Evolving Ring Terminals: Advanced Materials & Solderless Tech Revolution
The manufacturing of ring terminals has evolved significantly, transitioning from handcrafted solid …….
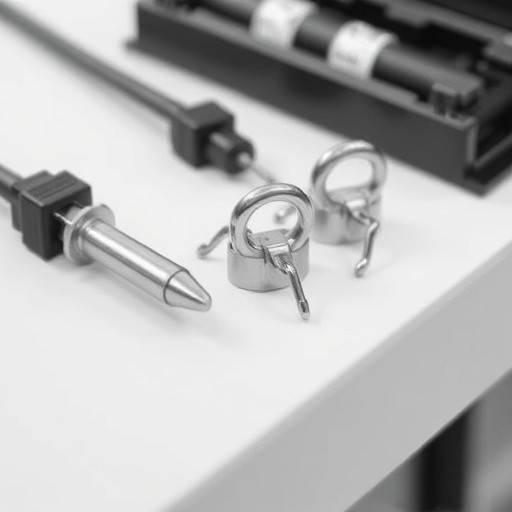
The manufacturing of ring terminals has evolved significantly, transitioning from handcrafted solid metal creations to highly automated, efficient processes. Mechanization in the 20th century brought about cost savings and increased accessibility. Modern advancements include advanced materials like high-performance polymers, lightweight composites, and corrosion-resistant metals, enabling lighter, stronger connectors for harsh environments. Automation and solderless technologies have further streamlined production, reducing human error, minimizing production times, and enhancing reliability, catering to diverse industry needs across automotive, aerospace, marine, and electronics sectors.
“Ring terminal manufacturing has evolved significantly over time, driven by advancements in technology and changing industry demands. This article delves into the historical perspective of ring terminal evolution, exploring how advanced materials, automation, and innovative connection methods have reshaped production. We discuss the trends in miniaturization and their impact on design, as well as sustainability practices within the industry. Furthermore, we provide a glimpse into emerging technologies and innovations that promise to redefine the future of ring terminals.”
- The Evolution of Ring Terminal Manufacturing: A Historical Perspective
- Advanced Materials Shaping Modern Ring Terminals
- Automation and Efficiency in Production Processes
- Solderless Technologies: Revolutionizing Connection Methods
The Evolution of Ring Terminal Manufacturing: A Historical Perspective
The manufacturing of ring terminals, essential components in electrical wiring and connections, has come a long way since their inception. Historically, these terminals were primarily crafted by hand, involving laborious processes that required skilled artisans. This era was characterized by custom-made ring terminals, often made from solid metals like copper or brass, offering limited production volumes and higher costs.
With advancements in technology, the 20th century brought mechanization to ring terminal manufacturing. The introduction of specialized machinery enabled mass production, significantly lowering costs and increasing accessibility. Over time, materials evolved from pure metals to alloys and then to more cost-effective options like tin-plated steel. Today, automation plays a pivotal role, allowing for precise crafting of various ring terminal types to cater to diverse industry needs, all while maintaining high quality standards.
Advanced Materials Shaping Modern Ring Terminals
In recent years, advancements in materials science have significantly shaped the future of ring terminal manufacturing. Engineers and manufacturers are now exploring a range of advanced materials to create more robust and versatile ring terminals. These innovative materials include high-performance polymers, lightweight composites, and corrosion-resistant metals, each offering unique advantages over traditional materials.
By leveraging these advanced materials, modern ring terminals are becoming lighter in weight, stronger, and more resistant to environmental factors. This evolution enables manufacturers to produce connectors that can withstand harsh conditions, such as extreme temperatures, moisture, and chemical exposure, making them suitable for diverse industries like automotive, aerospace, and marine. Additionally, the use of cutting-edge materials enhances the overall reliability and performance of ring terminals, ensuring secure and efficient electrical connections in various applications.
Automation and Efficiency in Production Processes
The manufacturing landscape of ring terminals has seen a significant shift towards automation and efficient production processes. Advanced robotic systems are now being integrated into assembly lines, allowing for faster and more precise connections, reducing human error and improving overall productivity. This technology ensures consistent quality in every ring terminal produced, setting new standards in the industry.
Automated production facilities can handle complex tasks such as crimping, swaging, and stripping with remarkable speed and accuracy. These processes are critical in creating reliable electrical connections, which is essential for various applications. By streamlining these steps, manufacturers can cut down production times and increase output without compromising on the integrity of the ring terminals.
Solderless Technologies: Revolutionizing Connection Methods
In recent years, the manufacturing landscape of ring terminals has seen a significant shift towards solderless technologies, marking a profound change in connection methods. This innovative approach is transforming the way these essential electrical components are assembled and integrated into various applications. Solderless ring terminal manufacturing offers several advantages, including faster assembly times, reduced labor costs, and improved reliability.
The technology leverages advanced materials and precision engineering to create terminals that secure connections without traditional soldering. This not only streamlines production processes but also enhances the overall durability and performance of the ring terminals. As a result, industries ranging from automotive to electronics are adopting solderless technologies, ensuring more efficient, cost-effective, and robust electrical systems.