Ensuring Ring Terminal Crimping Excellence: A Quality Control Guide
Ring terminals are critical for ensuring the safety and integrity of electrical connections in dive…….
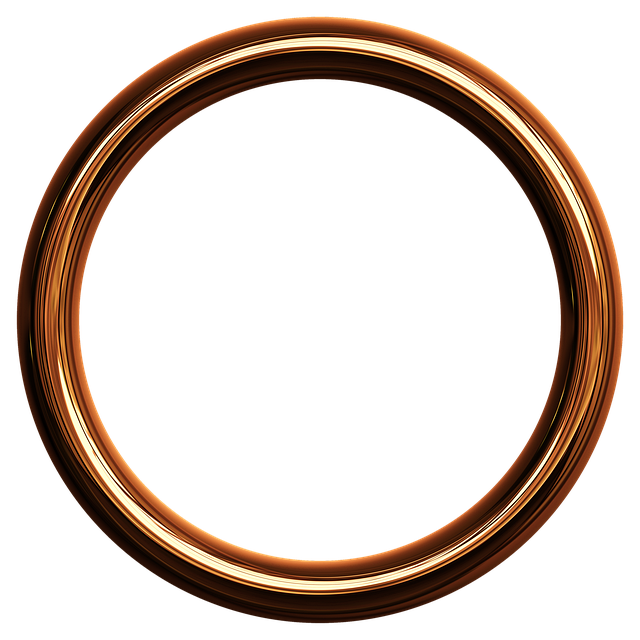
Ring terminals are critical for ensuring the safety and integrity of electrical connections in diverse applications. Manufacturers rigorously test these terminals against mechanical, electrical, and environmental stressors using advanced technology like high-resolution cameras and precision gauges to monitor the crimping process in real-time, ensuring a perfect crimp profile. Statistical process control complements this by offering continuous monitoring and data analysis to predict and prevent potential quality issues. This approach ensures that ring terminals consistently meet stringent quality standards, reflecting their reliability and robustness. The quality of terminal crimping is paramount for preventing failures and safety risks; advanced non-destructive evaluation techniques, including high-resolution imaging and automated X-ray systems, are employed to scrutinize the connections, while electrical property testing verifies that the terminals meet industry standards for resistance, current capacity, and insulation. These comprehensive testing methods aim to guarantee the reliability and longevity of electrical systems, resulting in safer and more dependable installations across various sectors.
When it comes to electrical connectivity, ring terminals play a pivotal role in ensuring reliable and safe power transmission. This article delves into the critical aspect of crimp quality testing within ring terminal manufacturing. We explore strategies to enhance crimping quality control, elucidate the significance of consistent crimp quality on the reliability and safety of electrical connections, and examine cutting-edge methods for assessing ring terminal integrity post-crimping. The focus on precision and effectiveness in this process is paramount, as it directly influences the performance and longevity of electrical systems across various industries.
- Optimizing Crimping Quality Control in Ring Terminal Manufacturing
- Understanding the Impact of Terminal Crimp Consistency on Reliability and Safety
- Advanced Techniques for Assessing the Integrity of Ring Terminals After Crimping
Optimizing Crimping Quality Control in Ring Terminal Manufacturing
In the realm of electrical connections, ring terminals serve as critical components for ensuring reliable and safe power transmission. To optimize crimping quality control in ring terminal manufacturing, it is imperative to integrate advanced testing methods that assess the integrity of each connection. These tests typically involve mechanical, electrical, and sometimes even environmental assessments to guarantee the crimp’s durability under various conditions. By employing high-resolution cameras and precision gauges, manufacturers can closely monitor the crimping process in real-time, identifying inconsistencies or deviations from the optimal crimp profile. This meticulous approach helps in maintaining consistent quality across large production volumes, which is essential for applications ranging from industrial machinery to consumer electronics.
Furthermore, incorporating statistical process control (SPC) into the manufacturing workflow allows for continuous monitoring and adjustment of the crimping process parameters. This ensures that the ring terminals produced are within the specified quality standards. Advanced analytics software can analyze data collected from the crimping equipment to predict potential issues before they occur, enabling proactive measures to correct the process. By focusing on automation and data-driven decision-making, manufacturers can significantly reduce the risk of substandard products reaching end-users, thereby upholding the reputation of ring terminals as reliable and robust electrical connectors.
Understanding the Impact of Terminal Crimp Consistency on Reliability and Safety
When it comes to electrical connections, the integrity of the terminal crimp is paramount for both reliability and safety. Consistency in the crimping process of ring terminals directly influences their performance over time. A well-executed crimp ensures that the connection is secure, with minimal risk of loosening or corrosion, which can lead to electrical failures or even hazardous situations. The impact of crimp consistency extends beyond mere functionality; it encompasses the entire lifecycle of the electrical component. Inconsistent crimping can compromise the structural integrity of the terminal, leading to potential failure under load and posing a significant safety risk.
To guarantee optimal performance, stringent quality testing protocols are essential. These tests measure various parameters such as the force applied during the crimp, the diameter and length of the crimped area, and the overall structural alignment of the terminal with the conductor. Advanced technologies like X-ray fluorescence (XRF) can detect inconsistencies in material thickness that might not be visible to the naked eye. By adhering to these rigorous testing standards, manufacturers can produce ring terminals with a higher degree of reliability and safety, ensuring that connections remain intact under varying conditions and over extended periods, thereby safeguarding both equipment and personnel from potential electrical incidents.
Advanced Techniques for Assessing the Integrity of Ring Terminals After Crimping
In the realm of electrical connections, ensuring the integrity of ring terminals after crimping is paramount for both safety and performance. Advanced techniques in assessment have been developed to evaluate the quality of the crimp connection on ring terminals. These techniques include high-resolution imaging that captures the intricate details of the crimped joint, allowing for a thorough examination of the solder fillet shape, size, and consistency. This non-destructive evaluation method provides a clear visual indication of any inconsistencies or defects that could compromise the connection’s reliability. Additionally, automated X-ray systems are employed to inspect internal geometry and identify issues such as voids, solder bridges, or insufficient solder volume. These advanced methods not only enhance quality control but also contribute to the overall longevity and dependability of electrical systems by ensuring that ring terminals meet stringent industry standards.
Furthermore, electrical property testing further substantiates the robustness of the crimp connection. Parameters such as resistance, current-carrying capacity, and insulation resistance are measured to confirm that the ring terminal’s performance aligns with specifications. These tests are critical in verifying that the connection can withstand environmental factors and operational stresses over time without degradation or failure. The integration of these sophisticated testing techniques ensures a high level of quality control for ring terminals, ultimately leading to safer and more reliable electrical installations across various industries.