Choosing the Right Ring Terminal: A Guide to Types and Applications
Ring terminals serve as pivotal components in electrical connections, ensuring robust and secure wi…….
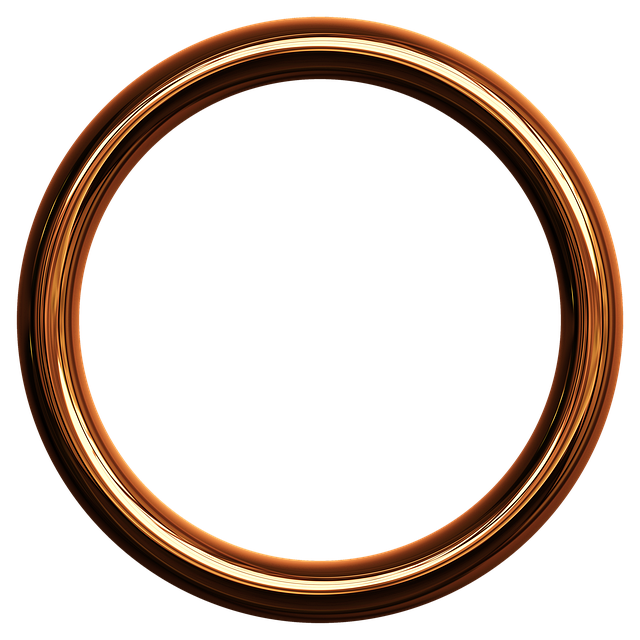
Ring terminals serve as pivotal components in electrical connections, ensuring robust and secure wire terminations. This article delves into the multifaceted world of ring terminals, from their fundamental functions to the diverse types available. We explore the material differences between copper and aluminum ring terminals, a critical choice that affects both performance and longevity. Additionally, we investigate the extensive applications of these terminals across various industries, underscoring their importance in a wide range of settings. Whether you’re an engineer seeking to select the optimal ring terminal for your specific application or a user aiming to understand the factors influencing this choice, this comprehensive guide offers valuable insights into the selection process.
- Understanding Ring Terminals: The Basics and Types
- Copper vs. Aluminum Ring Terminals: Material Considerations
- Applications of Ring Terminals Across Industries
- Selecting the Right Ring Terminal for Your Application: Factors to Consider
Understanding Ring Terminals: The Basics and Types
Ring terminals serve as critical components in electrical connections, providing a secure and weatherproof termination for flexible cables where movement is expected or exposure to environmental factors is a concern. These terminations are designed to connect the end of an electrical cable to a conduit or enclosure, ensuring the safe and reliable transmission of electrical currents. The fundamentals of ring terminals revolve around their robust construction and versatility; they are engineered to withstand various conditions, from mechanical stress to corrosive elements.
There are several types of ring terminals available, each tailored to specific applications. Standard ring terminals consist of a conductive metal ring with an insulating sleeve that slides over the cable end. The most common metals used for these rings include copper alloy and stainless steel, chosen for their durability and conductivity. For industrial or heavy-duty use, there are high-temperature resistant versions suitable for environments where extreme heat is present. Additionally, there are locking and non-locking options; the former provides a positive lock to prevent disconnection, while the latter allows for easy installation and removal. When selecting a ring terminal, it’s crucial to consider the cable size, voltage, environmental conditions, and the mechanical stress expected during service. This ensures that the chosen terminal will perform reliably throughout its intended lifespan.
Copper vs. Aluminum Ring Terminals: Material Considerations
When selecting ring terminals for electrical or electronic applications, the choice between copper and aluminum is a significant one, influenced by material properties that affect performance, durability, and safety. Copper ring terminals are renowned for their excellent electrical conductivity, which minimizes energy loss and ensures efficient power transmission. Their high thermal conductivity also aids in dissipating heat effectively, making them suitable for applications with elevated temperatures or high currents. Additionally, copper’s inherent strength and superior corrosion resistance contribute to its longevity and reliability in various environments.
In contrast, aluminum ring terminals offer a lighter alternative without compromising on conductivity. Aluminum is about one-third the weight of copper, which can be advantageous when minimizing overall system weight or when dealing with larger cables where the weight difference becomes significant. While aluminum’s conductivity is slightly lower than that of copper, advancements in alloy compositions have narrowed this gap. Moreover, aluminum’s reflective nature can make it more resistant to oxidation compared to copper, which can be beneficial in outdoor or corrosive environments. This resistance to corrosion, combined with its natural lightweight property, makes aluminum ring terminals a favored choice for applications where weight savings are critical and environmental conditions may pose challenges. Both materials have their merits, and the decision between copper and aluminum ring terminals should be based on a careful assessment of the application’s requirements, including conductivity needs, environmental considerations, weight constraints, and budgetary factors.
Applications of Ring Terminals Across Industries
Ring terminals serve as critical interfaces in electrical connectivity, providing robust and reliable connections essential for various industries. These components are designed to protect the conductor ends within enclosures, equipment, or machinery from environmental hazards or accidental disconnection. In the realm of construction, ring terminals ensure the safety of electrical installations by securely attaching wires to conductive fittings like pipes and conduits. Within the transportation sector, they are integral to the functionality of vehicles, from automobiles to locomotives, securing battery cables and lighting systems under harsh conditions. The aerospace industry also relies on ring terminals for avionics and communication systems, where their reliability is paramount due to the critical nature of these systems in flight safety. Additionally, in renewable energy applications, such as wind turbines and solar farms, ring terminals connect electrical components exposed to the elements, ensuring longevity and performance. Across all these industries, the versatility of ring terminals makes them indispensable for both high-voltage and low-voltage electrical systems, underscoring their critical role in modern technological advancements.
Selecting the Right Ring Terminal for Your Application: Factors to Consider
When selecting the appropriate ring terminal for your application, several key factors must be taken into account to ensure optimal performance and reliability. Firstly, consider the voltage requirements of your application; ring terminals are available in various insulation levels suitable for different voltage ranges. The environmental conditions where the terminal will be used is another critical aspect. Environmental factors such as temperature extremes, moisture, and chemical exposure can degrade terminal performance if not matched with the correct material. For instance, thermoplastics like LSZT offer high-temperature resistance, while other materials may be more suited to cold or corrosive environments.
Additionally, mechanical stress and physical space constraints are important considerations. The diameter of the conductor, the type of conductor (solid or stranded), and the intended application’s movement or vibration will influence the choice between ring terminals with set screws, hex nuts, or press-fit designs. The termination’s load-bearing capacity should also be assessed; some applications may require additional support to handle dynamic loads. Lastly, the compatibility of the ring terminal with the conductor size and type is paramount to ensure a secure and conductive connection. By carefully evaluating these factors and selecting a ring terminal that meets all the specified requirements, you can guarantee a robust and durable electrical connection tailored to your unique application needs.