offer exact specifications and high reliability, often complying with rigorous industry standards and safety certifications like UL or CSA. Aftermarket options provide a diverse selection that may be more economical but require careful selection based on material composition, resistance to environmental factors, grip strength, and insulation quality. The longevity of OEM ring terminals typically justifies their higher cost due to premium materials and meticulous engineering, while aftermarket alternatives offer a range of options suitable for various needs. Ultimately, the decision between OEM and aftermarket should be informed by the specific demands of your application, including environmental conditions, mechanical loads, and compliance with industry standards to ensure both project success and safety.
When it comes to electrical connections, ring terminals serve as critical components ensuring secure and reliable wiring. This article delves into the pivotal distinction between OEM (Original Equipment Manufacturer) and aftermarket ring terminals, guiding readers through their functionality, applications, quality specifications, economic considerations, and durability assessments. Whether you’re an engineer or a DIY enthusiast, understanding the nuances of OEM versus aftermarket options will aid in making informed decisions for your specific project needs. Join us as we navigate the various aspects that set these terminal types apart, from their performance expectations to the cost-benefit analysis and application-specific suitability.
- Understanding Ring Terminals: An Overview of Functionality and Usage
- OEM vs Aftermarket: Defining the Scope of Choices for Ring Terminals
- Quality and Specifications: What to Look for in OEM and Aftermarket Ring Terminals
- Cost Analysis: Assessing the Economic Implications of OEM vs Aftermarket Ring Terminals
- Durability and Longevity: Testing and Performance Expectations from OEM and Aftermarket Options
- Application-Specific Considerations: Selecting the Right Ring Terminal for Your Project
Understanding Ring Terminals: An Overview of Functionality and Usage
Ring terminals are robust electrical connectors designed to provide a secure and weatherproof enclosure for ring or circuit conductor terminations. They serve as a critical component in electrical systems, ensuring the integrity of connections where flexibility, durability, and protection against environmental factors are paramount. These terminals are engineered with a grooved fitting that slips over the end of a conductor, followed by a series of bends to form a ring. The functional design of ring terminals accommodates various applications, from industrial machinery to consumer electronics, where secure and reliable electrical connections are essential.
In terms of usage, ring terminals can be found in a myriad of settings, including in the automotive industry for battery connections, in heavy machinery for control circuitry, and in residential electrical installations. They are available in different materials, such as copper alloy, stainless steel, or aluminum, catering to diverse operational requirements, whether it be for high-temperature environments or harsh chemical exposures. The choice between OEM (Original Equipment Manufacturer) and aftermarket ring terminals involves considerations of compatibility, quality, and cost. OEM ring terminals are often produced by the original manufacturer of the equipment, ensuring a direct fit and match in terms of specifications. Aftermarket alternatives, on the other hand, offer a wider range of choices, potentially at a lower cost, but may require verification for proper functionality and compatibility with the intended application. Users must weigh the benefits of brand-specific, precision-engineered OEM terminals against the versatility and often competitive pricing of aftermarket options to make an informed decision that aligns with their specific needs.
OEM vs Aftermarket: Defining the Scope of Choices for Ring Terminals
When selecting ring terminals, professionals and DIY enthusiasts are often faced with a choice between Original Equipment Manufacturer (OEM) and aftermarket options. Both types serve the function of providing reliable electrical connections, but they differ significantly in terms of quality, compatibility, and cost. OEM ring terminals are specifically designed by the original manufacturer of the equipment to meet exact specifications, ensuring optimal performance and safety. These terminals are engineered to fit precisely with the intended application, offering a high degree of reliability and often adhering to stringent industry standards.
On the other hand, aftermarket ring terminals are produced by third-party manufacturers and offer an alternative to OEM parts. Aftermarket options can provide a wider variety of choices in terms of designs, materials, and pricing. While they may not always match the exact specifications of OEM counterparts, reputable aftermarket ring terminals can still deliver performance comparable to OEM products. The key is to carefully evaluate the aftermarket option for its suitability with your application, considering factors like material durability, electrical conductivity, and compliance with safety regulations. Both OEM and aftermarket ring terminals have their merits; the choice ultimately depends on the specific needs of the project, the required fit, function, and form, as well as budgetary constraints. It’s crucial to assess the application requirements, the environment in which the terminal will operate, and the manufacturer’s reputation and certifications when making your decision. This will help ensure that you select a ring terminal that provides both functionality and longevity.
Quality and Specifications: What to Look for in OEM and Aftermarket Ring Terminals
When assessing quality and specifications in ring terminals, whether OEM (Original Equipment Manufacturer) or aftermarket, it’s crucial to evaluate several key factors to ensure optimal performance and reliability. OEM ring terminals are designed and built by the original manufacturer of the equipment, offering a direct fit with the exact specifications required for that particular application. These terminals are often tailored to match the design, quality, and performance standards of the original product, which can lead to superior compatibility and longevity. When selecting OEM ring terminals, look for certifications like UL (Underwriters Laboratories) or CSA (Canadian Standards Association), which indicate adherence to safety and performance standards.
In contrast, aftermarket ring terminals are manufactured by third-party companies and offer a wide array of choices, often at different price points. While they may not always match the exact specifications of their OEM counterparts, aftermarket options can provide similar quality and functionality. Key aspects to consider in aftermarket ring terminals include the material composition, such as copper alloy or aluminum, which affects conductivity and durability; the size and type of ring, including its resistance to environmental factors like corrosion; and the grip strength, which ensures secure connections even under vibration or motion. Additionally, inspecting the insulation quality and the presence of any relevant industry standards compliance, such as IEC (International Electrotechnical Commission) norms, is essential for aftermarket ring terminals. Both OEM and aftermarket ring terminals have their place in maintenance and repairs; the choice between them should be guided by the specific needs of your application and the level of compatibility required.
Cost Analysis: Assessing the Economic Implications of OEM vs Aftermarket Ring Terminals
When considering the economic implications of choosing between OEM (Original Equipment Manufacturer) and aftermarket ring terminals, a detailed cost analysis is essential. OEM ring terminals are designed by the original manufacturer of the equipment and are specifically tailored to meet their exacting standards. They often come with a higher price tag due to the stringent quality control processes, brand reputation, and warranty that they carry. These terminals ensure compatibility and performance that aligns with the equipment’s specifications, which can prevent costly repairs or replacements in the future.
In contrast, aftermarket ring terminals offer a more economical alternative. They are manufactured by third-party companies and can provide similar functionality at a lower cost. The key differentiator is that aftermarket options may vary in terms of quality and performance when compared to their OEM counterparts. While they might be more affordable upfront, the decision to opt for aftermarket ring terminals should consider the potential long-term savings versus the risk of subpar performance or early replacement. It’s crucial to weigh the initial cost savings against the reliability and longevity offered by OEM products to make an informed decision that aligns with your budget and the operational requirements of your equipment.
Durability and Longevity: Testing and Performance Expectations from OEM and Aftermarket Options
When assessing durability and longevity in ring terminals, both OEM (Original Equipment Manufacturer) and aftermarket options are subject to rigorous testing to meet performance expectations. OEM ring terminals are designed to match the exact specifications of the original equipment they replace or complement. These terminals undergo stringent quality control processes during manufacturing to ensure consistency in their electrical conductivity, mechanical strength, and resistance to environmental factors like moisture and corrosion. The OEM’s commitment to using high-grade materials and precise engineering leads to a product that often exhibits superior longevity, as it is tailored to perform reliably under the exact conditions for which it was made.
In contrast, aftermarket ring terminals offer a competitive alternative, often at a lower cost. While these terminals are held to industry standards and must demonstrate compatibility with various applications, they may vary in quality and performance. Aftermarket manufacturers typically offer a range of products, from economy models to those that rival OEM quality. The key differentiator is the testing protocols, which, while still robust, might not be as stringent as OEM processes. Aftermarket ring terminals are a cost-effective solution for many applications, but users must carefully select options based on their specific application requirements to ensure long-term performance and reliability. When choosing between OEM and aftermarket ring terminals, it’s crucial to consider the intended use environment, the operating conditions, and the necessary electrical and mechanical specifications to make an informed decision that balances cost with durability.
Application-Specific Considerations: Selecting the Right Ring Terminal for Your Project
When selecting the appropriate ring terminal for your project, it’s crucial to consider the specific demands of your application. Ring terminals serve as vital components in electrical installations, providing a secure connection between wires and various types of equipment. The right choice ensures both the reliability and safety of the system. For instance, if your project involves high-temperature environments, opting for ring terminals with high-heat resistance materials is essential to prevent degradation or failure over time. Similarly, when working in hazardous locations where fire or explosion risks are present, flame-resistant and explosion-proof ring terminals are imperative to safeguard both the installation and personnel.
The compatibility of the ring terminal with the wire gauge and type is another critical factor. Different applications demand different wire sizes and types, such as stranded versus solid copper wires. The chosen ring terminal must securely hold the wire in place while facilitating electrical conductivity without compromising the wire’s integrity. Additionally, the mechanical load that the terminal will endure should be assessed. This includes considering factors like vibration, shock, and tension, which can affect both OEM (Original Equipment Manufacturer) and aftermarket ring terminals differently. For instance, OEM ring terminals are often designed specifically for certain equipment, potentially offering optimized performance and fit within that system. On the other hand, aftermarket options may provide a wider range of choices, including specialized features tailored to unique or less common applications. Regardless of whether you choose OEM or aftermarket, ensuring that the ring terminal meets the necessary standards and certifications for your industry is non-negotiable. This due diligence will help guarantee that the selected ring terminal will perform reliably under the specific conditions it will face in your project.