Comprehensive Guide to Maintaining and Inspecting Ring Terminals for Optimal Safety and Functionality
Ring terminals are robust connectors critical for secure and durable electrical connections in indu…….
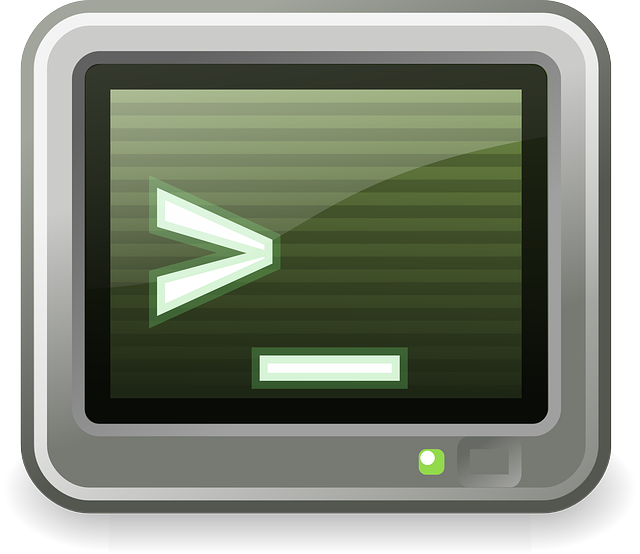
Ring terminals are robust connectors critical for secure and durable electrical connections in industrial and heavy-duty applications. These components are built with resilient materials like brass or stainless steel to endure environmental factors and resist corrosion. A spring mechanism inside ensures a stable connection, while the copper alloy head provides optimal conductivity for high current loads. The terminals feature protective insulation that guards against contamination and damage. Maintenance is paramount for their longevity; it includes regular inspections to detect wear, corrosion, or physical harm that could impact the integrity of electrical systems. Proper upkeep involves tightening with lock washers and set screws to prevent loosening due to vibration. Adhering to maintenance guidelines, visual checks for signs of degradation, and applying protective coatings as necessary are essential practices to maintain the performance and extend the lifespan of ring terminals. Compliance with safety standards such as those set by the National Electrical Code (NEC) and Occupational Safety and Health Administration (OSHA) is crucial for ensuring the reliability and safety of these components in various industrial sectors, thereby preventing potential hazards and safeguarding operational integrity. Regular maintenance and thorough inspections are not just best practices but mandatory for compliance and safe electrical operations involving ring terminals.
Ring terminals are pivotal components in electrical systems, ensuring secure and reliable cable connections. This comprehensive guide delves into their anatomy and functionality, setting the stage for a detailed exploration of maintenance best practices, inspection techniques, and troubleshooting common issues. From understanding the intricacies of ring terminals to ensuring adherence to safety standards, this article equips you with the knowledge to maintain and inspect your equipment effectively. Whether you’re an electrician, engineer, or a professional in the field of electrical maintenance, mastery of these practices is essential for optimal performance and safety.
- Understanding the Anatomy and Functionality of Ring Terminals
- Best Practices for Regular Maintenance of Ring Terminals
- Step-by-Step Guide to Visual Inspection of Ring Terminals
- Troubleshooting Common Issues with Ring Terminals
- Ensuring Compliance with Safety Standards and Regulations in Ring Terminal Use and Maintenance
Understanding the Anatomy and Functionality of Ring Terminals
Ring terminals are robust connections used in electrical systems to provide a reliable and secure way to terminate conductors, often used in industrial and heavy-duty applications. A close examination of their anatomy reveals a series of components that work in concert to ensure efficient performance. The fundamental structure includes a brass or stainless-steel body, designed for durability and resistance to environmental factors such as corrosion and wear. This body houses the internal spring mechanism, which is crucial for maintaining a firm connection under varying conditions and repeated use.
The terminal’s head, typically made of copper alloy for superior electrical conductivity, makes contact with the conductor, forming an electrical interface that can handle high current loads without degrading performance. The insulation around the head protects the connection from contamination and mechanical damage. Additionally, the ring terminal’s design often incorporates a lock washer and set screw to prevent loosening during vibration or movement, ensuring a consistently secure fit within the device or apparatus it serves. Understanding these components and their roles is essential for maintaining ring terminals, as this knowledge facilitates effective inspection and maintenance practices, thereby extending their operational life and ensuring consistent electrical performance. Regularly inspecting ring terminals for signs of wear, corrosion, or damage is a critical step in safeguarding the integrity of electrical systems where they are employed.
Best Practices for Regular Maintenance of Ring Terminals
Regular maintenance and inspection are critical for ensuring the reliable operation of ring terminals, which serve as crucial connections in electrical systems across various industries. To maintain the integrity and longevity of ring terminals, adhering to a few key best practices is essential. Firstly, establish a routine maintenance schedule based on the manufacturer’s recommendations and the specific conditions in which the terminals operate. This proactive approach helps identify potential issues before they lead to system failures or safety hazards.
During each maintenance interval, conduct a thorough visual inspection of the ring terminals to check for physical damage, corrosion, or signs of overheating. Any abnormalities should be addressed promptly. Additionally, verify that all connections are secure and that the terminal settings match the design specifications. Use appropriate cleaning methods to remove any accumulated dirt, grime, or oxidation, as these can compromise the connection integrity and electrical performance. Applying a protective coating, if recommended by the manufacturer, can further safeguard against environmental factors that may degrade the terminals over time. By consistently following these best practices, you can significantly reduce the risk of failure in ring terminal applications, ensuring consistent and safe electrical performance.
Step-by-Step Guide to Visual Inspection of Ring Terminals
Ring terminals are critical components in electrical systems, serving as the point of connection between cables and various apparatuses. Regular maintenance and inspection are paramount to ensure their longevity and reliability. A visual inspection is a fundamental step in this process, allowing for early detection of potential issues before they lead to larger problems or system failures.
To perform a thorough visual inspection of ring terminals, begin by examining the physical condition of the terminal. Look for any visible signs of damage such as cracks, deformation, or corrosion. The connections should be tight and secure; if there is any looseness, it must be addressed to prevent electrical disconnection or overheating. Inspect the terminal’s insulation for any cuts, abrasions, or wear that could expose the conductive elements. Pay close attention to the areas where the cable enters the terminal, as this is a common point of failure due to stress and moisture ingress. Ensure that there is no excessive strain on the cable that could lead to premature wear or damage. After assessing the physical integrity, check for proper alignment and that the terminals are correctly positioned within their respective housings. Lastly, verify that there is no foreign material, such as dirt or debris, that could cause an impedance in the connection or create a conduction path for noise or ground loops. Regular visual inspections, coupled with a systematic maintenance program, will help maintain the integrity of ring terminals and contribute to the overall safety and performance of the electrical system.
Troubleshooting Common Issues with Ring Terminals
When maintaining ring terminals, proactive troubleshooting is essential to prevent malfunctions and extend their service life. Common issues with ring terminals can stem from improper installation, environmental factors, or wear and tear over time. To address these challenges, it’s crucial to regularly inspect the terminal connections for any signs of looseness, corrosion, or damage. Loose connections can be tightened according to the manufacturer’s specifications, ensuring a secure and conductive interface. Corrosion is a frequent problem that can impede electrical flow; it can be mitigated by cleaning the terminals with a wire brush and applying an appropriate protective coating or anticorrosive compound.
Environmental factors such as high humidity or exposure to chemicals can accelerate corrosion and degrade ring terminals. It’s imperative to assess these conditions regularly and take corrective measures, like sealing the terminals or using environmentally resistant materials. Additionally, monitoring the terminal’s resistance and continuity with a multimeter is a good practice to ensure they are functioning correctly. By identifying and addressing these issues promptly, maintenance personnel can avoid more complex problems that might arise, thereby ensuring the safety and reliability of electrical connections in various applications where ring terminals are used. Regular maintenance schedules and thorough inspections are key to maintaining the integrity of ring terminal installations.
Ensuring Compliance with Safety Standards and Regulations in Ring Terminal Use and Maintenance
Regular inspection and maintenance of ring terminals are paramount to ensure safety and compliance with industry standards and regulations. These components, which connect electrical wires to devices or systems, are subject to environmental factors and wear over time, making routine checks indispensable. Employers must adhere to the National Electrical Code (NEC) and Occupational Safety and Health Administration (OSHA) guidelines, which stipulate the necessary procedures for maintaining and inspecting ring terminals. These protocols include visual inspections to identify any signs of corrosion, overheating, or damage that could compromise their integrity. Any deviation from optimal condition necessitates immediate corrective action to prevent potential accidents. Regular upkeep not only aligns with safety regulations but also extends the lifespan and reliability of the ring terminals, ensuring they perform safely under expected operating conditions. It is imperative for personnel responsible for maintenance to be thoroughly trained in these standards to effectively carry out inspection tasks and maintain a safe working environment for all personnel involved. By keeping abreast of regulatory changes and incorporating best practices into the maintenance routine, organizations can safeguard their operations from electrical risks associated with poorly maintained ring terminals.