Choosing the Right Ring Terminal: A Guide to Materials, Sizes, and Best Practices for Durable Electrical Connections
When selecting a ring terminal for an electrical project, it's crucial to consider the wire ga…….
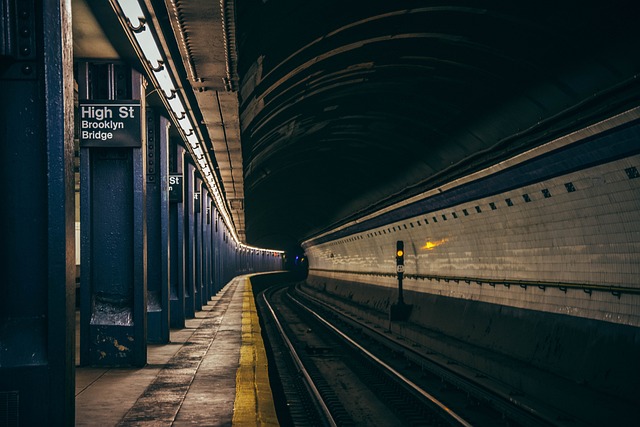
When selecting a ring terminal for an electrical project, it's crucial to consider the wire gauge compatibility, environmental conditions, and application requirements to ensure safe and efficient electrical connections. Material choices like copper alloy, aluminum, or stainless steel offer different benefits depending on whether you need high conductivity, resistance to corrosion, or durability in extreme conditions. Proper installation demands precise measurement, insulation stripping, and crimping using appropriate tools to secure the terminal to the wire without compromising conductivity. After installation, thorough visual inspections and functional tests are necessary to verify the terminal's integrity and resistance to electrical forces. Regular maintenance and environmental protection measures, such as anti-corrosive treatments, are essential for long-term reliability and performance. By carefully selecting and maintaining your ring terminal, you can ensure a durable and effective electrical connection that meets safety standards and endures over time.
When it comes to electrical connections, selecting the right ring terminal is paramount for safety, performance, and longevity. This article serves as a guide to understanding the diverse options in ring terminals, ensuring you choose the most suitable one for your specific application. We’ll delve into material selection between copper, aluminum, and stainless steel, examine size and capacity requirements relative to wire gauge and ampacity, and provide insights on quality inspection and installation best practices. Additionally, we’ll discuss strategies for maintaining your ring terminals to maximize their lifespan and maintain optimal electrical connections. With the right knowledge, you can make informed decisions that will enhance the reliability and efficiency of your electrical systems.
- Understanding Ring Terminals: A Comprehensive Overview
- Key Factors in Selecting the Appropriate Ring Terminal for Your Application
- Material Considerations: Choosing Between Copper, Aluminum, and Stainless Steel Ring Terminals
- Ring Terminal Sizes and Capacities: Matching to Wire Gauge and Ampacity Requirements
- Inspecting and Testing Ring Terminals for Quality and Compatibility
- Installation Techniques: Ensuring Proper Application of Ring Terminals
- Maintenance and Longevity: Maximizing the Lifespan of Your Ring Terminal Investment
Understanding Ring Terminals: A Comprehensive Overview
When selecting the appropriate ring terminal for your electrical project, it’s crucial to consider the specific application requirements and environmental conditions the connection will face. Ring terminals serve as the endpoint for insulated copper conductors in electrical wiring, ensuring a secure and reliable connection between the wire and the terminal hardware. They are available in various sizes, materials, and configurations to suit different gauges of wire and diverse environments, ranging from domestic to industrial applications.
The material choice for ring terminals is a significant factor, as it influences both performance and longevity. Common materials include copper alloy, aluminum, and stainless steel, each offering distinct advantages. Copper alloy provides excellent conductivity and durability, making it a popular choice for general use. Aluminum offers a lighter weight alternative with good conductivity, often preferred in applications where weight reduction is important. Stainless steel is resistant to corrosion, which is essential in harsh or wet environments. Additionally, the type of ring terminal—straight, right-angle, teardrop, or locking—must align with the intended use, whether it’s for a control panel, a piece of equipment, or an outdoor installation. Understanding the specific needs of your application will guide you to select the right ring terminal for optimal electrical performance and safety.
Key Factors in Selecting the Appropriate Ring Terminal for Your Application
When selecting the appropriate ring terminal for your application, it’s crucial to consider several key factors that will ensure both functionality and safety. The first factor is the cable size and gauge; ring terminals must be compatible with the wire they are intended to connect. The diameter of the wire affects the choice of terminal to prevent poor connections or potential damage to the conductor. Additionally, the type of application—be it industrial, commercial, or residential—dictates the level of durability and environmental resistance required from the ring terminal. For example, terminals used in outdoor settings need to withstand harsh weather conditions, necessitating materials that offer superior corrosion resistance, such as stainless steel or aluminum alloys.
Another vital aspect is the electrical requirements of your application. The voltage and current specifications must be within the rating range of the ring terminal to prevent overheating and potential fires. Moreover, the physical environment where the terminal will be used also plays a role in selection. This includes considering factors such as temperature extremes, exposure to chemicals or solvents, and mechanical stress. For instance, terminals used in high-temperature environments may require special insulation or materials that maintain integrity under heat. Similarly, if the terminal will be subjected to frequent vibrations or movements, a robust design with secure locking mechanisms will be necessary to prevent loosening or disconnection.
By carefully evaluating these factors and matching them with the right ring terminal, you can ensure a reliable electrical connection that meets both your application’s needs and safety standards. It’s also advisable to consult manufacturer specifications, industry standards such as IEC or ANSI, and to seek guidance from professionals when in doubt. This due diligence will help you choose the most suitable ring terminal for your specific project.
Material Considerations: Choosing Between Copper, Aluminum, and Stainless Steel Ring Terminals
When selecting a ring terminal, one of the primary considerations is the material type. Each material—copper, aluminum, and stainless steel—offers distinct advantages that make them suitable for different applications. Copper ring terminals are renowned for their excellent electrical conductivity, making them an ideal choice for applications where high electrical currents are involved. Their robust mechanical properties also ensure a secure connection, which is crucial for long-term reliability in various electrical systems. Aluminum ring terminals, on the other hand, provide a lighter alternative to copper, which can be beneficial in reducing the overall weight of an electrical circuit without significantly compromising on conductivity. Additionally, aluminum’s natural resistance to corrosion and its thermal conductivity make it a preferred option for outdoor or harsher environments where copper might oxidize over time. Stainless steel ring terminals are a robust choice, especially in settings that demand high resilience against environmental factors like saltwater or industrial chemicals. Their durability and resistance to rust and corrosion ensure a long service life, even under extreme conditions. When choosing between these materials, it’s important to consider the specific requirements of your application, including the electrical load, environmental conditions, and the expected lifespan of the connection. The right material for the ring terminal not only ensures a reliable connection but also contributes to the overall efficiency and longevity of the system. Ring terminals are a critical component in electrical installations, and selecting the correct one can significantly impact the performance and safety of the entire setup.
Ring Terminal Sizes and Capacities: Matching to Wire Gauge and Ampacity Requirements
When selecting the appropriate ring terminal for an electrical project, it is imperative to consider both the wire gauge and the ampacity requirements to ensure a safe and reliable connection. Ring terminals are designed to securely fasten the end of a wire to a conductor such as a bolt or nut. The right match between the ring terminal size and the wire gauge is crucial for maintaining the integrity of the electrical circuit, as a mismatch can lead to overheating, potential fires, or even system failure.
Firstly, the American Wire Gauge (AWG) or the comparable gauge system in metric (mm2) must be taken into account. The size of the ring terminal should correspond with the wire gauge it will connect to; typically, a larger gauge wire requires a larger ring terminal. This is to ensure that the wire’s electrical current can safely pass through without exceeding the wire’s ampacity—the maximum current the wire can carry without degradation. Ampacity requirements are determined by factors such as the type of wire insulation, the environmental conditions the wire will be exposed to, and the length of the wire run. It is important to consult electrical codes and standards like the National Electrical Code (NEC) to adhere to these specifications. By choosing a ring terminal with an ampacity rating that meets or exceeds the wire’s ampacity, you can safeguard against overloading and ensure a long-lasting, efficient connection. Always refer to manufacturer specifications to find the correct ring terminal for your specific application, ensuring both safety and performance excellence in your electrical projects.
Inspecting and Testing Ring Terminals for Quality and Compatibility
When selecting a ring terminal for an electrical application, it is imperative to conduct thorough inspections and tests to guarantee both quality and compatibility with the specific use case. Initial visual assessments should be performed to ensure that the ring terminals exhibit no signs of damage or defects. Attention must be paid to the material’s integrity, including the metal contacts and insulating elements, as these are critical for maintaining electrical continuity and preventing corrosion and overheating. Furthermore, resistance tests are essential to confirm the terminals’ conductivity. They should meet or exceed industry standards for the desired application, ensuring a reliable connection under various environmental conditions.
In addition to visual and resistance testing, insulation resistance and dielectric strength tests are vital to assess the ring terminal’s performance under voltage stress. These tests help determine the quality of the insulating material and its ability to withstand electrical forces without failure. Compatibility with the system’s voltage requirements is paramount, and the ring terminals should be rated accordingly to prevent potential risks associated with overvoltage conditions. By adhering to these rigorous testing protocols, users can select ring terminals that are not only suitable for their specific electrical needs but also safe and durable under real-world operating conditions.
Installation Techniques: Ensuring Proper Application of Ring Terminals
When it comes to the proper application of ring terminals, installation techniques play a pivotal role in both the functionality and longevity of electrical connections. To ensure that ring terminals are applied correctly, one must adhere to specific steps during the installation process. Begin by carefully measuring the wire gauge to select the appropriate size of ring terminal; this ensures a secure fit and optimal conductivity. It’s crucial to strip the wire insulation with precision, exposing enough length for the terminal to make a solid connection without compromising the wire’s integrity. After crimping the ring terminal onto the wire using pliers designed for this purpose, such as a crimping tool or a hydraulic press, inspect the connection for any irregularities or signs of improper application. Properly installed ring terminals should be flush with the end of the wire and securely in place, allowing for safe and reliable electrical connections.
For those dealing with high-current applications, it’s essential to consider specialized ring terminals designed for heavy-duty use. These terminals may require additional steps, such as the application of an anti-corrosive compound or the use of heat shrink tubing to further insulate and protect the connection. Additionally, when working with ring terminals in environments subject to high vibration or shock loads, it’s important to ensure that the terminal is not only securely attached to the wire but also that it is mounted in a way that mitigates the risk of detachment. Regular maintenance and inspections should be part of the routine to guarantee that ring terminals remain a dependable component of any electrical system.
Maintenance and Longevity: Maximizing the Lifespan of Your Ring Terminal Investment
When it comes to maximizing the lifespan of your ring terminal investment, maintenance plays a pivotal role. Regular inspections are crucial for identifying potential issues early on. This proactive approach can prevent minor problems from escalating into major failures, thus extending the functional life of your ring terminals. It’s advisable to conduct these checks after installation and periodically thereafter, especially in environments where the terminals are subject to harsh conditions or frequent handling.
Ensuring that the ring terminals are properly secured and that all connections are tight can prevent wear and electrical contact issues. The use of anti-corrosion compounds on terminal contacts will safeguard against environmental factors such as moisture, salt, dust, and other contaminants that could degrade the terminals over time. Employing the correct ring terminal for the application, considering factors like current load, voltage, and environmental conditions, is equally important. Selecting a ring terminal with an appropriate gauge and insulation type will not only enhance performance but also contribute to its durability and longevity. Regular maintenance, coupled with using the right ring terminal for your specific needs, will significantly bolster the longevity of your investment, ensuring that it serves you reliably for years to come.