Mastering Heat Shrink Ring Terminals: Applications and Future Trends
Heat shrink ring terminals are innovative electrical connectors that offer compact, reliable solutio…….
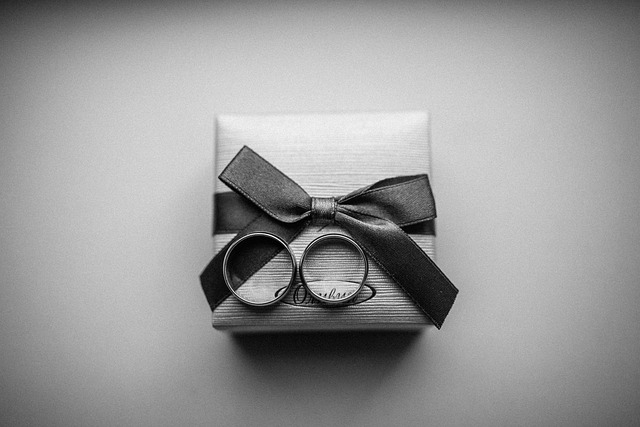
Heat shrink ring terminals are innovative electrical connectors that offer compact, reliable solutions for confined spaces. Crafted with a metal core in a heat-shrinkable tube, these terminals form secure seals around conductors upon heating. Their design enhances installation simplicity and system longevity, making them ideal for demanding industries like automotive, aerospace, and industrial applications. Although they require specialized equipment for installation, heat shrink ring terminals provide significant advantages in cable management and are crucial for achieving secure and durable connections in tight-space electrical applications. With ongoing technological advancements, these terminals are poised to revolutionize smart manufacturing through integrated functionality and real-time monitoring capabilities.
“Discover the versatile world of heat shrink ring terminals—a game-changer in electrical engineering. This comprehensive guide explores their unique capabilities, from the science behind their shrinking magic to diverse applications. We dissect advantages over traditional terminals, providing a step-by-step installation process for ensuring top-notch quality.
Uncover future trends and innovations shaping ring terminal technology while navigating best practices for reliable performance. Get ready to shrink your knowledge gaps and expand your understanding of these indispensable connectors.”
- Understanding Heat Shrink Ring Terminals: A Comprehensive Overview
- The Science Behind Their Functionality
- Applications in Electrical Engineering
- Advantages and Disadvantages Compared to Traditional Terminals
- Installation Process: Step-by-Step Guide
- Best Practices for Ensuring Quality and Reliability
- Future Trends and Innovations in Ring Terminal Technology
Understanding Heat Shrink Ring Terminals: A Comprehensive Overview
Heat shrink ring terminals are a specialized type of electrical connection that offers both convenience and reliability. They’re designed for use in tight spaces, providing a secure and compact alternative to traditional terminal methods. These terminals consist of a metal core surrounded by a flexible, heat-shrinkable tube. The unique feature is their ability to shrink down to a fraction of their original size when heated, creating a tight seal around the conductor.
This innovative design ensures a robust connection, making them ideal for demanding applications like automotive, aerospace, and industrial settings. Ring terminals are known for their ease of installation; simply insert the wire into the terminal, apply heat, and the tube shrinks, locking the terminal in place. This process creates an insulated joint, enhancing the terminal’s lifespan and overall system reliability.
The Science Behind Their Functionality
Heat shrink ring terminals are a remarkable innovation in the world of electrical connections, offering both strength and flexibility. Their functionality is rooted in a simple yet powerful scientific principle: thermal contraction. When heated, the plastic material of these terminals shrinks, tightly sealing around wires and creating an insulated, secure bond. This process ensures reliable electrical conductivity while also protecting against environmental factors like moisture and corrosion.
The science behind ring terminals provides a robust solution for various applications. The heat-activated shrink material allows for precise fitting, accommodating different wire sizes without compromising integrity. This adaptability makes them versatile, suitable for both residential and industrial settings. Additionally, the thermal process creates a strong mechanical bond, ensuring connections withstand vibration, stress, and extreme temperatures.
Applications in Electrical Engineering
Ring terminals are an indispensable tool in electrical engineering, offering a versatile and efficient solution for wire connection and termination. These innovative devices find applications across various industries due to their ability to provide secure and reliable connections. From automotive to aerospace and beyond, ring terminals ensure robust wiring systems.
In electrical engineering projects, ring terminals simplify the process of making connections, particularly in tight or confined spaces. They are commonly used for wiring harness assembly, where multiple wires need to be organized and connected securely. The compact design of ring terminals allows for space-efficient routing of cables, ensuring a neat and professional finish. This is especially valuable in high-performance systems where reliability and aesthetics matter.
Advantages and Disadvantages Compared to Traditional Terminals
Heat shrink ring terminals offer several advantages over traditional terminal types. One key benefit is their compact design, which allows for more efficient cable management and reduced overall bundle diameter. This feature is particularly valuable in tight spaces, such as automotive applications or confined electrical panels. Additionally, ring terminals provide a secure and reliable connection by crimping directly onto wires, eliminating the need for solder or separate connectors. They are also available in a wide range of sizes and materials, ensuring compatibility with various wire gauges and environmental conditions.
However, there are disadvantages to consider. Heat shrink ring terminals require specialized equipment and training for proper installation, which can increase initial setup costs and complexity. Furthermore, while they offer excellent insulation once shrunk, the process itself demands careful control to avoid damage or overheating. In contrast, traditional terminals often have simpler installation methods and may be more readily available, making them a preferred choice for less specialized applications or where cost is a primary concern.
Installation Process: Step-by-Step Guide
The installation process for heat shrink ring terminals involves a few simple yet precise steps. First, prepare your wire by stripping about 1/4 inch of insulation from both ends using wire strippers. Then, insert the bare wires into the terminal’s holes—one for each conductor—ensuring they fit snugly. Next, apply heat to the terminal using a heat gun or torch; this causes the terminal’s plastic to shrink tightly around the wire, creating an insulated connection.
As you heat, keep an eye on the terminal to avoid over-shrinking. Once cooled, test the connection for any signs of wear or damage. This step-by-step process ensures a secure and durable connection using ring terminals, ideal for applications requiring reliable electrical connections in tight spaces.
Best Practices for Ensuring Quality and Reliability
When working with heat shrink ring terminals, adhering to best practices is essential for maintaining quality and reliability. Firstly, ensure proper preparation of the wire ends before inserting them into the terminals. Cleanliness and deburring are crucial to prevent any short circuits or loose connections. Use high-quality heat shrink tubes that match the recommended size for your terminal type, ensuring a secure fit after shrinking.
During the installation process, maintain consistent pressure and temperature during the heat shrinking process. Exceeding the specified temperature or applying uneven pressure can damage the terminal or the wire insulation. Regularly inspect terminals for any signs of damage, corrosion, or misalignment before testing the circuit to ensure long-term reliability and safety.
Future Trends and Innovations in Ring Terminal Technology
The future of ring terminals looks promising, with ongoing innovations pushing the boundaries of what’s possible in electrical connectivity. One emerging trend is the development of smarter, more durable materials. Researchers are exploring advanced polymer blends that offer improved heat resistance and mechanical strength, ensuring ring terminals can withstand harsh environmental conditions. These advancements are particularly relevant for industries like automotive and aerospace, where reliability and longevity are paramount.
Additionally, there’s a growing focus on miniaturization and enhanced functionality. Engineers are designing compact ring terminals with integrated sensors and communication capabilities, allowing for real-time monitoring and control of electrical systems. This trend is set to revolutionize industrial automation and smart manufacturing processes, as these intelligent terminals can provide data-driven insights and improve overall system efficiency.