Maximizing Industrial Efficiency with Advanced Ring Terminal Solutions
Ring terminals are indispensable for maintaining robust and dependable electrical connections acros…….
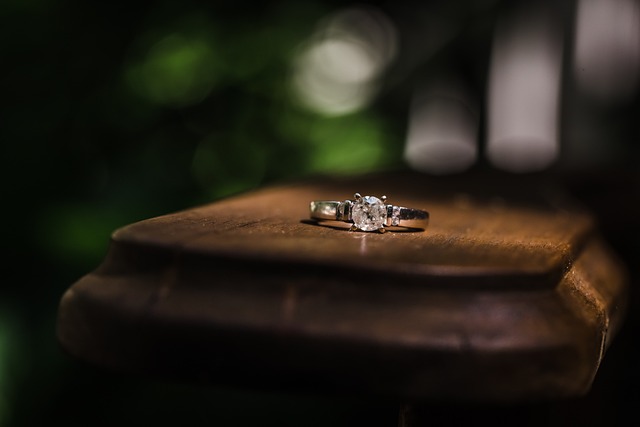
Ring terminals are indispensable for maintaining robust and dependable electrical connections across a variety of industrial applications. These terminals ensure safe power transmission by protecting against environmental factors like moisture, dust, and chemicals, and cater to diverse needs through different mounting options and voltage/current ratings. The choice of material, such as copper alloys or stainless steel, is crucial for longevity and performance in specific conditions, with the need for stringent industry standards compliance to ensure safety. Selection considerations include wire gauge compatibility, environmental resilience, and mechanical stress resistance. A secure fit with a reliable clamping mechanism is vital to prevent loosening or failure, while the interface between the ring terminal and the wire must be carefully engineered for minimal resistance. Advanced materials and insulation, along with sophisticated design software, enhance the durability, safety, and reliability of these components in challenging environments. Proper installation, maintenance, and adherence to manufacturer guidelines are essential for prolonging their lifespan and ensuring consistent performance in industrial settings. The commitment to innovation in ring terminal technology continues to meet the demands for both longevity and safety in critical industrial applications.
Ring terminals are indispensable components in the industrial landscape, ensuring secure electrical connections that withstand rigorous conditions. This article delves into their critical role, material science advancements, and the diverse applications driving innovation within this field. From design and material selection for peak performance to the practical aspects of installation, maintenance, and troubleshooting, gain insights into selecting the right ring terminal for your industry’s needs and learn about the latest enhancements in durability and safety. Understanding the intricacies of ring terminals is not just about connectivity; it’s a matter of optimizing industrial operations for reliability and efficiency.
- Understanding the Essence of Ring Terminals in Industrial Settings
- Design and Material Considerations for Optimal Performance
- The Functionality of Ring Terminals: Types, Uses, and Applications
- Factors Influencing the Selection of Ring Terminals for Different Industries
- Innovations in Ring Terminal Technology for Enhanced Durability and Safety
- Best Practices for Installing, Maintaining, and Troubleshooting Ring Terminals
Understanding the Essence of Ring Terminals in Industrial Settings
Ring terminals serve as critical components in the electrical infrastructure of industrial settings, ensuring robust and reliable connections for various equipment and machinery. These terminal ends are designed to provide a secure and weatherproof interface between electrical conductors and equipment, facilitating the safe transfer of electrical current. The durability of ring terminals is paramount; they must withstand the rigorous demands of industrial environments, which often include exposure to harsh elements such as moisture, dust, and chemicals. This robustness allows for consistent performance across a wide array of applications, from heavy-duty machinery to sensitive control systems.
The selection of ring terminals is influenced by a range of factors, including the voltage, current rating, environmental conditions, and the specific mechanical requirements of the application. For instance, ring terminals designed for high-current applications will have larger contacts and more robust insulation to handle the increased power flow without overheating. Additionally, their versatility is evident in the variety of mounting options available, such as flange mounts or threaded studs, which cater to different installation contexts within industrial settings. This adaptability ensures that there is a ring terminal to suit every electrical connection need in the demanding world of industry.
Design and Material Considerations for Optimal Performance
When selecting ring terminals for industrial applications, design and material considerations play a pivotal role in ensuring optimal performance under various conditions. The design of ring terminals must accommodate the specific requirements of the application, including the gauge of the wire to be used, environmental factors such as temperature extremes and exposure to corrosive substances, and the mechanical stresses encountered during operation. A robust design with a secure clamping mechanism is essential to prevent electrical contacts from loosening or failing over time. Additionally, the terminal’s interface with the conductor should be engineered to minimize resistance and ensure a reliable electrical connection.
Material selection for ring terminals is equally critical. Common materials include various copper alloys, stainless steel, and sometimes aluminum, each chosen for its specific properties. Copper alloys are often preferred for their excellent electrical conductivity and durability, while stainless steel offers superior resistance to corrosion in harsh environments. The choice of material must align with the application’s environmental conditions and longevity requirements. For instance, applications in marine or chemical processing environments may necessitate the use of high-grade stainless steel to prevent corrosion and maintain performance integrity over time. In all cases, the materials used should adhere to industry standards and certifications, ensuring that the ring terminals meet the necessary safety and reliability benchmarks for industrial use.
The Functionality of Ring Terminals: Types, Uses, and Applications
Ring terminals are robust electrical connectors that serve as critical components in various industrial applications, ensuring secure and reliable connections between wires and equipment. These terminals, characterized by their ring-shaped design, are engineered to withstand harsh environments and repeated use, making them indispensable in sectors such as automotive, aerospace, and heavy machinery. They offer a versatile solution for making weatherproof connections that can be easily installed and maintained.
There are several types of ring terminals, each designed to meet specific needs within industrial settings. These include insulated and uninsulated options, with the insulated variants providing protection against electrical shock and environmental factors. The application scope for ring terminals is vast, ranging from securing wires in control panels and switchgear to being used in outdoor installations like traffic lights or solar panel systems. Their ability to resist corrosion, accommodate different wire sizes, and withstand a variety of temperatures make them an essential choice for both static and dynamic applications where safety and efficiency are paramount. Industrial users benefit from the ease of installation and the long-term durability that ring terminals offer, ensuring consistent performance even under the most demanding conditions.
Factors Influencing the Selection of Ring Terminals for Different Industries
When selecting ring terminals for industrial applications, several critical factors must be considered to ensure optimal performance and safety in a given environment. The first factor is the electrical rating, which must align with the current capacity requirements of the application. Ring terminals are available in various amperage ratings, from small gauge wires to large industrial cables, ensuring that the selected terminal can handle the maximum expected current without overheating or failing.
Another important consideration is the environmental conditions in which the ring terminals will operate. Factors such as temperature extremes, exposure to chemicals, moisture, and mechanical stress all influence the choice of materials for the ring terminals. Stainless steel options are often preferred for their corrosion resistance, while other environments may necessitate specialized plastics or coatings to protect against environmental degradation. Additionally, the mechanical design of the terminal must be compatible with the space available and the movement or flexibility required by the application. For instance, automotive industries might require terminals that can withstand frequent bending or vibration, while stationary equipment may demand a more robust, fixed installation. The choice of ring terminals is thus a complex decision that balances electrical specifications, environmental resistance, and mechanical integrity to deliver reliable connections under diverse industrial conditions.
Innovations in Ring Terminal Technology for Enhanced Durability and Safety
Innovations in ring terminal technology continue to advance, addressing the critical needs for enhanced durability and safety within industrial applications. The evolution of these components is a testament to the relentless pursuit of reliability and performance under demanding conditions. Ring terminals are engineered with robust materials, including high-strength alloys, that offer superior resistance to environmental factors such as corrosion, extreme temperatures, and mechanical stresses. These advancements ensure that connections remain intact, even in the most challenging environments, thus preventing potential failure and ensuring operational integrity. The incorporation of advanced insulation technologies has further improved their safety profile by reducing the risk of electrical faults or arcing. Manufacturers are also leveraging sophisticated design software to optimize the cable-to-terminal interface, resulting in a more secure and efficient connection that withstands repeated cycles of vibration and movement, which is particularly important in mobile machinery and harsh industrial settings. This commitment to innovation ensures that ring terminals continue to meet and exceed industry standards for both durability and safety, making them indispensable components in the modern industrial landscape.
Best Practices for Installing, Maintaining, and Troubleshooting Ring Terminals
When installing ring terminals for industrial applications, it is imperative to adhere to best practices to ensure reliable performance and longevity. Begin by selecting the appropriate ring terminal that matches the conductor size and insulation type for your application. Proper installation starts with cleaning and stripping the conductor insulation to the specified length, ensuring a secure and conductive connection. The ring should be slipped over the conductor, and the mounting bracket or set screws must be tightened according to manufacturer specifications to prevent loosening under vibration or thermal cycling.
Maintaining ring terminals involves regular inspections for signs of wear, corrosion, or damage. Any exposed conductors or damaged insulation should be addressed immediately to prevent electrical hazards or performance issues. Cleaning the terminal and its surrounding environment regularly with appropriate cleaning agents can remove dirt and debris that may cause corrosion over time. Lubrication of movable parts, if applicable, will further protect against wear. For troubleshooting, consult the manufacturer’s guidelines for specific advice on common issues such as intermittent connections or poor conductivity. It is also wise to replace ring terminals during routine maintenance when they show signs of aging or have reached their service life as outlined by industry standards, to prevent unexpected failures. Regular monitoring and proactive maintenance can extend the lifespan of ring terminals and ensure they continue to provide a reliable electrical connection in demanding industrial environments.