Mastering Ring Terminal Crimp Quality: Testing for Unwavering Reliability
Ring terminal crimping is a critical process for creating secure electrical connections, enhancing s…….
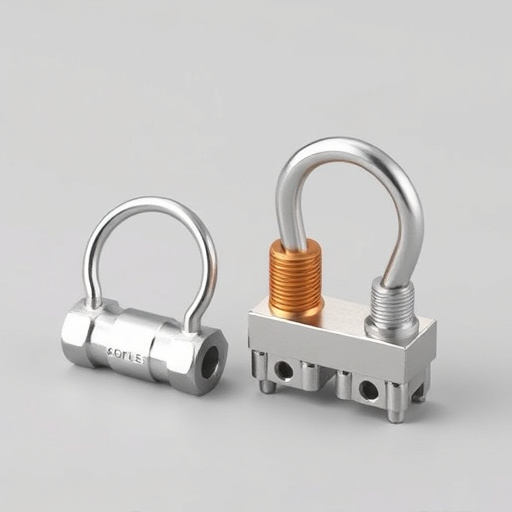
Ring terminal crimping is a critical process for creating secure electrical connections, enhancing system performance and safety. This method, involving specialized tools and strict standards, ensures low resistance, optimal current flow, and longevity against vibration and stress. Quality testing, from visual inspections to stress testing, guarantees reliable ring terminals. Maintaining these connections through regular checks and proper maintenance prevents failures caused by loose connections, corrosion, or damage, emphasizing the importance of ring terminals in electrical networks.
In the realm of electrical connections, ring terminal crimping is a vital process ensuring robust and reliable joints. This article explores the intricacies of ring terminal crimp quality testing, a critical step in maintaining efficient and safe wiring systems. From understanding the fundamental process to identifying common issues, we delve into the essential practices for ensuring the integrity of your ring terminals. Mastering these techniques is paramount for any professional, as it directly impacts system performance and safety.
- Understanding Ring Terminal Crimping and Its Importance
- The Process of Quality Testing for Ring Terminals
- Ensuring Reliability: Common Issues and Troubleshooting Tips
Understanding Ring Terminal Crimping and Its Importance
Ring terminal crimping is a critical process in electrical wiring, ensuring secure and reliable connections between wires and components. It involves using specialized tools to create a crimped connection on a ring terminal, which is then used to terminate or join wires. This method is widely employed in various industries due to its efficiency and strength. The quality of this crimping process directly impacts the overall performance and safety of electrical systems, making it an essential aspect for professionals to master.
Proper ring terminal crimping ensures a solid mechanical bond and low resistance at the connection point, allowing for optimal current flow. It is particularly vital in demanding applications where connections are frequently subjected to vibration or stress. By adhering to strict crimp quality standards, technicians can prevent issues like loose connections, arcing, or even electrical failures, ensuring the reliability and longevity of the wiring system.
The Process of Quality Testing for Ring Terminals
The process of quality testing for ring terminals involves a series of meticulous steps designed to ensure their reliability and performance under various conditions. It begins with visual inspection, where technicians scrutinize the terminal for any signs of damage, deformation, or manufacturing defects. This initial check is crucial as even minor issues can compromise the integrity of the connection.
Next, electrical testing is conducted to verify the terminal’s conductivity and insulation properties. This includes measuring resistance, capacitance, and other electrical parameters to ensure they meet the specified standards. Additionally, stress testing assesses the terminal’s endurance under mechanical strain, simulating real-world conditions to guarantee their durability. The use of specialized equipment and precise measurement techniques is essential throughout this process to identify any shortcomings in the ring terminals’ quality.
Ensuring Reliability: Common Issues and Troubleshooting Tips
Ensuring reliability in electrical connections is paramount, especially with ring terminals, which are crucial for secure and efficient wiring. Common issues include loose connections, corrosion, or damage to the terminal’s insulation. These problems can lead to poor conductivity, arcing, and even electrical failures. To maintain optimal performance, regular inspection and maintenance are essential.
Troubleshooting tips involve checking for any visible signs of wear or damage, ensuring tight crimping, and applying protective coatings to prevent corrosion. Using the right tools for crimping and following manufacturer guidelines can significantly enhance reliability. Additionally, testing with specialized equipment before and after installation can identify potential issues early on, guaranteeing the integrity of the electrical network.