Navigating Global Standards for Ring Terminal Safety and Selection
Ring terminals are crucial components for reliable and safe electrical connections, widely used acr…….
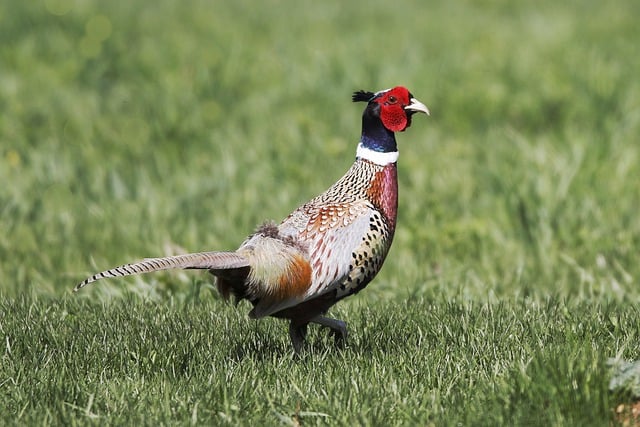
Ring terminals are crucial components for reliable and safe electrical connections, widely used across automotive, industrial, renewable energy, and telecommunications sectors. These terminals ensure secure and weatherproof connections between conductors and devices like motors and instruments. They adhere to rigorous industry standards that dictate their material composition, mechanical strength, environmental resistance, and safety features. Compliance with certifications from organizations such as UL, IEC, VDE, and CE ensures these terminals perform effectively under different application contexts, enhancing the overall integrity and operational efficiency of electrical systems. Advanced ring terminals now feature locking mechanisms, durable finishes, and adaptability to various wire sizes and environmental conditions, reflecting ongoing innovation in design for optimal performance and safety. Adherence to regional and national regulations like NEMA standards in the U.S. and ENs and LVD in Europe is essential for ensuring compliance with safety and environmental benchmarks globally. Selection of materials such as copper alloys, aluminum, or stainless steel for ring terminals is critical based on the application's specific needs, ranging from high-current to harsh environmental conditions. Properly selected and certified ring terminals guarantee long-term reliability and cost-effectiveness within their respective fields.
Ring terminals serve as pivotal components in electrical systems, ensuring secure and reliable connections. This article delves into the critical aspects of ring terminal standards and certifications, a subject of paramount importance for safety and efficiency in various industries. We’ll explore the fundamental role of ring terminals, their evolution, and the international standards governing their performance and safety. Additionally, we will examine how these components adhere to national and regional regulations and the intricacies of the certification process, highlighting essential marks that signify compliance and quality. Furthermore, understanding material considerations and appropriate applications for ring terminals is crucial for optimal performance in diverse settings. Join us as we unravel the nuances surrounding ring terminal standards and certifications.
- Understanding the Essence of Ring Terminals in Electrical Systems
- The Evolution and Functionality of Ring Terminals
- International Standards for Ring Terminal Performance and Safety
- Compliance with National and Regional Regulations
- Certification Process and Key Marks for Ring Terminals
- Selecting the Right Ring Terminal: Material Considerations and Applications
Understanding the Essence of Ring Terminals in Electrical Systems
Ring terminals play a pivotal role in the reliability and safety of electrical systems across various industries. These components are designed to provide a secure and weatherproof connection between electrical conductors and devices such as motors, instruments, and machinery. The construction of a ring terminal typically involves a metal ring with an insulating handle; the ring slides over the conductor and is crimped in place, ensuring a tight and durable fit. This design not only facilitates easy installation and maintenance but also enhances the electrical performance by minimizing corrosion and reducing the likelihood of accidental disconnection or loosening.
Incorporating ring terminals that adhere to industry standards is crucial for guaranteeing the longevity and efficiency of electrical installations. The standards and certifications for ring terminals are established to ensure that they meet specific criteria related to electrical conductivity, mechanical strength, environmental resistance, and safety. These standards may vary depending on the application; for instance, ring terminals used in marine environments must withstand corrosive saltwater conditions, while those in industrial settings require higher load-bearing capacities. By adhering to these stringent standards, manufacturers provide consumers with terminal solutions that are up to the task of handling the demands of their respective applications, thereby contributing to the overall integrity and functionality of electrical systems.
The Evolution and Functionality of Ring Terminals
Over the years, ring terminals have undergone significant evolution to meet the changing demands of electrical connectivity across various industries. Initially conceived as basic cable end protection, they have transformed into sophisticated components designed for both functionality and safety. Today’s ring terminals are engineered to accommodate a wide range of wire sizes, insulation types, and environmental conditions. The development of these terminals has been guided by stringent industry standards, which ensure consistent quality and performance across different applications. These standards address aspects such as mechanical strength, electrical conductivity, and resistance to environmental factors like temperature extremes and corrosive substances.
The functionality of ring terminals is a testament to their design evolution. They provide secure connections that are resistant to vibration and movement, which is crucial for applications ranging from household electronics to industrial machinery. Modern ring terminals often incorporate features such as locking mechanisms to prevent accidental disconnection and various finishes to improve durability in harsh conditions. Compliance with certifications like UL (Underwriters Laboratories) and CSA (Canadian Standards Association) ensures that these terminals adhere to safety and performance benchmarks, making them indispensable for ensuring the integrity of electrical systems. The continuous innovation in ring terminal design continues to push the boundaries of what is possible, enhancing their role as a critical link in the safety and efficiency of global electrical infrastructure.
International Standards for Ring Terminal Performance and Safety
Ring terminals serve as critical components in electrical connections, ensuring the safe and efficient transfer of electricity in various applications. The performance and safety of these terminals are governed by a suite of international standards that dictate their design, materials, and testing procedures. These standards, developed by organizations such as the International Electrotechnical Commission (IEC) and the National Electrical Manufacturers Association (NEMA), are integral to ensuring that ring terminals meet stringent performance criteria and adhere to safety requirements across different industries and environments.
The IEC’s published standards for ring terminals cover a range of aspects, including mechanical and electrical specifications, material compatibility with different environments, and the testing methods to verify compliance with these standards. These include assessments for load capacity, insulation resistance, environmental sealing, and durability under various conditions. Additionally, safety standards are paramount; they address potential risks such as fire hazards, electrical shocks, and the integrity of connections in harsh or fluctuating temperatures. Compliance with these international benchmarks not only ensures the quality and reliability of ring terminals but also contributes to the longevity and safety of the systems in which they are used. Adherence to such standards is a testament to the manufacturer’s commitment to excellence and consumer protection, making them indispensable in maintaining the integrity of electrical installations globally.
Compliance with National and Regional Regulations
When integrating ring terminals into electrical systems, compliance with national and regional regulations is paramount to ensure safety, reliability, and performance. Ring terminals, which serve as critical connections between wires and various conductive elements, must adhere to stringent standards that vary by geography. In the United States, for instance, these components are subject to the National Electrical Manufacturers Association (NEMA) standards and the National Electrical Code (NEC), which provide guidelines on proper installation, materials, and performance criteria. The NEC, specifically, outlines requirements to minimize fire hazards and reduce the risk of electrical shock. Similarly, in Europe, ring terminals must comply with the European Norms (ENs) and the Low Voltage Directive (LVD), which dictate safety and environmental protection standards. These regulations ensure that ring terminals meet the necessary performance levels for their intended use, reflecting a commitment to quality and safety that is recognized globally. Manufacturers must stay abreast of these regulations to guarantee their products are market-ready across different regions and to avoid legal ramifications or product recalls due to non-compliance. Adherence to these standards not only protects end-users but also positions manufacturers as responsible entities within the industry, emphasizing the importance of understanding and implementing compliance measures in the design and production process of ring terminals.
Certification Process and Key Marks for Ring Terminals
Ring terminals are critical components in electrical installations, ensuring secure and reliable connections for conductors to various devices and systems. The certification process for ring terminals is a rigorous series of tests designed to validate their performance, safety, and interchangeability. This process involves assessments against international standards, which often include mechanical stress tests, electrical load tests, and environmental endurance tests. These evaluations are conducted to ascertain that the ring terminals meet the necessary requirements for their intended applications.
Key marks or certification symbols on ring terminals are indicators of compliance with specific standards. Recognized symbols like IP (Ingress Protection) ratings denote the level of protection against intrusion from foreign bodies and moisture, while others signify adherence to electrical safety standards such as those set by organizations like Underwriters Laboratories (UL) or the International Electrotechnical Commission (IEC). These marks ensure that users can identify ring terminals that have been tested and certified for their intended use. For instance, a VDE mark on a ring terminal indicates it complies with the German Electrotechnical Testing Association’s standards, which are highly regarded globally. Similarly, CE marking signifies conformity with European Union safety, health, and environmental protection requirements. These marks facilitate the global acceptance of ring terminals by providing clear evidence of their quality and compliance with relevant industry standards.
Selecting the Right Ring Terminal: Material Considerations and Applications
When selecting the appropriate ring terminal, material considerations are paramount to ensure durability and performance under various environmental conditions. Ring terminals are designed from a range of materials, including copper alloys, aluminum, and stainless steel, each with its own set of properties that make it suitable for specific applications. For instance, copper alloy ring terminals offer superior conductivity, making them ideal for use in situations demanding high electrical currents. Aluminum options, on the other hand, provide a lighter weight alternative without compromising on conductivity, which is particularly advantageous in applications where weight reduction is critical, such as in portable electronic devices or battery-operated equipment. Stainless steel ring terminals boast exceptional resistance to corrosion and are well-suited for environments exposed to harsh elements like saltwater or industrial chemicals. The choice of material not only affects the terminal’s durability and conductivity but also its overall lifespan and maintenance requirements, which are essential factors in the long-term cost-effectiveness of any electrical installation.
In addition to material considerations, the intended application of the ring terminal is a key determinant in the selection process. These terminals are employed across various sectors, including automotive, industrial machinery, renewable energy systems, and telecommunications infrastructure. The automotive industry, for example, demands high-quality ring terminals that can withstand vibrations, shocks, and varying temperatures, ensuring consistent electrical connections in engine compartments or within the vehicle’s electrical system. Industrial applications may prioritize ring terminals that can endure heavy loads and resist mechanical wear, while renewable energy systems might focus on those that are resistant to environmental factors like UV light, humidity, and wind. The diverse range of standards and certifications for ring terminals, such as those from UL (Underwriters Laboratories) or IEC (International Electrotechnical Commission), ensures that there is a ring terminal available to meet the specific needs of any given application, guaranteeing safety, reliability, and optimal performance.